Martin Engineering unveil new impact cradle design
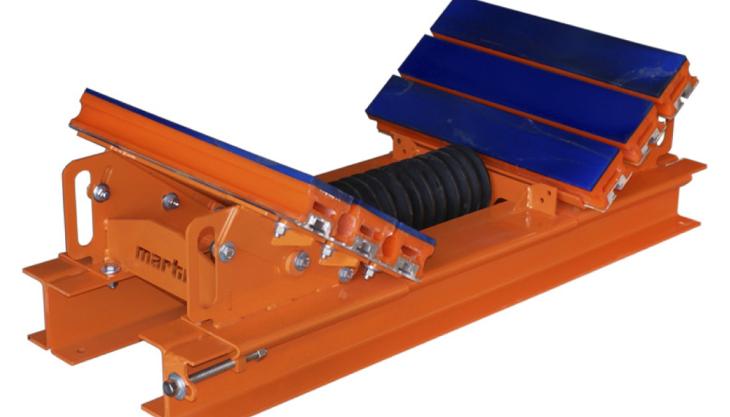
Evo Combination Cradle designed to provide better protection in conveyor loading zones
MARTIN Engineering say their innovative impact cradle design is helping bulk material handlers protect conveyor belts and structures from falling material in loading zones which, in turn, helps reduces equipment damage and downtime while stabilizing the belt line to prevent dust and spillage.
The company has unveiled its Evo Combination Cradle which features reinforced impact bars and adjustable wing supports to match standard trough angles at 20 degrees, 35 degrees or 45 degrees.
‘To minimize drag on drive motors, the cradles can be ordered with centre rollers instead of centre impact bars,’ explained Chris Schmelzer, global product manager at Martin Engineering. ‘In either style, eccentrics built into the supports also deliver five degrees of wear adjustment, so the alignment between wings and idlers can be optimized for effective transfer point sealing.’
Evo Combination Cradles are typically installed so the bars/rollers in the centre are slightly below the unloaded belt’s line of travel. This helps the belt absorb impact, but at the same time avoids continuous drag and unnecessary wear if the conveyor is running empty.
Constructed on a base of heavy formed channels to deliver long service life even under severe operating conditions, impact bars are secured with two bolts each, allowing for easy service and replacement. Evo Combination Cradles are available to fit on belts from 24-72in (50-200 cm) wide, and may have as few as four impact bars or as many as 16, depending on cradle size and centre roll option.
There are two bar constructions available and both options have steel or aluminum reinforcement, with an absorption layer and a sliding layer of UHMW polyethylene, which delivers a 0.5 coefficient of friction. The first option is manufactured with a 50 durometer SBR rubber absorption layer and has a service temperature range from -29 to 60 degrees Celsius. The second version utilizes an 83 durometer urethane absorption layer and has a temperature range between -29 and 70 degrees Celsius.
‘Conveyor downtime is extremely expensive, especially for high-speed operations,’ commented Mr Schmelzer. ‘The longer components last and the easier they are to replace, the lower the cost of ownership.’