Martin Engineering introduce the ABS
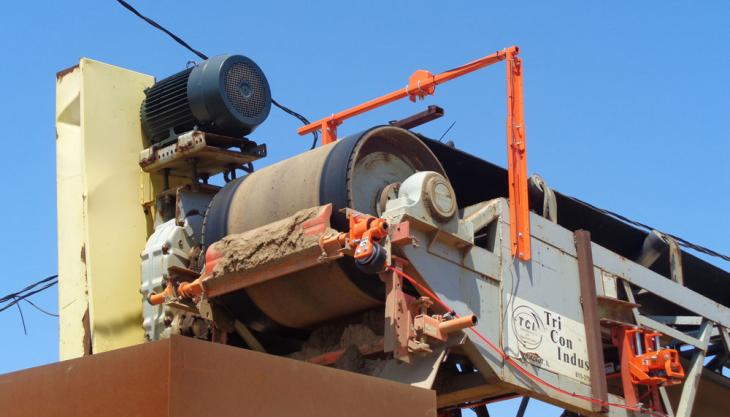
New automated pneumatic tensioning system for belt cleaners helps reduce wear and maintenance
IN a move to provide ‘smarter’ materials handling, Martin Engineering have introduced a new automated pneumatic tensioning system for belt cleaners. The Automated Blade System (ABS) is said to deliver precise monitoring and tensioning throughout all stages of blade life, reducing the labour typically required to maintain optimum blade pressure while extending the service life of both the belt and the cleaner.
Equipped with sensors to indicate that the belt is loaded and running, the system automatically backs the blade away during stoppages or when the conveyor is running empty, minimizing unnecessary wear to both the belt and cleaner. The result is consistently correct blade tension, with reduced power demand on start-up – all managed without operator intervention.
‘Pneumatic tensioners have some advantages over mechanical construction,’ said Andrew Timmerman, product development engineer for Martin. ‘Mechanical designs work well as long as they are properly adjusted, but in many cases this requires periodic attention from maintenance crews as the cleaning blade wears down.
‘Furthermore, some operators will loosen a mechanical tensioner to reduce drag at start-up, which reduces the cleaner’s performance if not correctly re-tensioned afterwards.’
The ABS can be supplied in two variants – for locations with or without an existing power source. On sites with available power, Martin Engineering offer a 120/240V AC version to power the system’s 24V compressor. Martin can also design the system so that the panel simply handles the ‘smart’ portion of engaging and disengaging the cleaner blade in facilities where power and compressed air (to the head pulley) are supplied.
For locations lacking convenient power access, the self-contained version uses the moving conveyor to generate its own electricity, which powers a small 24V DC air-compressor to maintain optimum blade pressure at all times.
Built around the patented Martin roll generator, the self-powered ABS includes a proprietary storage system developed specifically for this application. With lead acid batteries to hold the energy, the system can produce ample power to drive the compressor, which maintains pressure in the reservoir to re-tension the cleaner as needed.
According to Martin, the generator can produce as much as 40W when running at maximum speed, which is sufficient enough to run components such as weigh scales, proximity switches, moisture sensors, solenoids and relays, as well as timers, lights and safety devices. Wireless communication can be used to transmit directly to a central controller, giving operators a cost-effective way to access data that has not been readily available in the past.
When designing the new unit, Martin engineers knew they needed more power than 40W to achieve the desired function. ‘Although 40W is sufficient for low-power devices such as PLCs, sensors or LED lights, it falls short of powering high current draw devices such as compressors or actuators,’ explained Mr Timmerman.
‘So, the batteries supply the extra energy to power the compressor, which only needs to run for a brief period to maintain pressure in the reservoir. The reservoir is then regulated to keep the cleaners at proper tension. The batteries recharge during normal running of the belt to ensure they are ready to cycle again as needed.’
Both regulated power outputs can be individually adjusted to the desired pressure to tension multiple cleaners, including a single primary with as many as three secondary units.