Marshalls benefit from extensive air leak audits
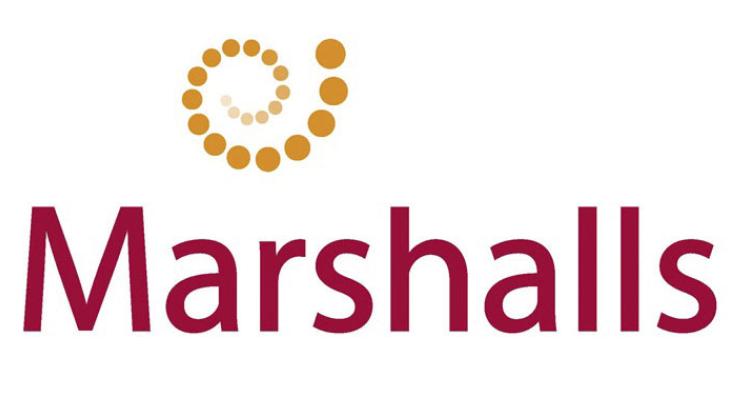
Brammer’s air-tight energy-saving solution reduces Marshalls’ carbon footprint by 426 tonnes
COMPRESSED air consumes more than 10% of all the electricity supplied to industry, but the process of compressing air can be wasteful and of the total energy supplied to a compressor, as little as 8–10% is converted into usable energy at the point of use.
Despite the high cost of production, many systems waste around 30% of the compressed air through leaks, poor maintenance, misapplication and poor control.
Marshalls, the UK’s leading hard landscaping product supplier and a major user of compressed air at the company’s numerous manufacturing operations, are constantly seeking to reduce air leakage and improve efficiency in compressed-air usage in a drive to save energy and reduce associated costs.
They therefore approached Brammer, the UK’s leading supplier of manufacturing, repair and overhaul products and services, and a supplier partner to Marshalls for seven years, to conduct a full air leak audit at their manufacturing facilities.
Brammer’s audit involved using specialist equipment to detect all air leaks, identifying each leak with a number, photographing the leaking units and specifying the appropriate parts for repair in order to make it easier for the completion of remedial work.
On completion of this stage of the process, Brammer’s engineering team worked on site to address any issues likely to hamper the remedial work and initiated alternative plans to eradicate such problems before the ‘fix’.
Nigel Cork of Brammer believes a compressed-air audit has the capability to provide immediate energy savings that could be as high as 30%. When the potential to reduce operating costs by 50% is also taken into consideration, the overall impact on the bottom line is sizable.
Explaining what is involved in a typical air leak audit, Mr Cork said: ‘It normally includes an examination of both air supply and use, and the interaction between supply and demand. The output of a compressed-air system, energy consumption in kilowatt-hours, and the annual costs of operating the system are calculated. The auditor also measures total air losses from leaks and locates those that are significant. All components of the compressed-air system are inspected individually and problem areas identified. A report is then prepared with a recommended course of action.’
Following the audit and the completion of the remedial work, Brammer are now working closely with Marshalls to lower the pressure at the compressors and to install line-side monitoring equipment so that any future leakages can be identified as soon as they occur. This will allow remedial work to be factored into a planned maintenance programme or undertaken as part of an unscheduled outage.
Peter Stevens, group carbon and energy manager with Marshalls, said: ‘Brammer and Marshalls have worked in partnership to conduct air leak audits on all major manufacturing sites within the group. This has allowed us to reduce our carbon footprint by 426 tonnes. Future work includes video tutorials for staff on better air management to achieve further savings.’