Manchester mill recycling role for Kleemann
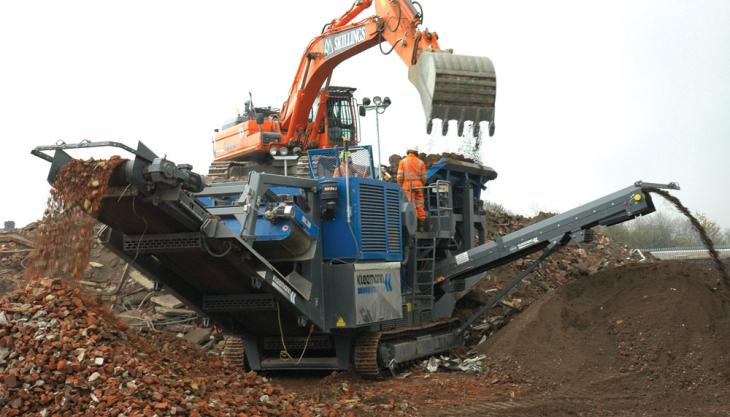
Skillings Crushing Co. Ltd, of Bury, Lancashire, have recently taken delivery of their second Kleemann track-mounted jaw crusher from Wirtgen Ltd, following the purchase last year of a similar Mobicat MC110Z machine (pictured) for use on a major redevelopment site at Chadderton, Greater Manchester.
David Skillings and his wife Jan own the North West-based company, whose plant has become a familiar sight on demolition and brownfield sites around the region. Paper and textile mills, power station turbine halls and even nuclear air-raid shelters have all featured in Skillings’ contracts, which usually involve the processing of demolition arisings for recycling. ‘Each year we typically process about 750,000 tonnes of concrete and brick,’ said Mr Skillings, who added that the two Kleemann machines have consolidated the company’s fleet and brought significant advantages to their operations. Chosen for their high productivity and operational safety, Mr Skillings says they out-perform other machines the company has owned.
‘Because the machines feature a pre-screen before the jaw crusher, you don’t have to bring a separate piece of plant on to site to screen the material before loading the crusher. They are also much quieter than comparable machines and operate with less vibration, which is an important consideration when working in urban areas. And because vibration levels are low, the machines are also very stable and easy for operators to work on, which is important in today’s health and safety conscious demolition environment.’
The company’s first Kleemann MC110Z was used to produce 75mm brick rubble at a rate of around 800–1,000m3 per day, and by the completion of the contract at the end of 2007 had processed some 30,000m3 of demolition arisings at the Chadderton site, home of a former seven-storey textile mill dating back to 1901, a former World War II hospital and, more recently, a semiconductor manufacturing unit. Material arisings from the buildings, floor slabs, foundations and a 65m high chimney were crushed and used for new roads and piling mats on the 4ha site, which is being transformed into a 120-unit residential development by Redrow Homes.
Such was the performance of the machine on this contract that Mr Skillings decided to purchase a second unit, which has recently been delivered for work on other brownfield sites in the region.
With a crusher inlet size of 1,100mm x 700mm, Kleemann’s 45–50-tonne Mobicat MC110Z track-mounted single-toggle jaw crusher is equally at home in quarrying or recycling operations. The machine’s independently vibrating double-deck pre-screen can be equipped with different meshes, according to the application. Pre-screened material can bypass the crusher or be stockpiled on either side of the machine by side discharge conveyor, giving flexibility on construction sites where space is at a premium.
A quiet, fuel-efficient 266kW diesel engine, flange-mounted hydraulic pumps and a coupled electricity generator deliver power for the crusher and electric drive for the belt, conveyors, conveying chutes and screens. A Siemens PLC control system with LCD display for manual and automatic operation, a vibration-isolated double switch cabinet housing and a built-in overpressure system, along with connections for control cable to interlock auxiliary machinery and socket outlets for 230V and 400V components, are all provided as standard.
Optional features include an electric or permanent magnetic separator and, on the 110 model, a single-deck, longitudinally tensioned, large-area vibration screen that can be hydraulically lowered for rapid mesh replacement.
Wirtgen Ltd, Reinhard House, Paving Way, Whisby Road, Lincoln LN6 3QW; tel: (01522) 889200; fax: (01522) 889222.