Layer-by-layer extraction with Wirtgen 280 SM(i) surface miner
Ash Grove Cement Company use selective extraction as an alternative to drilling and blasting
AT a quarry in Louisville, Nebraska, a Wirtgen 280 SM(i) surface miner is being used for the layer-by-layer and particularly environmentally friendly extraction of limestone from previously undeveloped reserves. Limestone for the production of cement has been quarried in Louisville since 1929.
The extraction of the material in the quarry was contracted out to North American Mining (NAM). The limestone reserves in the quarry in Louisville are by no means exhausted, even though it has now been in operation for almost 100 years. The geological situation, however, has made extraction a more difficult task, as the remaining limestone strata are interlayered with shale.
As a result, quarrying with conventional methods such as drilling and blasting would have led to contamination of the material. Ash Grove Cement Company therefore decided to use a Wirtgen surface miner from NAM for the job. As the 280 SM(i) allows selective extraction of the primary resource, it can guarantee outstanding material purity and is also a particularly suitable choice for projects in areas with sensitive infrastructures.
The 280 SM(i) cuts, crushes, and loads the extracted material in a single pass. This means that processes such as pre-crushing, or conventional extraction processes such as drilling and blasting, are no longer necessary. This not only offers significant savings in terms of costs, but also the extraction of materials in areas that are otherwise hard to access or prohibit the use of drilling and blasting due to the difficulty of obtaining appropriate permits.
The use of surface miners opens up entirely new opportunities for the extraction of limestone at the quarry in Louisville. The extraction of the material takes place in a selective, layer-by-layer process. The valuable limestone resource is cleanly separated from waste materials such as shale before crushing with extremely high output and efficiency.
Considering the limestone has a compressive strength of 110MPa, the 280 SMi achieves a mean cutting rate of approximately 400 tons/h – with 87.5% of the material produced in the process being crushed into pieces smaller than the specified maximum size of 76mm. In the waste rock (shale and overburden), the machine achieves a mean cutting rate of approximately 650 tons/h.
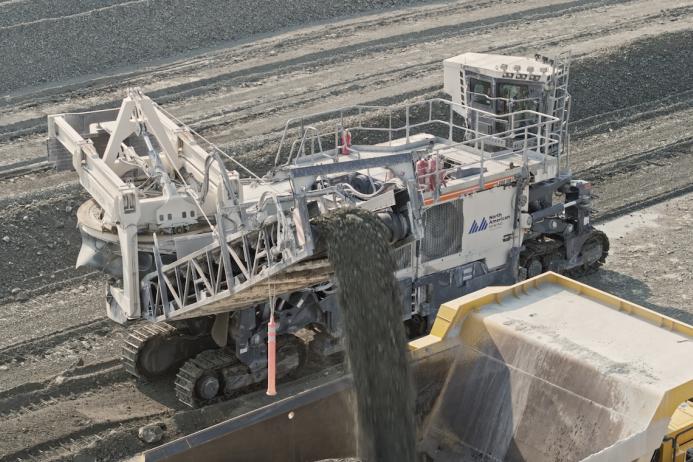
The cut and crushed material is loaded directly into 70-ton dumptrucks travelling alongside the surface miner. The process is fast and continuous, with a fresh truck being filled with crushed limestone every four minutes – around the clock, five to six days a week.
Owing to the high compressive strength of limestone, the cutting tools used are subjected to enormous stresses, however the 280 SM(i) is ideally prepared to take on the challenge and achieves maximum cutting rates with minimal pick wear.
‘The machine does a great job. I’m really impressed with the round-shank picks and the quick-change toolholder. They make it so easy to change worn picks that we can get back to work again after stopping for only a couple of minutes’, said David Ashby, machine operator from North American Mining.
He continued: ‘One of the advantages of the movable counterweight and the 90° slewing angle of the discharge conveyor is that they let you work very close to the high quarry walls. Although the machine is very big, its simply fantastic manoeuvrability makes it very useful for working in tighter spots.
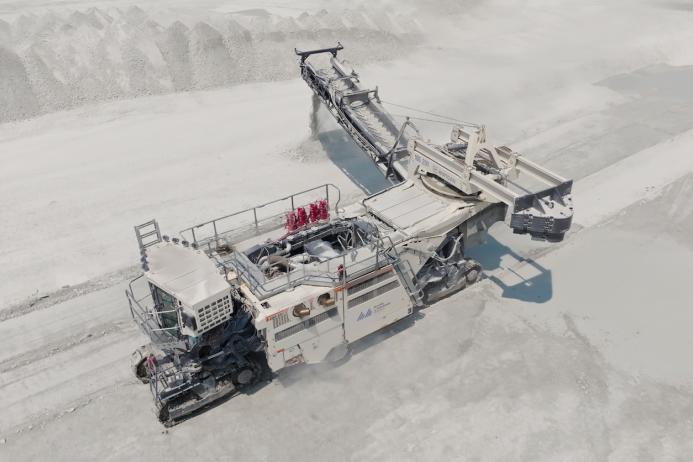
Apart from its efficiency, the machine also impresses with a range of environmentally friendly aspects: The number of extraction processes is reduced from four to one, while lower exhaust, noise, and dust emissions not only make everyday work on site much easier, but also offer new opportunities for quarrying rock close to populated areas.
‘We can now extract limestone from deposits we could hardly have reached before,’ explained Nic Haubruge, business development manager at North American Mining. ‘In many cases, the use of drilling and blasting is simply no longer a viable option, however, with this machine we can develop new deposits with minimal dust emissions, minimal noise emissions, and no vibrations.’