HOPEFlow used in construction of military homes
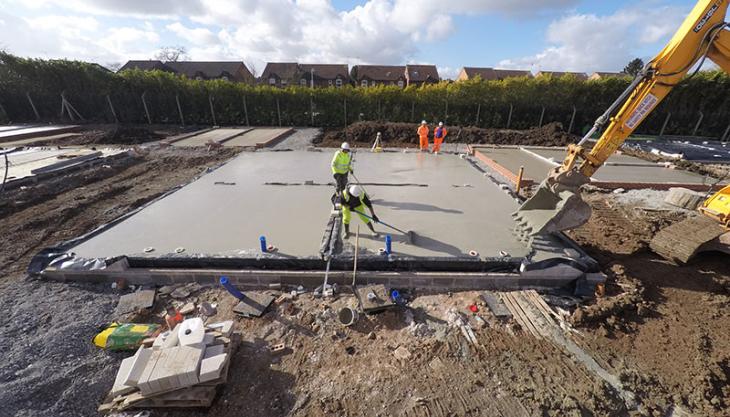
Self-compacting concrete saves time and money on Staffordshire ‘super garrison’ construction project
HOPE Construction Materials have completed the supply of 12,500 cubic metres of concrete for the construction of more than 300 new military homes in Staffordshire.
The project, which launched in August 2014, saw a total of 346 new homes built, with Hope providing the concrete slab flooring for each home, using their HOPEFlow high-performance, self-compacting concretes, to ensure that the build was completed to a stringent timescale.
Around 1,000 troops from the 16th Signal Regiment and 1st Armoured Division Signal Regiment will be housed on the Beaconside site, as part of the £51 million ‘super garrison’ development funded by the Ministry of Defence. The timber-frame housing build, the largest of its kind in Britain, is being fulfilled by social housing specialists Lovell.
Typically, a build of this size would take between three and four years, however to be able to accommodate troops returning from Germany, it needs to be completed in just 11 months.
As such, the HOPEFlow performance products were used in a bid to minimize cost and project duration, laying 20 slabs (and homes) per week as opposed to an average of four. By doing so, groundwork subcontractors Chasetown were able to save time and money, pouring the slabs without the need of power floating and reducing slab construction time by nearly 75%.
Throughout the build, Hope supplied a total of 2,500 cubic metres of HOPEFlow concrete and 10,000 cubic metres of conventional concrete from their Four Ashes and Staffordshire concrete plants, respectively, with the conventional concrete used to build the footings, drainage, curbing and road access.
Both sites are within close proximity to the Beaconsfield garrison site, ensuring that the carbon footprint of the project was kept to a minimum, in line with Hope’s sustainability targets.
Paul Coleman, area commercial manager at Hope Construction Materials, said the project highlighted a growing demand for high-quality, quick-pour products. ‘Since its launch, the HOPEFlow product has proven particularly popular and we are delighted to have used it on what was an important and substantial building initiative,’ he commented.
‘This was a large-scale project and there was a real desire to complete the build quickly and professionally, to ensure available housing when our troops return to Britain. We’re pleased that by using HOPEFlow we vastly reduced the build time of the project to get the soldiers in their homes as soon as possible.’
Kevin Pugh, contract manager with Chasetown, added: ‘We were working to particularly tight deadlines in order to ensure that the homes were ready for when the troops return home, and HOPEFlow has played a major role in being able to meet this demand due to its fast pouring time. This simply wouldn’t have been possible without it.’