Hercules trommel success in the Middle East
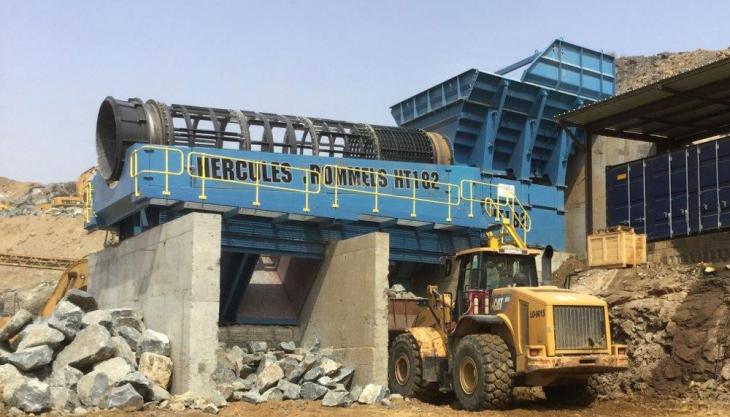
Stelex Construction Equipment supply heavy-duty HT182 static trommel to customer in Middle East
STELEX Construction Equipment Ltd, sole suppliers of the original ‘Hercules’ range of heavy-duty trommel screens, have supplied of one their HT182 static trommels to a customer in the Middle East.
Rated at 500 tonnes/h, the trommel is working with a highly aggressive feed material to produce a range of sizes for various projects in the region.
Stelex also supplied extra barrel sections for the trommel, to increase the size options available to the customer. These sections can easily be changed in and out as and when required.
According to Stelex, it would not have been possible to carry out this project with any other screening method, due to the large feed size and high tonnage rates and large product sizes required.
To this end, the company says the heavy-duty barrel sections have been subject to special manufacturing processes, to help absorb high impacts and provide a longer service life. Many of these techniques are said to be unique to the Hercules trommel.
Moreover, the 100-tonne capacity feed hopper is fitted with wear-resistant liner plates to help combat the abrasiveness of the feed material, which is loaded directly from dumptrucks.
In addition, a fines chute has been fitted under the first section of the barrel, allowing this material to be conveyed away for further processing. Extra chutes have also been used to separate the different product sizes ready for collection from bays on each side of the trommel.
Stelex say the modular design of the trommel allowed for simple installation, ensuring that the unit was up and running very quickly after delivery to site from the company’s UK factory.
The purpose-built power unit for the HT182 trommel allows the barrel rotation speed and feeder stroke rate to be changed very quickly and easily via a touch-screen panel. These parameters can be changed to suit feed material characteristics and weather conditions at different locations and at different times of the year.
The standard 20ft container used to house the power unit also provides a safe and lockable compartment for the motors, pumps and other associated hydraulic and electrical equipment.