GipoCOMBI plant for Cuddy Group
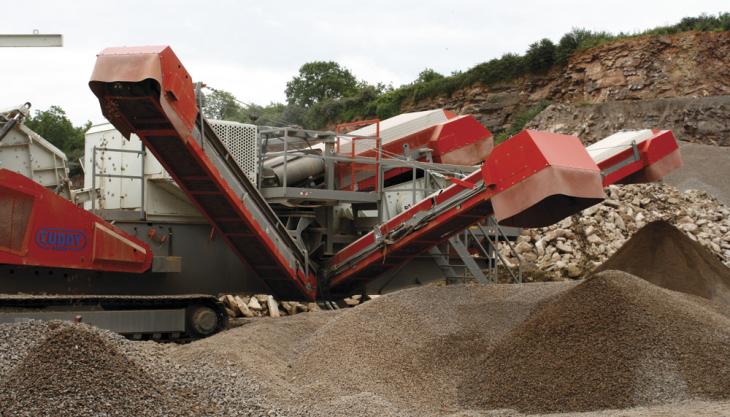
Aggregate Processing and Recycling Ltd (APR) have supplied a GipoCOMBI RC130FDR mobile crushing and screening plant (pictured) to the Cuddy Group. The machine is being used for a variety of roles, including producing single size aggregates, operating as a primary/secondary crusher and processing high tonnages of ‘as-blasted’ limestone into 0-5 and 5-25mm sizes.
The GipoCOMBI RC130FDR is a heavy-duty, highly efficient machine of compact design, which can be operated by remote control within a 200m range. The plant is driven by a Caterpillar C15 engine that develops 430kW,of which 380kW is applied to the crusher.
Featuring a dual-zone blockage release system (which can be operated remotely), the variable-speed P130 impact crusher allows maximum variance on output grading. All gap adjustments are hydraulically driven, while the crusher inlet and top apron have hydraulic lift for blockage reduction.
A variable-speed feeder supplies material to a two-deck pre-screen (with scalping at 0-40mm) and crusher bypass facility. Crusher discharge is catered for with the provision of a tray feeder as standard to absorb impact and to protect the conveyor.
Final screening of material is performed via a two-deck screen (4.5m x 2m), incorporating a 25mm aperture top deck and 5mm aperture bottom deck. The machine is also equipped with three belt weighers, two of which are on the main product conveyors and the other on the scalping belt.
To ensure optimum dust suppression, the machine is fitted with an on-board water pump system, which supplies spray bars at the crusher inlet/outlet and all conveyor heads. Other key features include aluminium covers on all conveyors and walkways and maintenance platforms around relevant parts of the machine for easy maintenance.
According to APR, the GipoCOMBI RC130FDR has major advantages over other units on the market in that it utilizes a system of combined crushing and screening in a ‘closed circuit’ to achieve maximum efficiency. With fuel consumption significantly lower in comparison with a separate crusher and screen, the machine also has the advantage of much quicker set-up and movement times than when aligning two separate units.
Another advantage is the reduction of loading and stockpile clearing activity. Once material is fed into the RC130FDR, it is contained within the machine until the process is complete, causing no extra work or fuel usage on loading shovels by handling oversize stone back to the hopper. Maintenance is well catered for as the machine has only one engine and features fewer conveyor belts than the combination of a separate crusher and screen, resulting in less risk of downtime and lower service costs.