Flexco add urethane capabilities to manufacturing process
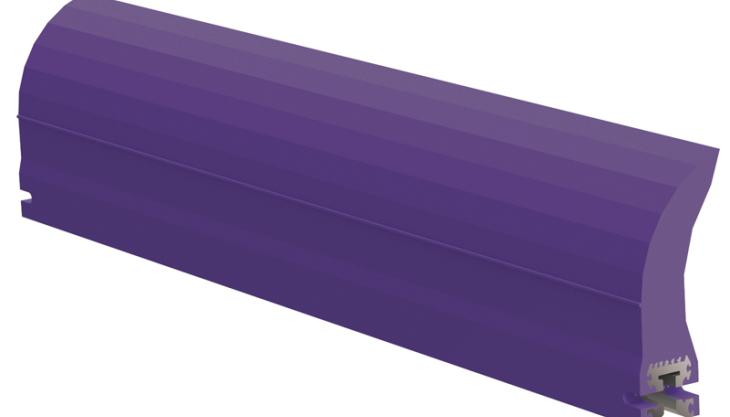
US company invests in new equipment and resources at its Grand Rapids operation in Michigan
FLEXCO have announced that their urethane belt cleaner blades are now being manufactured at the company’s Grand Rapids operation in Michigan. The recent investment in equipment and resources will give Flexco the opportunity to further develop new, innovative products.
Ryan Grevenstuk, senior product manager for Flexco, commented: ‘We spent more than a year testing over 100 formulations in the laboratory and field to ensure that we have the highest-quality urethane blades on the market. We continue to invest to ensure we’re creating products that withstand the most demanding applications.’
In-house and field tests were carried out by Flexco specialists until it was determined that the urethane blades met the company’s quality standards. The success of the blades has also encouraged Flexco to continue innovating with other customized urethane products.
‘These capabilities will speed up the time it takes to bring innovative products to the market in terms of development and delivery, continually enhancing the quality we put into every product we manufacture,’ Mr Grevenstuk added.
‘We continue to make investments in our manufacturing capabilities in the US and around the world to ensure our products can be delivered to local markets in a timely and consistent manner.’
In addition, Flexco have invested in two new side-by-side inclined conveyors to expand testing and R&D capabilities on heavy-duty products at the Michigan location. The conveyors feature a 36in wide belt with a top speed of 750 ft/min, together with an integrated belt scale and tons/h meter.
According to Carl Hessler, BCP engineering manager for Flexco, having the new conveyor loop will give engineers the capability to conduct internal testing that mirrors realistic conditions in the field and augments current laboratory, field and other conveyor testing performed on Flexco products.
‘The new conveyor system is allowing engineers to test the performance of our products in a realistic mining environment,’ he said. ‘The control we have over the test variables with this equipment allows us to investigate and understand the science behind our products, and we then use that knowledge to enhance our products’ performance and value to our customers.’