Doosan launch new DX1000LC-7 excavator
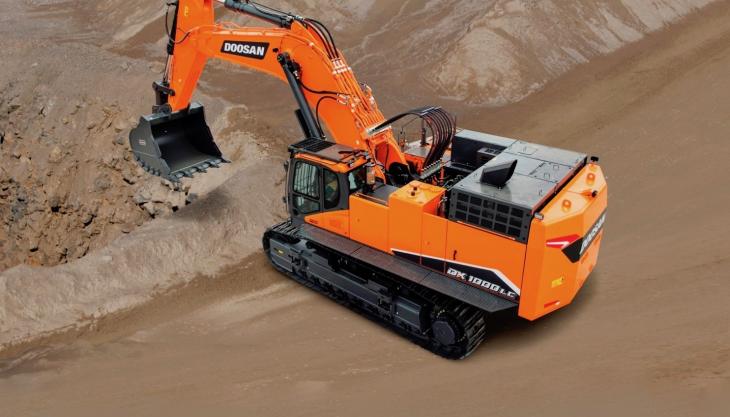
New 100-tonne machine said to offer highest power and flow with comfort and smoothness
DOOSAN have launched the new DX1000LC-7 Stage V-compliant 100-tonne crawler excavator – the largest excavator model ever manufactured by the company.
Primarily intended to serve customers in mining and quarrying applications and driven by the most powerful engine in the 100-tonne class, Doosan say the DX1000LC-7 also has the highest hydraulic flow for this size of machine, providing best-in-class performance, with higher productivity, lower fuel consumption, and smoother controls.
Like all Doosan excavators, much attention has been given to operator comfort and safety. The DX1000LC-7 has a new and spacious operator cab equipped with ergonomic controls and instrumentation, and special care has been taken to ensure noise is kept to a minimum.
All components and assemblies have been designed, built, and tested to ensure durability. Multi-stage filters and features such as track guards and cylinder guards for the boom and arm, the auto-grease system, and greased and sealed track links are designed to provide superior reliability and a long service life.
The DX1000LC-7 excavator is powered by the new stage V version of the well-proven Perkins 2806J diesel engine, providing a power output of 469kW (629hp), more than any other machine in this class. The engine meets Stage V emission regulations by utilizing exhaust gas recirculation, selective catalyst reduction, diesel oxidation catalyst and diesel particulate filter (DPF) after-treatment technologies.
The high output of the engine is combined with a Virtual Bleed Off (VBO) hydraulic system (D-ECOPOWER+) and controlled by electric manipulator (FEH), providing a best-in-class hydraulic flow of 1,569 litres/min and a high system pressure of 360 bar.
Doosan’s D-ECOPOWER+ FEH technology utilizes an electronic pressure-controlled pump within a closed-centre hydraulic system to optimize productivity and fuel consumption, depending on the mode selected. A closed-centred main control valve minimizes pressure loss, whilst the electric pressure-controlled pump manages and optimizes engine power more effectively.
Software is utilized to electronically reproduce the full benefits of an open-centre hydraulic system with very little energy loss. The hydraulic system and engine output are fully optimized and synchronized, further reducing losses within the system.
Improved feedback to the operator through the joystick results in improved machine control and less operator fatigue. The acceleration and deceleration of the excavator workgroup functions are smoother, allowing operators to perform repetitive swinging and digging motions with less jerking movements. Moreover, the operator can switch between two modes – Boom or Swing – to best match how they are using the machine to the application they are working on.
Faster working speeds are ensured by the two-spool Boom Down Regeneration system on the DX1000LC-7, which also reduces fuel consumption. The two-spool hydraulic system for the bucket cylinder also increases hydraulic flow and the working speed of the bucket, again reducing fuel consumption. In addition, the DX1000LC-7 has a boom/arm cylinder lock valve (anti-hose burst valve) as standard for increased safety, preventing accidents caused by hydraulic hose rupture on site.
Designed to significantly enhance operator comfort and ease of operation, the new cab in the DX1000LC-7 has a new high-quality seat and is said to offer more features as standard than other machine on the market. Key new features in the cab include: an 8in touch-enabled colour LCD gauge panel, providing more information on a 30% larger screen; keyless start system; full LED lighting pack; side protection and catwalks; and mandatory FOPS guard (level 2) for quarry applications.
A full camera array is standard, comprising a front camera, two side cameras, and a rear camera. The camera display is separate from the gauge panel and provides full visibility around the excavator, allowing the operator to see a top-down view of the area outside the machine. This is combined with an AVM (around-view monitoring) system as standard.
LED working lamps are also standard on the DX1000LC-7, providing up to 75% better illumination of the workspace around the excavator and the new machine is factory-fitted with the DoosanCONNECT wireless fleet-monitoring/management system.
The DX1000LC-7 also features a new heavy-duty front end with two different front combinations possible based on 7.2m (short) and 8.4m (long) booms. In addition, the counterweight design has been changed to include a horizontal mounting system that is easy to assemble/disassemble and has better durability.