Density separator increases productivity at south London recycling centre
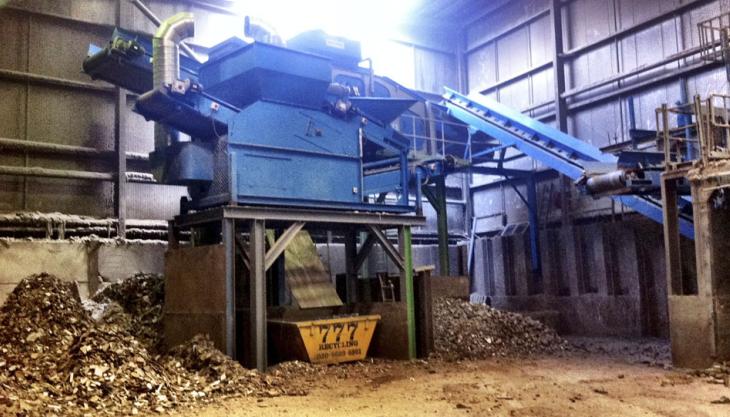
Dig A Crusher supply two Max X Tract units to 777 Recycling Centre Ltd
777 Recycling Centre Ltd, the waste management arm of one of the UK’s best-known demolition contractors, are maximizing their materials recovery operations with a pair of Max X Tract density separators supplied by Cheshire-based Dig A Crusher.
The 777 recycling centre just outside Croydon in South London features a state-of-the-art processing and extraction system that comprises multiple levels of screens, trommels and manual picking stations to extract valuable resources from the waste stream. That waste stream – a mix of construction and demolition and skip waste – arrives at the facility at a rate of more than 4,000 tonnes per week, and is converted into a wide array of products from refuse-derived fuel (RDF), ferrous and non-ferrous metals and plastics for onward processing, and a range of crushed concrete and aggregate products for reintroduction to the UK construction industry.
Malcolm Beattie, operations director, commented: ‘All of our equipment is to the highest standard and our manual picking crew were exceptionally good at ensuring that we extracted metals and other products for resale. Yet despite this, we knew that some valuable products were not being recovered quite as effectively as we would like.’
Resource extraction
The solution came in the shape of a pair of Max X Tract density separators that now form the final stage in 777 Recycling Ltd’s resource extraction process. Manufactured by Waste Systems Ltd, the Max X Tract is fully self-contained and is suited to applications that require metals to be recovered from or plastics and paper removed from bio-mass material, thereby a perceived waste product into a saleable asset.
Weighing just nine tonnes, the Max X Tract uses a one-pass system to process up to 150 tonnes/h, depending on the feed material.
At 777’s recycling centre, the first Max X Tract unit receives material from a trommel via an elevated conveyor. The first pass through the first density separator segregates the light and heavy materials; the light being destined for RDF applications, and the heavier materials moving on for further processing to the second Max X Tract. Here the final clean up occurs where wood gets separated from the aggregate ensuring two high-quality end products. The first Max X Tract effectively removes any remaining metals, both ferrous and non ferrous, from the waste stream.
According to Malcolm Beattie, this is a vital part of the process: ‘With scrap values currently at an all-time high, every ounce of metal we can extract has a value. Since we installed the Max X Tract density separators, we are recovering an additional four tonnes of metal each week on average, so the machines will pay for themselves in no time.’
Further cost savings
But the added value doesn’t end at the recovery of metals. Before the two Dig A Crusher machines were installed, 777 Recycling employed a team of 14 pickers to manually pick their way through the waste in the hope of extracting some additional value from the stream. Since the Max X Tract machines were installed, the company has been able to reduce this team to just six people, while actually increasing recovery rates.
Malcolm Beattie concluded: ‘Our pickers are very good but, ultimately, they are human and the speed with which they’re required to work to keep up with the waste inputs means they’re always likely to miss some potentially valuable materials.
‘We have no such problems with the Max X Tract machines. They’re more than capable of keeping pace with our waste inputs and they literally don’t miss a thing. The increase in our metal recovery rate speaks for itself.’
By removing the metals and aggregates the wear on the high-speed shredders has reduced by over 70 percent. Now only the RDF material goes into the high-speed shredder, giving less downtime and significant operational savings.