Danish success for Kleemann
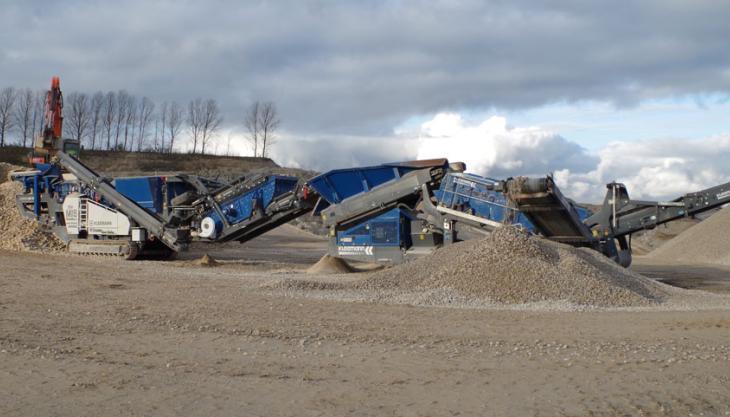
MIS Recycling A/S continue to use Kleemann crushing and screening equipment as operations expand
IN recent years the recycling market in Denmark has been booming and one waste-management firm reaping the rewards are MIS Recycling A/S, who have been actively involved in the processing of construction and demolition (C&D) waste in the past two decades.
To meet the huge demand for recycled materials in the country, MIS operate 10 impact crushing plants from Kleemann’s Mobirex series that achieve a high level of productivity. Each year, the recycling firm processes approximately 3 million tonnes of construction waste materials and 100,000 tonnes of natural stone.
The company is also heavily involved in the reprocessing of reclaimed asphalt, with the Kleemann machines crushing recycled asphalt paving (RAP) into two grain sizes: 0–6mm; and 0–20mm. The final product is returned to the asphalt production cycle.
It was important for MIS to deploy waste-processing plant and equipment that are robustly designed and offers increased productivity and higher capacity. And meeting these requirements has been the growing fleet of Kleemann crushing and screening equipment purchased by the company.
‘The high quality and robustness of the [Kleemann] plants impressed us as soon as we started using our first Mobirex 130 mobile crushing plant in 2002,’ said Martin Henriksen, director of MIS Recycling.
Since then the company has continued to invest in Kleemann products, including 10 Mobirex MR EVO2 plants and three Mobiscreen screening models, the MS 12 Z, MS 15 Z and MS 16 D.
Henrik Hvid, production manager for MIS, added: ‘The Kleemann plants last longer, are more powerful and deliver a higher quality than other crushing plants we have worked with. Service for the plants is also important for us, as we can always rely on the team from the Wirtgen Group in Denmark.’
Two of the company’s recently delivered Mobirex MR 130 Zi EVO2 mobile impact crushers are equipped with Kleemann’s Spective intuitive control system, which automates several machine functions.
Mr Henriksen commented: ‘Our operators can control all machine operations and components simply from the ground using the touchscreen panel. The flexibility of the plants is crucial for the contracting part of our business. For example, the Mobirex EVO2 plants, with their hydraulically folding hopper walls and side discharge conveyors, can be set up for operation in just 30 minutes.’