Customized EcoOperator training for Cemex site managers
SMT expand training programme to help equip site managers for lower-emission operations
ON the road to net zero, Cemex UK have partnered with SMT to implement a customized training programme designed to enhance collaboration between site managers and operators, drive immediate CO2 reductions from existing diesel machinery, and pave the way for zero-emission equipment in the future.
Cemex long understood the critical role their machine operators play in driving productivity and profitability across their sites and have consistently invested in enhancing their knowledge and skills over the years. As Cemex strive to achieve carbon neutrality by 2050, with a 2030 interim goal of reducing CO2 emissions from cement production by 47% versus 1990 levels, the company is also tapping into the potential of its operators to accelerate decarbonization – specifically through the EcoOperator programme from SMT.
‘Even with conventional diesel machines, operators can implement techniques to improve efficiency and reduce emissions, laying the groundwork for a seamless transition to zero-emission equipment, powered by renewable energy or hydrogen power in the future,’ said Kevin Cage, head of UK aggregate operations at Cemex.
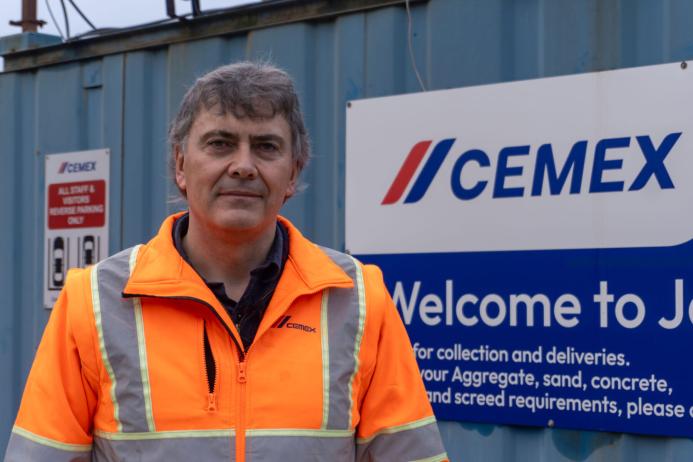
Recognizing, however, that operators can only reduce emissions so far without the right support from others in the organization, Cemex UK challenged SMT, the exclusive dealer of Volvo Construction Equipment (Volvo CE) in Great Britain, to develop a version of EcoOperator training tailored to site managers.
EcoOperator training is an advanced programme designed to deepen experienced operators’ awareness and understanding of how they can contribute to greater sustainability. Combining theory with practical exercises, EcoOperator training provides operators with the motivation and skills to directly reduce emissions through lower fuel consumption. It also focuses their attention on minimizing machine wear and tear, which decreases the carbon footprint associated with the manufacture and distribution of replacement parts.
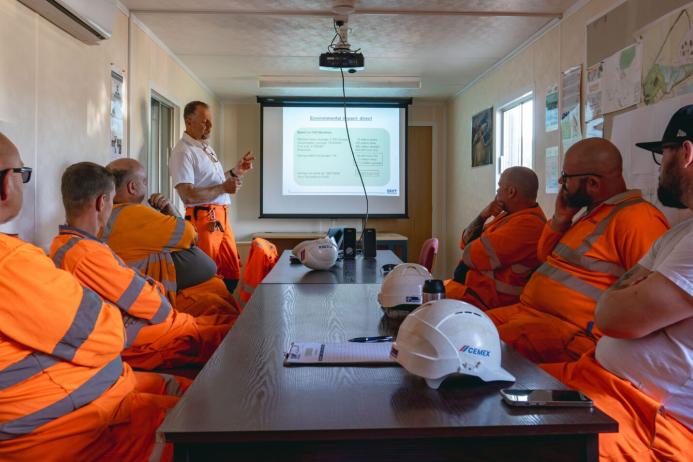
‘EcoOperator training typically results in fuel-efficiency improvements of around 5%, and while that might seem modest, the impact is substantial,’ explained Richard Cannon, operator training manager at SMT.
‘Given that each litre of diesel consumed emits 2.63kg of CO2, based on a study of 7,500 machines operating 2,000h annually with an average fuel consumption of 15 litres/h could save 11 million litres of fuel and reduce CO2 emissions by 30,000 tonnes per year – equivalent to eliminating the carbon footprint of 1,395 flights between Stockholm and Paris.’
The new site manager version of the programme developed for Cemex focuses on helping managers to understand and interpret machine telematics data, facilitate more efficient fleet and site setups, and establish appropriate targets, so they can support operators in achieving their maximum potential for emissions savings.
‘When managers understand the goals we’re trying to achieve with the operators, it significantly enhances the effectiveness of the entire programme. It’s much easier when everyone is on the same page,’ said Kevin Cage.
Giving an example of the co-operation required, Richard Cannon added: ‘While it’s widely acknowledged that excessive machine idling wastes fuel, setting overly strict idling targets, for instance, might inadvertently encourage operators to bypass the necessary engine cool-down process, risking costly damage to the turbocharger. In this case, the training would help site managers to establish a more realistic idling target for improving fuel efficiency while maintaining machine health.’
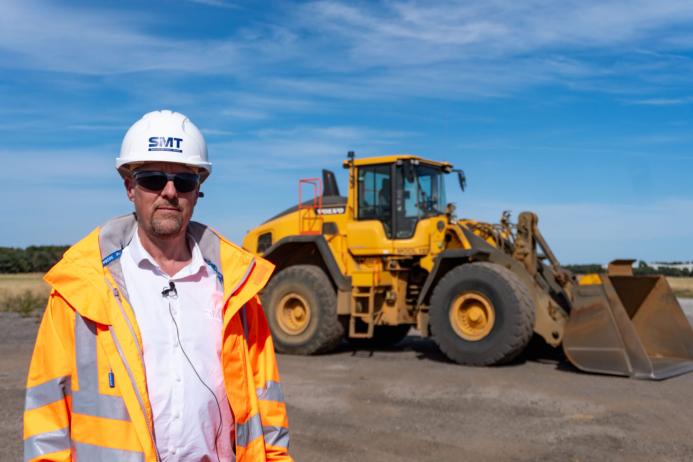
To ensure that the techniques learned in the EcoOperator training are effectively implemented and that progress is sustained, SMT will collaborate closely with Cemex by analysing machine telemetry data and identifying any further opportunities for improvement.
‘At SMT, we share the Cemex team’s commitment to reducing CO2 emissions and we’re proud to be at their side on this important journey,’ said Mr Cannon. ‘Whether through additional training or new technologies, we’ll continuously monitor and refine our approach to help them along the way.’
Expressing his satisfaction with the partnership, Kevin Cage concluded: ‘We’ve been really impressed by SMT’s readiness to listen, adapt, and develop training tailored to our specific needs. In this regard, SMT have proven to be a valued partner in our decarbonization efforts, demonstrating true collaboration in helping us to achieve our sustainability goals.’