Construction ‘game-changer’ from CCP
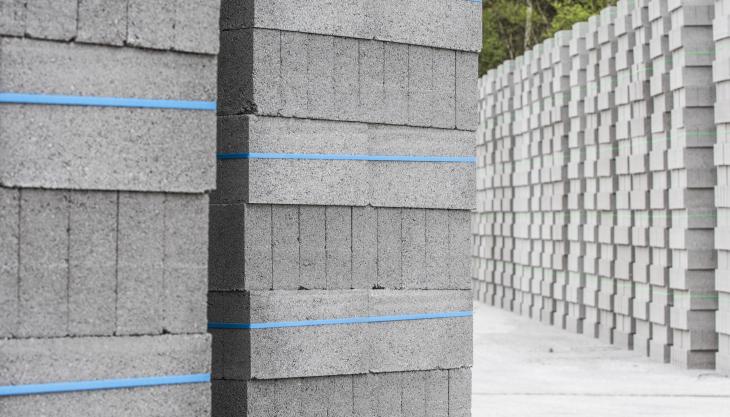
UK’s first cement-free ultra-low-carbon concrete block launched by SigmaRoc’s PPG platform
CCP, part of SigmaRoc plc’s Precast Products Group (PPG), have today launched the first cement-free ultra-low-carbon concrete block, which promises up to 77% eCO2 savings compared with traditional concrete blocks.
The new sustainable concrete block – Greenbloc – is an ultra-low-carbon alternative to traditional cement-based concrete blocks and is designed to help reduce the construction industry’s dependency upon cement – the world’s third highest source of man-made CO2 – as a key ingredient in concrete manufacturing.
Greenbloc, which is being made immediately available, is a high-density load-bearing concrete block made from Class 1 aggregates and Cemfree – a totally cement-free alternative to conventional concrete.
Manufactured to BS EN 771 – 3: (2011) and complying with Part E of the Building Regulations for Walls and Floors, Greenbloc is manufactured, stored and placed in the same way as conventional concrete blocks. With no compromise on strength compared with ordinary Portland cement (OPC) blocks, it is suitable for all applications, including foundations, load-bearing walls, internal leaves of cavity walls and partition walls.
PPG managing director Michael Roddy commented: ‘Greenbloc is a game-changer for the construction industry. Up until now sustainability has all too often been focused on operating carbon emissions post-build, rather than the carbon generated during the build schedule and in the manufacture of building materials.
‘Greenbloc is an important step in the greening of both construction projects and the wider supply chain, as it has the capability to reduce CO2 by up to 77% on a project compared with OPC. In short, the only difference to OPC is that Greenbloc has the ability to dramatically reduce CO2.’
Concrete has long been regarded as a key building material despite the fact that its manufacturing process is one of the world’s largest emitters of CO2. CCP’s own figures suggest that, for an average three-bedroom house, OPC accounts for almost 3.7 tonnes of CO2.
In comparison, Greenbloc accounts for just 981kg of CO2 for the same house, achieved through a saving of 1kg of CO2 per block and adding up to a total saving of 2.7 tonnes of CO2 per house.
Data from the National Energy Foundations suggests that switching to Greenbloc is the equivalent of offsetting the electricity emissions on an average three-bedroom house for an entire year.
Mr Roddy continued: ‘As a building material, cement cannot be matched; however, it remains the source of about 8% of the world’s carbon dioxide emissions. Greenbloc offers the construction industry a clear path to a more sustainable future, decreasing the carbon footprint of one of its core building products and the projects it is used in.’
Max Vermorken, chief executive officer of SigmaRoc, commented: ‘Our Greenbloc range and brand is the brainchild of our innovation and technical teams. It addresses a key challenge in the building products industry, the embodied CO2 in one of the most widely used building materials: the concrete block.
‘Greenbloc is only the start of a range of sustainable alternatives to our product offering as we invest, improve, integrate and innovate.’