CEMEX and Coolbrook to electrify cement production
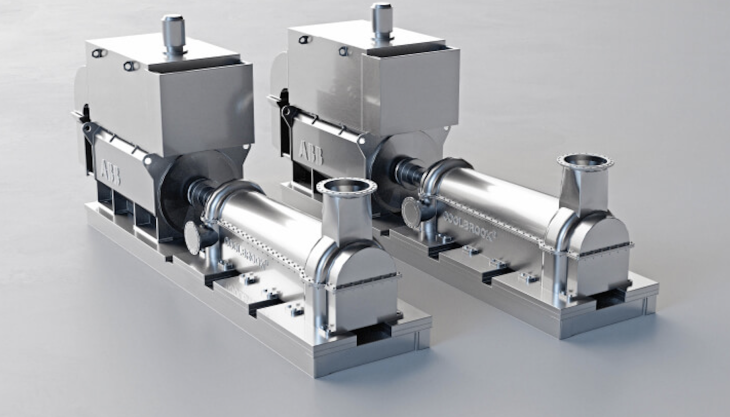
Finnish-Dutch company signs MoU to explore electrification of cement kiln heating process
CEMEX are set to work with Finnish-Dutch company Coolbrook to test their patented, innovative technology which uses electricity in place of fossil fuels in the heating process during cement production. Fossil fuels used to heat the kilns account for approximately 45% of the carbon emissions in cement production.
The two companies have signed a Memorandum of Understanding to combine their expertise to develop optimal electric process heating solutions that can be applied in the cement manufacturing process.
Coolbrook’s Roto Dynamic Heater (RDH) technology aims to revolutionize cement production by replacing the fossil fuels traditionally used to heat the kilns with electricity. RDH technology is able, using electricity alone, to heat kilns to a high enough temperature (around 1,700C) to produce cement with state-of-the-art materials.
When powered by electricity from renewable sources, the technology eliminates CO2 emissions from the fuels used in the heating process and is seen as an important development in the eventual decarbonization of the industry.
‘The electrification of the heating and calcination process of cement production is an important step towards decarbonizing our cement operations,’ said Roberto Ponguta, CEMEX’s vice-president of global operations, technical and energy. ‘To the extent that we can use electricity from renewable sources, we can eliminate carbon emissions related to the heating of cement kilns.
‘We are constantly looking for the best technologies and most promising partnerships to meet our climate action targets and our collaboration with Coolbrook is another example of this.’
Coolbrook executive chairman Ilpo Kuokkanen added: ‘We have set a target to build a comprehensive ecosystem around our revolutionary technology and to test its use in as many industrial processes as fast as possible. Together with CEMEX, we can bring the technology to cement production and achieve significant emission reductions in one of the most energy- and CO2-intensive industrial processes.’
The companies plan to jointly evaluate the best production site to test and develop the ground-breaking technology and expect it to be ready for commercial use at an industrial scale in 2024.