CDE washing plant for Tooperang Quarry
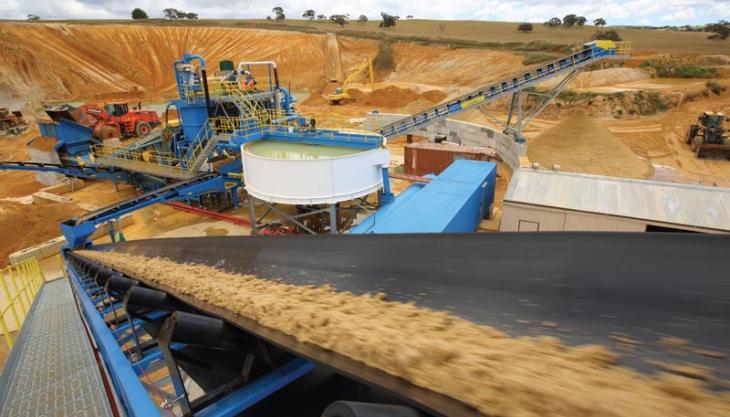
M2500 washing plant employed to process silica sand for use by Australian wine bottle manufacturer
TOOPERANG Quarry has announced the completion of a silica sand washing plant at a new site near Adelaide, South Australia. The plant has been supplied by CDE and is producing glass sands for use by Owens-Illinois (O-I) at their glass bottle manufacturing plant in Adelaide.
The new turnkey plant includes a range of equipment from the CDE product portfolio including the M2500 with integrated counter-flow classification unit (CFCU), EvoWash fines recovery system, fine sand screens, attrition cells and spirals. The plant configuration also includes an AquaCycle thickener which reduces the volume of fresh water required to feed the washing plant by more than 90%.
The design feed rate to the plant is 100 tons per hour and this produces 50 tons per hour of glass sand with an additional 30 tons per hour of concrete sand. The plant accepts –120mm feed to the M2500 hopper; this material is transferred to the integrated ProGrade double-deck rinsing screen. The top deck removes the –120mm +40mm material to a stockpile while the bottom deck sends the –40mm +7mm material to another stockpile.
The 0–7mm material collects in the ProGrade sump and is pumped to a five-deck fines screen. At this point the silica sand is screened at 0.43mm and the –7mm +0.43mm is sent to a separate EvoWash sand washing plant to allow for the production of concrete sand. Meanwhile, the –0.43mm material is sent to an EvoWash fines recovery plant where, following delivery to the EvoWash sump, the material is pumped to the integrated hydrocyclone which removes the –63 micron material. The cyclone overflow containing the waste material is sent to the AquaCycle thickener.
The underflow from the cyclone is delivered to the EvoWash dewatering screen before being transferred to the attrition cells, which assist with the removal of iron oxide and other deleterious materials from the silica sand. The iron oxide which adheres to the silica particles must be scrubbed from the surface of the particles to allow removal later in the process.
Refractory heavy minerals and iron oxide particles are then separated from the silica sand through the introduction of spiral classifiers. As these particles have a higher specific gravity than the silica sand particles, the spirals are able to perform the required separation. The rejects from the spirals – a sand product containing the liberated heavy mineral and iron oxide – is delivered to the EvoWash sand washing plant sump and is destined for the concrete sand product. The silica sand slurry is delivered to the sand sump on the M2500 from where it is pumped to the integrated CFCU
The CFCU unit is used to remove the –106 micron particles from the sand as required by the specification. The CFCU is an upward-flow classifying unit which operates on the principle that an upward flow of water will cause the lighter particles to rise and the heavier particles to sink. This facilitates the removal of any remaining fines while the silica sand slurry is delivered to a dewatering screen. The dewatered silica sand is transferred via an integrated stockpile conveyor, while the fine material removed by the CFCU is sent to the EvoWash for recovery into the concrete product.
From an initial iron oxide (Fe2O3) content in the feed of 0.3%, the glass sand is required to achieve 0.25% Fe2O3 in line with O-I’s sand specification for coloured glass. The final product has less than 0.1% iron oxide, ensuring that it meets the specification required by the Adelaide plant.
‘We are achieving the 0.1% figure consistently which is as important as achieving the reduction in the iron content,’ explained CDE project manager Chris McKeown.
Both the dewatered silica sand and concrete sands are subsequently stockpiled using 26m radial conveyors which ensure a stockpile capacity of 5,000 tons. From an initial silica content of 93% for the as-dug material the final product achieves +99% silica.
Waste water from the plant is processed by the AquaCycle thickener which recovers 90% of the water for recirculation around the washing plant. The plant requires 400 cubic metres per hour of water for its operation and the introduction of the AquaCycle ensures that the top up water supply is only 40 cubic metres per hour. The sludge from the AquaCycle thickener is pumped to on-site settling ponds.
The glass sands produced by Tooperang Quarry are used at O-I’s Adelaide plant in West Croydon, which produces mainly wine bottles for Australia’s renowned wine industry.
Following successful completion of the project, CDE have obtained preferred-supplier status with O-I to support future sand processing requirements. O-I procurement director David Abela said: ‘The achievement of a consistent sand specification at Tooperang Quarry, in accordance with our requirements, proves CDE’s silica sand processing capabilities.
‘CDE also delivered the project in a very professional manner through their project-management system and it is for this reason that we will continue to work with CDE to investigate glass sand supply opportunities in other parts of Australia.’