Caterpillar launch new 986K wheel loader
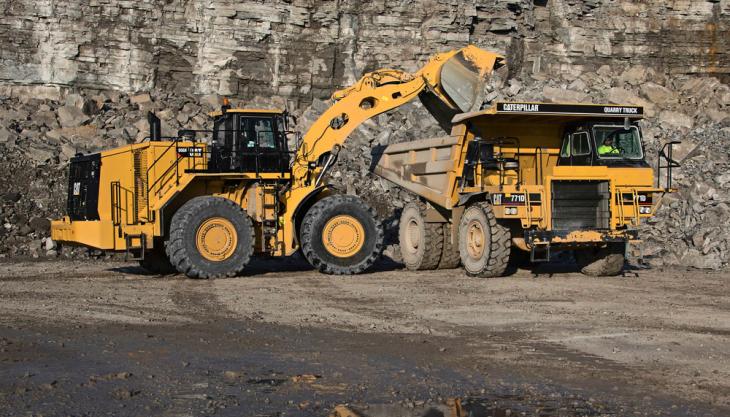
New loader said to deliver significant efficiency increase for low cost-per-tonne operation
COMBINING reliable, efficient loading with multiple lives, the new Caterpillar 986K wheel loader features a completely redesigned state-of-the-art cab equipped with Cat Production Measurement, bringing payload weighing to the cab so operators can work more productively and deliver accurate loads with confidence.
Weighing less and being shorter than the Cat 988K loader, the new 986K loader serves as a replacement for the legacy 988F model, offering a low cost-per-tonne loading option that is well matched to Caterpillar’s 36- to 55-tonne articulated and rigid-frame dumptrucks. Its new Aggregate Handler configuration includes an 8.3 cubic metre bucket (12.7-tonne payload) and additional counterweight for high-volume loading in fewer passes.
The new 986K wheel loader features Cat STIC steer, which combines directional selection, gear selection and steering into a single joystick. For repetitive tasks, such as loading trucks, the joystick control requires significantly less operator energy compared with steering wheel control, thereby helping to reduce fatigue and increase productivity.
With its standard and high-lift linkage options, the Cat 986K offers four-pass loading of Cat 740 and 745 articulated haulers and 770 rigid-frame trucks, whilst the high-lift configuration offers five-pass loading of the Cat 772 and six-pass loading of the 773 rigid-frame truck.
Meeting US EPA Tier 4 Final (EU Stage IV) emissions standards, the highly responsive Cat C15 ACERT engine delivers a net power rating of 373hp (278kW), while the loader’s Auto Engine Idle Shutdown maximizes fuel efficiency by reducing engine idle time. Load-sensing hydraulics enhance the machine’s performance and efficiency by directing hydraulic fluid flow through the implement and steering systems only when needed.
The loader’s completely redesigned cab improves operator comfort, safety and productivity. Access is via left- or right-hand stairs built at a reduced 45° angle, whilst the STIC steer armrest easily folds up to allow quick and easy operator entry to the cab. Isolation cab mounts and an air-suspension seat help reduce vibration for increased operator comfort, while the enclosed, pressurized and sound-suppressed structure reduces in-cab noise levels.
The ergonomic placement of switches and information displays helps ensure comfortable, productive loader operation, while the simple, intuitive control interface with touch-screen display allows even less-experienced operators to quickly learn machine functions and operation. In addition, large front and side windows, plus a standard rear-vision camera, offer excellent visibility of the working area to improve operational safety.
The integrated electronics on the new 986K wheel loader provide flexible levels of information for both the operator and company. The loader comes complete with Cat Production Measurement (CPM), said to be the most advanced payload weight measuring system on the market. Offering quick, on-the-go weighing of material in the bucket, CPM allows operators to manage target payload by minimizing under-loading and overloading, which reduce efficiency and increase fuel consumption.
Moreover, Cat Product Link takes the guesswork out of loader management and maximizes uptime by offering remote monitoring through VisionLink. With its easy-to-navigate user interface, VisionLink tracks machine utilization, fuel usage and payload summaries, giving key company personnel access to valuable reports, analysis and histograms to improve fleet management. Scheduled service event reminders and fault code alerts can also be sent to key service and management personnel to improve machine uptime availability.
Reducing downtime and long-term operating costs, the 986K wheel loader features extended service intervals for both fluids and filters. Grouped service points are quickly and safely accessed from ground level or a platform, whilst swing-out doors on both sides of the machine provide unobstructed access to the engine compartment for the servicing of components.
Grease fittings for difficult-to-reach components are conveniently grouped to provide quick preventative lubrication, whilst an optional autolube will automatically inject grease into linkage pin joints at regular intervals. The machine’s electrical service centre, accessed from ground level, includes remote jump-start, main and engine circuit breakers, emergency engine shutdown, stairway light switch, and battery disconnect.