Belt drive alignment and tensioning made easy
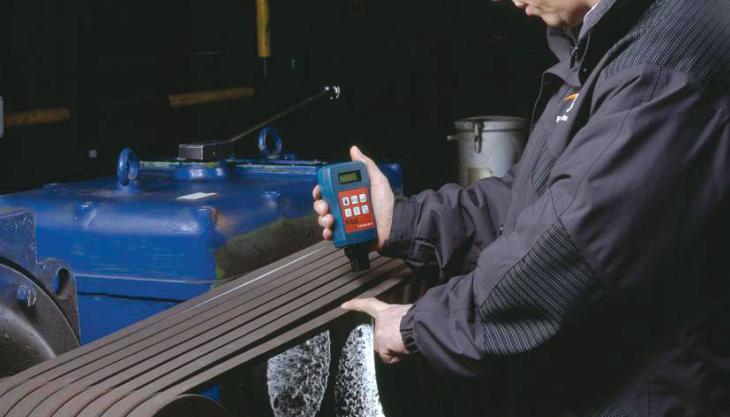
FAG Industrial Services (F’IS), the maintenance and condition monitoring division of the Schaeffler Group, have extended the range of functions offered by two of their measuring instruments – Smarty2 and Trummy2 – used for aligning and tensioning belt drives and chain sprockets.
The new digital functions, say F’IS, not only ensure the precision instruments are more accurate and easier to use, but also help reduce wear and tear on the drive components.
Correctly aligned and tensioned belt drives or chain sprockets result in less friction and vibration generated by the drive system, which, in turn, leads to
less wear on belts, belt pulleys, bearings and seals. As a result, the running time and reliability of the machinery is increased, energy costs are kept to a minimum and overall plant efficiency is improved.
Suitable for checking the alignment of belt-driven fans, compressors, conveyors, pumps and ventilators, the FAG Top-laser Smarty2 is said to measure and adjust the alignment of drives and pulleys significantly faster and more accurately than conventional methods.
Featuring a new, optional real-time digital display of readings, Smarty2 shows the parallelism and misalignment of both pulleys, and is appropriate for both horizontally- and vertically-mounted machinery. Designed for use on flat, toothed and Vee belts, the device detects angular/parallel misalignment, or a combination of the two.
When operating Smarty2, the user can clearly see the laser beam on the target marks. Adjusting the laser beam to coincide with the slots in the target marks means machinery is correctly aligned. As the instrument is lightweight (270g), the emitter and target marks can be attached to non-magnetic drive pulleys using strong, double-sided adhesive tape.
As well as alignment, correct belt tension is a prerequisite for maximizing the working life of belt drives. The FAG Top-Laser Trummy2 is a high precision, opto-electronic hand-held instrument for optimizing belt tension (strand force).
Measurement parameters are shown in the display either as frequency (Hz) or force (N), and the device’s enhanced design now allows users to perform measurements using only one hand.
To calculate the optimum strand force for a drive, the belt mass and length are entered into the instrument. By generating an impulse, such as striking the stationary belt, the tensioned belt is excited to its natural vibration.
The individual static natural frequency generated is then measured in seconds by a sensor using ‘clock pulse light’ and shown on the display. The strand force is calculated and compared with the specified nominal value.
According to F’IS, clock pulse light technology is far more advanced than conventional methods (eg measurements using sound waves) because the measurement result is not distorted by disruptive external influences.
Schaeffler (UK) Ltd, Forge Lane, Minworth, Sutton Coldfield, West Mids B76 1AP; tel: (0121) 351 3833; fax: (0121) 351 7686.
The new digital functions, say F’IS, not only ensure the precision instruments are more accurate and easier to use, but also help reduce wear and tear on the drive components.
Correctly aligned and tensioned belt drives or chain sprockets result in less friction and vibration generated by the drive system, which, in turn, leads to
less wear on belts, belt pulleys, bearings and seals. As a result, the running time and reliability of the machinery is increased, energy costs are kept to a minimum and overall plant efficiency is improved.
Suitable for checking the alignment of belt-driven fans, compressors, conveyors, pumps and ventilators, the FAG Top-laser Smarty2 is said to measure and adjust the alignment of drives and pulleys significantly faster and more accurately than conventional methods.
Featuring a new, optional real-time digital display of readings, Smarty2 shows the parallelism and misalignment of both pulleys, and is appropriate for both horizontally- and vertically-mounted machinery. Designed for use on flat, toothed and Vee belts, the device detects angular/parallel misalignment, or a combination of the two.
When operating Smarty2, the user can clearly see the laser beam on the target marks. Adjusting the laser beam to coincide with the slots in the target marks means machinery is correctly aligned. As the instrument is lightweight (270g), the emitter and target marks can be attached to non-magnetic drive pulleys using strong, double-sided adhesive tape.
As well as alignment, correct belt tension is a prerequisite for maximizing the working life of belt drives. The FAG Top-Laser Trummy2 is a high precision, opto-electronic hand-held instrument for optimizing belt tension (strand force).
Measurement parameters are shown in the display either as frequency (Hz) or force (N), and the device’s enhanced design now allows users to perform measurements using only one hand.
To calculate the optimum strand force for a drive, the belt mass and length are entered into the instrument. By generating an impulse, such as striking the stationary belt, the tensioned belt is excited to its natural vibration.
The individual static natural frequency generated is then measured in seconds by a sensor using ‘clock pulse light’ and shown on the display. The strand force is calculated and compared with the specified nominal value.
According to F’IS, clock pulse light technology is far more advanced than conventional methods (eg measurements using sound waves) because the measurement result is not distorted by disruptive external influences.
Schaeffler (UK) Ltd, Forge Lane, Minworth, Sutton Coldfield, West Mids B76 1AP; tel: (0121) 351 3833; fax: (0121) 351 7686.