Atlas Copco upgrade 8-Series compressors
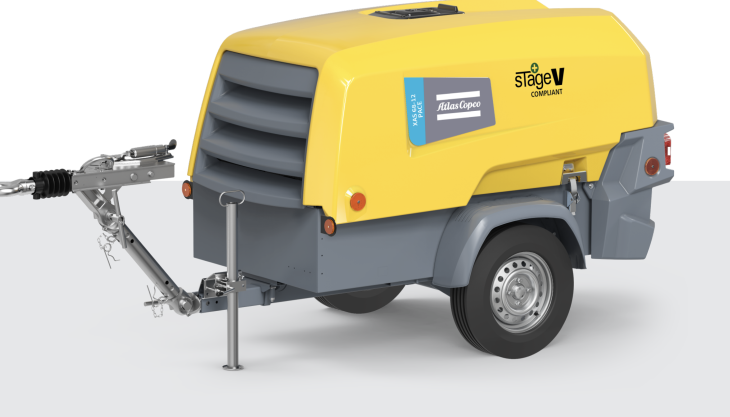
Stage V-compliant air compressors optimized for improved fuel efficiency and increased performance
IN response to upcoming regulation, Atlas Copco have upgraded their 8-Series air compressor range. In addition to greener operation, the compressors now feature innovative new technologies that help cut operating costs and improve productivity, with 25% less fuel consumption.
The updated 8-Series consists of 11 models, some with built-in generators, ranging from the XAS 38-7 with free air delivery of 2 cubic metres per minute to the XAS 88-7 with free air delivery of 5 cubic metres per minute. Models in this range also feature a corrosion-free, strong and durable HardHat hood.
Thanks to Atlas Copco’s pioneering air element design, most of the compressors weigh under 750kg and have a footprint approximately 10% smaller than other similar models on the market. Beneficially, being light in weight, they can be towed behind a normal passenger car without any special driving license, simplifying operation and reducing cost.
Also, some of the compressors are now equipped with advanced control panels to simplify management and improve efficiency. Six models in the range have either an XC1004 controller or an even more sophisticated XC2003 controller. The basic XC1004 introduces an electronic controller for models that would otherwise only have gauges.
The XC1004 controller allows for easy, smooth and safe operation while avoiding downtime, as service requirements are clearly visualized, whilst the XC2003 controller introduces applications such as PACE and ECO-mode.
PACE (pressure adjusted through cognitive electronics) allows users to easily select the required pressure from a wide range, while the flow adjusts automatically to suit the needs of the application. The XAS 68-12 PACE, for example, can handle a pressure range from 5–12 bar.
ECO-mode reduces the cost associated with running compressors in idling mode during downtime, such as when changing parts in machinery or moving equipment to new locations on site, thereby helping to boost fuel efficiency.
Traditionally, when in idling mode, the compressor switches to no-load mode: even though no air is required, the compressor is still running and consuming fuel. When ECO-mode is activated, however, the 8-Series compressors automatically switch from no-load to unload mode, reducing fuel consumption by a further 50%.
This translates into significant savings, as fuel consumption typically accounts for around 80% of the operating costs of a compressor. Crucially, utilizing ECO-mode does not delay productivity, as once work is ready to resume, the compressor is back up and running in seconds.
Despite their light weight and compact design, the upgraded 8-Series air compressors are designed to operate reliably in the harshest environments. Atlas Copco’s patented HardHat canopy provides protection against the elements and its plastic casing is resistant to corrosion and cracks, allowing it to endure arduous operations on site.
Finally, to further enhance uptime, the compressors have a service interval of 1,000 hours and can be fully serviced in less than 60 minutes, without any special tools.
‘We wanted to take this opportunity to engineer further efficiencies into this range to help our customers meet the upcoming regulations and improve their operation in the process,’ said Rodolfo Reimberg, vice-president of marketing for portable compressors and tools at Atlas Copco. ‘This range gives users better control over their energy consumption, helping them achieve a more cost-efficient, sustainable and productive way of working.’