Asphalt Burner Services install burner at Shap
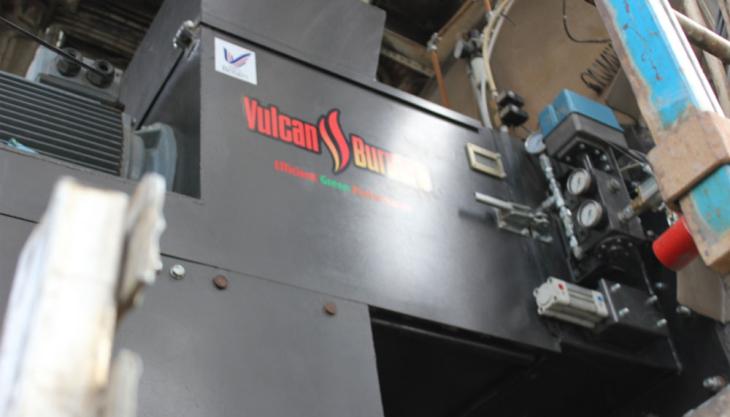
CEMEX select Vulcan burner for Marini asphalt plant in Cumbria
Asphalt Burner Services (ABS) have installed a Vulcan burner at CEMEX’s asphalt plant in Shap, Cumbria.
Although a relatively new plant, operating since 2009, a new burner installation was required. The result since installation of the Vulcan burner show that fuel usage is reduced, emissions lowered and the overall plant performance has increased substantially. The Vulcan burner range comes with innovative features that raise the standards for asphalt production.
ABS have spent years on the Vulcan range, researching the optimum performance. Features include: excess air control, combustion chamber optimization and air pressure compensation, which are said to be unique to the Vulcan range. The design concept delivers energy savings in excess of 20%, whilst the high-efficiency compact burner design is easily accessible for servicing which is a major benefit for any service engineer.
Carbon monoxide (CO) emissions at the dryer exhaust duct have been recorded averaging across three test points at unprecedented low levels of 45ppm with the burner set at 30% output. ABS say that this is exceptional as the target levels normally experienced on good asphalt plant burners are anything between 200ppm and 400ppm. CO in flue gases are an indicator of the efficiency of the burning process, the higher concentration of CO present equates to unburnt fuel in the process. The undiluted carbon monoxide (uCO) was averaging at 150ppm, again levels of the uCO are normally recorded on other asphalt plant burners at levels of 400-900ppm.
The Vulcan burner is successfully burning 100% of Nexgen 3 fuel oil; which has been fitted on a four-year-old Marini 200-280 tonnes/h asphalt plant at Shap Cumbria for CEMEX UK Ltd. Initial tests indicate the fuel costs have been significantly reduced from 9 litres/tonne to just over 6.5-7 litres/tonne, with an additional saving in carbon tax due to the overall performance of the new burner.