Aggregate Industries go the extra green mile
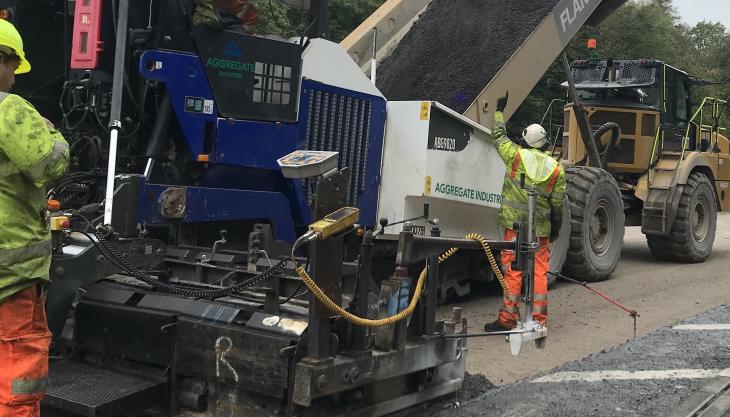
Company’s contracting division completes the UK’s first carbon-neutral pavement scheme
AGGREGATE Industries’ contracting division has made history by completing the UK’s first carbon-neutral pavement scheme as part of Highways England’s A590 M6 J36 to Brettargh Holt resurfacing project.
Now complete, the road improvement project included full-depth resurfacing of the dual carriageway between junction 36 of the M6 and the Brettargh Holt roundabout, along with the roundabout at junction 36. This forms part of the estimated £8 million A590 scheme to ensure safer, smoother journeys for road users on this vital route in south Cumbria.
Heavily trafficked, the old surface had come to the end of its life with dangerous potholes and uneven surfacing posing a safety risk for drivers. Hence, Highways England’s objective was to ensure the new road was constructed quickly and safely with minimum disruption to the local road network.
The project came with highly ambitious carbon-reduction targets, which drew heavily upon Aggregate Industries’ expert technical credentials and value engineering approach help to achieve the UK’s first carbon-neutral road improvement project.
Working in collaboration with principal contractors AE Yates and designers Amey, at the early contractor involvement stage – more than 18 months before the contract began – Aggregate Industries’ national technical manager, Neil Leake, recommended an innovative Foamix approach.
This pavement design option meant that the structural layers of the existing road surface were recycled and encapsulated back into the pavement by producing an ex-situ cold-recycled asphalt, which, when combined with the use of Aggregate Industries’ recently launched range of SuperLow asphalt, helped to achieve a carbon-neutral pavement construction.
As the only carbon-neutral asphalt available in the UK, SuperLow technology ensures reduced carbon levels compared with standard asphalt, due to it being manufactured at lower temperatures.
To ensure continuous and consistent production of Foamix material, a dedicated SiteBatch mixing plant was installed on site, supported by a fleet of articulated dumptrucks to deliver the material and return the extracted planings.
This approach ensured maximum efficiency and saw the team working 24 hours a day across two shifts and laying more than 1,000 tonnes of Foamix asphalt per night, ensuring minimum disruption to the local area whilst keeping ahead of all key deadlines.
Aside from the benefit of improved circular economy and significant reductions in CO2 in the mixing process, working in this way negated the need for truck movements and waste disposal costs, significantly improving the sustainability aspects of the project and resulting in a 43% carbon reduction compared with conventional resurfacing methods.
Moreover, in an industry first, through the company’s partnership with Circular Ecology (a non-profit organization), Aggregate Industries purchased a number of credits to offset the remaining carbon on the scheme.
With Aggregate Industries’ advanced site operating procedures ensuring that construction could safely take place through the COVID-19 pandemic, in total some 50,000 tonnes of material was extracted from the original pavement and 38,887 tonnes recycled over the course of just six weeks.
This included 11,607 tonnes of asphalt and 27,280 tonnes of Foamix laid using 8m wide pavers. Meanwhile, around 20,000 tonnes will be reused on the A590 Cross-a-Moor roundabout scheme and the strategic road network.
Guy Edwards, chief executive officer at Aggregate Industries UK, said: ‘As the world’s first building materials supplier to commit to hitting net-zero emissions by 2050, completing the UK’s first carbon-neutral pavement scheme is a landmark achievement for us and demonstrates our commitment to achieving this goal.
‘By working collaboratively with Highways England, AE Yates and Amey on the A590 M6 J36 to Brettargh Holt scheme during the early contractor involvement stage, we were able to identify a low-carbon approach designed to provide significant environmental and, in turn, cost benefits by establishing a best-practice approach to greener road surfacing.
‘Looking forward, as we continue to work more closely together as an industry and utilize our expanding range of eco-friendly products and services, we can start to make a real difference when helping to deliver essential infrastructure projects.’