ABB gearless conveyor drive for wider range of motors
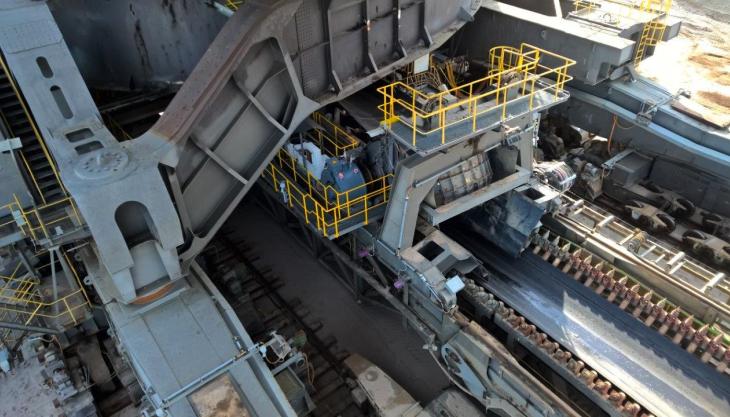
Innovative solution improves reliability, saves energy costs and reduces overall maintenance costs
ABB have announced that their gearless conveyor drive is now available for use on a wider range of conveyor systems. Already proven on larger motors, the newest drive is designed for medium power range motors (1 to 3MW per motor) to make this technology economically feasible for a broader range of conveyor systems.
The new solution, which can be applied to both greenfield and brownfield systems, is said to significantly decrease the cost threshold for gearless conveyor technology.
According to ABB, fewer parts and new motor technology increase the reliability and efficiency of the overall conveyor system. A permanent magnet motor specifically designed for mining applications is a core element of the system, contributing to its reliability and ability to perform in the most challenging environments.
The gearless conveyor drive system eliminates the gearbox from the drive, thereby reducing the number of main wear parts, so less maintenance is needed, and lengthening the lifespan of the equipment. ABB say the expected lifespan for the drivetrain increases by more than 10 years, compared with traditional geared systems, to a projected in-service life of 25 years.
Other advantages include a considerable reduction in the drive system’s footprint, less weight, and a reduction in the instrumentation required to operate the system. The gearless drive design is also more energy efficient, requiring less power, and operates more quietly, thus reducing noise emissions.
In July 2017, a pilot project utilizing this solution was conducted in collaboration with Lausitz Energie Bergbau AG (LEAG) in their Jänschwalde open-pit lignite mine, near Cottbus, in Germany. The new gearless solution was installed on the high-capacity (15,000 tonnes/h) discharge conveyor of a bucket-chain excavator in parallel with the existing geared drive. Both drives were connected to the same pulley shaft to allow for exact benchmarking.
According to LEAG, the gearless solution has performed better with regard to dynamic accuracy and overall efficiency than the existing traditional solution.
They say the operational data demonstrates the advantages of the gearless solution with fewer components. The gearless solution is more reliable (with a 50% lower failure rate) and requires less maintenance. It also meets eco design and energy-performance requirements according to international standards, to support mine site’s environmental approvals and certification. It also consumes 5% less energy than the other drive.
‘LEAG’s interest in this pilot project mainly lies in the expectations related to higher efficiency, lower wear and, hence, less expense for repairs and maintenance,’ said Peter Scholze, the company’s head of service - open pit mines. ‘These results have been verified from measurements and analytics taken during operations in the past few weeks. Since commissioning, the drive has been running smoothly.’
Mr Scholze added that the on-site operations and maintenance teams had found the new system to be easy to learn, understand, and use, with no major differences in operation or handling compared with the existing systems/technology.