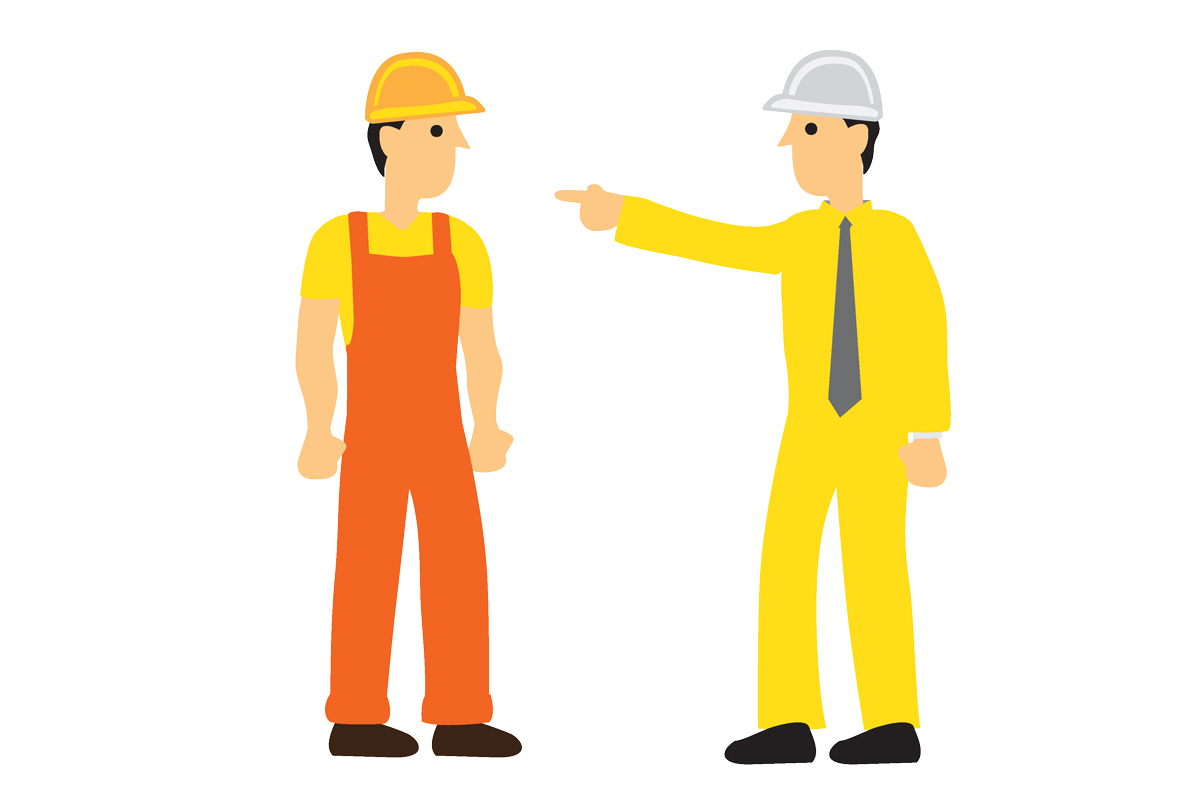
People make mistakes, I was once told if I hadn’t made a mistake, I hadn’t made a decision.
In actual fact people make mistakes all the time. Sometimes those mistakes or errors lead to things going badly wrong and sometimes they don’t.
Management generally look at these errors in two ways.
- The error doesn’t lead to something going wrong: Management might not even know the error happened, because they rarely look or may not be told. In actual fact the error may be beneficial to the way things are working, how weird is that? What I mean is that people do things differently because they have to, because its expected. The good man syndrome….
- The error leads to an incident: Management look at the error with the benefit of hindsight, 20:20 vision and immediately the thought is to blame the worker. The worker has made a violation, has broken the rules.
There is a perception that only bad workers have incidents - the employee is the problem. The management look at the incident and say a better worker wouldn’t have made that mistake or broken that rule.
Have you ever fallen into this trap? Have you ever said the incident happened because the employee made a mistake, broke the rule, got it wrong? Because, if you have, you are missing an opportunity.
I’m not saying that employees don’t make mistakes, break rules or get it wrong. What I am saying is that at the time that the error was happening the person or people who were making the error were not aware of, or considering, the consequence at the exact point in time. It’s not bad workers who make mistakes, it’s all workers who make mistakes and we encourage our employees to be adaptable, to make decisions, to keep things going. And sometimes people make wrong decisions.
If the system can’t handle that then the system is wrong, because people make mistakes.
And yesterday and the day before and the day before that things went OK, Yes?? Well don’t kid yourself that everything was being completed absolutely text book on those days (whatever text book means). To be fair, if you asked your employees to do things the way you currently have it written down could they perform the task? Now there is a challenge for you have a look at your text book, if you can find it. How do you do things well around here?
Mistakes are being made because people make mistakes, but bad things aren’t always happening.
Let’s look at this slightly differently, humans are not robots. In actual fact we rely on people making calls every single minute of the day to get things done, to adjust things. To make minor changes to the process that a robot couldn’t make, and we embrace that. We love the fact our employees are adaptable, can modify and change, can keep the plant running.
So why do we build systems and procedures where we expect people to comply 100% of the time and if they don’t, we blame the individual who has made the mistake. Surely there is a better way.
Why not build a system that can handle an amount of mistake making - build in some capacity. Do it in a way where people don’t get seriously injured or killed by the error. What I am saying is where there is a task being completed that can seriously injury or kill someone if they get it wrong then build in better control, build in checks, build in capacity. Don’t rely on luck. I am going to talk about this a lot more over the coming months and years and you can hear more about this on The Interesting Health and Safety Podcast [details to follow].
But as an example, let’s take a look at your near miss/hit reporting procedure. How effective is it? I would like you to consider the following and add a couple of lines to whatever document you have.
And consider this everytime….
1. Did this near miss/hit occur because our system stopped something more significant happening?
2. Were we just lucky?
Every time a near miss happens it’s a fantastic learning opportunity. If you tick line 1 then you have some comfort that your processes have capacity and people are protected but you may still be able to improve.
If you tick line 2 then you need to change something now, straight away, today!
Oh, I want you to put a third line on the form.
3. On talking to our employees, they have decided that the following improvements should be made to what we do around here.
So how do we achieve this? Well maybe challenge your safety committee to look at what you do, review the near hits/misses or even set up a learning group for your near hits/misses.
Look at how you do things on a good day and challenge. Talk to your employees to make it even better.
After all your employees are not the problem, they are the problem solvers.
If you would like some help setting up learning groups or challenging your systems and people then please call Colin on 07799 656303 or drop an email to colin.nottage@influentialmg.com