Making Use Of Hassock At Hermitage Quarry
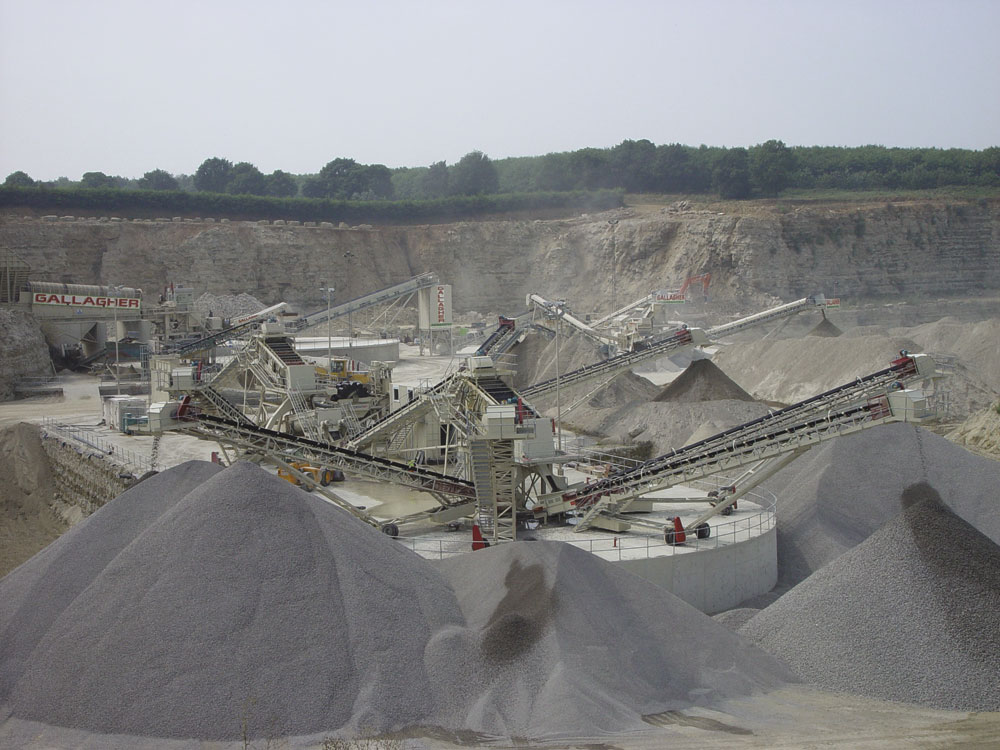
Gallagher invest nearly £2 million in new washing plant and silt-management system
Hermitage Quarry, near Maidstone, one of only two remaining sources of Kentish ragstone, has recently undergone further major development with the Kent-based Gallagher Group, owners and operators of the 24-acre site, investing almost £2 million in a new 350 tonnes/h washing plant and silt-management system.
The deposit at Hermitage Quarry comprises an interbedded 50/50 mix of ragstone (a hard, fine-grained limestone) and hassock (a relatively soft, sandy material with a high but variable silt content). Owing to the interbedded nature of the deposit, both materials are extracted together, with a trommel screen used to separate the bulk of the lower-quality hassock from the ragstone prior to further processing.
Before the introduction of the aggregates levy, a large percentage of the hassock was sold each year as low-price construction fill, with the remainder being used for restoration purposes within the quarry. However, with the addition of the £1.60 per tonne levy, hassock could no longer compete against cheaper alternatives to fill such as ground stabilization. Consequently, the market for hassock dried up and the material became an unwanted waste by-product of ragstone production.
To maintain the quarry’s annual tonnage ‘out of the gate’, Gallagher therefore had to step up extraction rates to recover more ragstone, which in turn generated more unsaleable piles of hassock; an environmental paradox and a situation obviously in direct contradiction to the principles of the aggregates levy.
Although in the past Gallagher had looked at ways of processing the hassock to make better use of it, these investigations concluded that the investment required would deliver only marginal benefits for the company while the material had an existing market as a bulk fill. However, with the loss of this market following the introduction of the aggregates levy, additional investment in new processing plant became a viable option.
In extensive trials using modern washing technology, Gallagher found that by washing the silt content from the hassock and grading the remaining constituents, the resulting materials would prove suitable for use in other applications such as concrete production.
Once the decision to proceed with such a scheme had been made, work on the civils for the new plant commenced in December 2003. This was undertaken by Gallagher Contractors and involved the placement of some 5,000m3 of ready-mixed concrete supplied by Gallagher Concrete.
The project was then handed over to Coventry-based Powerscreen Washing Systems to design, build and install a washing plant that would interface with the quarry’s existing trommel screen and crushing plant.
Aggregate washing
The –100mm hassock discharged by the quarry’s existing trommel screen is now conveyed, via a 26m long powered radial conveyor, to the washing plant feed hopper. By rotating this conveyor to one side, the hassock can also be stockpiled adjacent to the plant if necessary.
The 30-tonne capacity feed hopper, which can also be fed directly by loading shovel, is equipped with a 4.5m long remote-controlled tipping grid. From here material is discharged on to an 80ft long static conveyor that delivers it to a twin-deck static 20 x 6 rinsing screen. This separates any oversize, which is conveyed to stockpile, while the underflow passes to a Fines Master 160 to produce a combined total of 100 tonnes/h of soft and sharp sand. This machine, which effectively retains the sand constituents while separating the –75 micron silt and water, comprises a twin bucket wheel, a centrifugal slurry pump, twin hydrocyclones, a collection tank and a high-frequency 12ft x 5ft dewatering screen mounted on a single chassis. The sands produced have a low moisture content and are delivered to their respective stockpiles by two M100 powered radial conveyors.
The mid-size material from the rinsing screen is fed directly to a Powerscreen Powerscrub 180R log-washer, capable of producing up to 200 tonnes/h of contaminant-free sand and gravel. This unit, which comprises an inclined trough fitted with two counter-rotating axles with Hardox 500 exchangeable blades and an elevated spray-bar system, mixes the incoming feed while scrubbing and washing the material at the same time. Silt-laden process water is discharged via two sieve bends to remove any lightweight contaminants (roots, wood, plastic etc), while the scrubbed mid-size material passes through the Powerscrub and is fed on to a second 80ft long conveyor leading to a static 20 x 6 triple-deck part rinser. Here the material is given a final rinse while being screened into 6mm, 10mm, 14mm and 20mm graded products, which are delivered to their respective stockpiles by four M100 powered radial conveyors.
To minimize sand losses from the plant, all –5mm sand/silt/water underflow from both rinsing screens and the log-washer is fed, via a sump and two Warman sump pumps, to the Powerscreen Fines Master 160.
Silt management
The new silt-management system at Hermitage Quarry utilizes the combined technology and experience of Tecnoidea, CIBA, Parnaby and Powerscreen Washing Systems. The system is designed to clarify all waste water for subsequent reuse and to produce a manageable silt cake. In sizing the water-treatment plant for this application, Powerscreen had to consider such factors as the silt content of the raw material, settlement rate, throughput and site drainage. The system was also specifically designed and sized to minimize operator input and to maintain low running costs.
Water and silt from the Fines Master 160 is pumped across the site to a sieve bend with 3mm apertures. This removes any oversize prior to further processing to help protect the filter cloths on the belt presses. The water and silt is collected in a primary pit and pumped, via two Abra pumps, to two 7m diameter deep-cone thickeners equipped with automatic anti-clog systems on their discharge valves.
Flocculant solution is mixed by two fully automated Tecnoidea mixing stations, housed in an adjacent building, and automatically dosed to the thickeners. As the sludge is fed into the thickening tanks from the Powerscreen plant, the feed is monitored every 50s. This allows the flocculant control system to automatically adjust the flocculant solution feed rate, thereby guaranteeing clean water for reuse and optimizing the amount of flocculant powder used. The mixing and dosing system utilizes a continuous supply of filtered clean water from two borehole pumps and automatically mixes a new batch of solution when the level drops.
Clarified water weirs over the top of the deep-cone thickeners and is piped to a clean-water collection tank for subsequent recirculation back to the washing plant, while top-up water for the washing plant is obtained from two borehole pumps adjacent to the clean-water tank. Meanwhile, the silt settles to the bottom of the cones and is automatically discharged when the density reaches 35% solids; this is constantly monitored to ensure that a consistent feed is pumped to the belt presses. The underflow from both thickeners is collected in a 150m3 sludge tank, fitted with three stirrers to maintain agitation, from where it is pumped, using two inverter-controlled Warman horizontal pumps, to two 3m wide Parnaby multi-roll belt presses.
The entire water-treatment/silt-management system is fully automated with only minimal operator intervention required for the addition of flocculant powder and the removal of the pressed silt cake using a loading shovel.
Acknowledgement
The editor wishes the thank Gallagher Aggregates Ltd for permission to visit the site and, in particular, Martin Hobbs, managing director, for his help in preparing this report.