Making The Grade
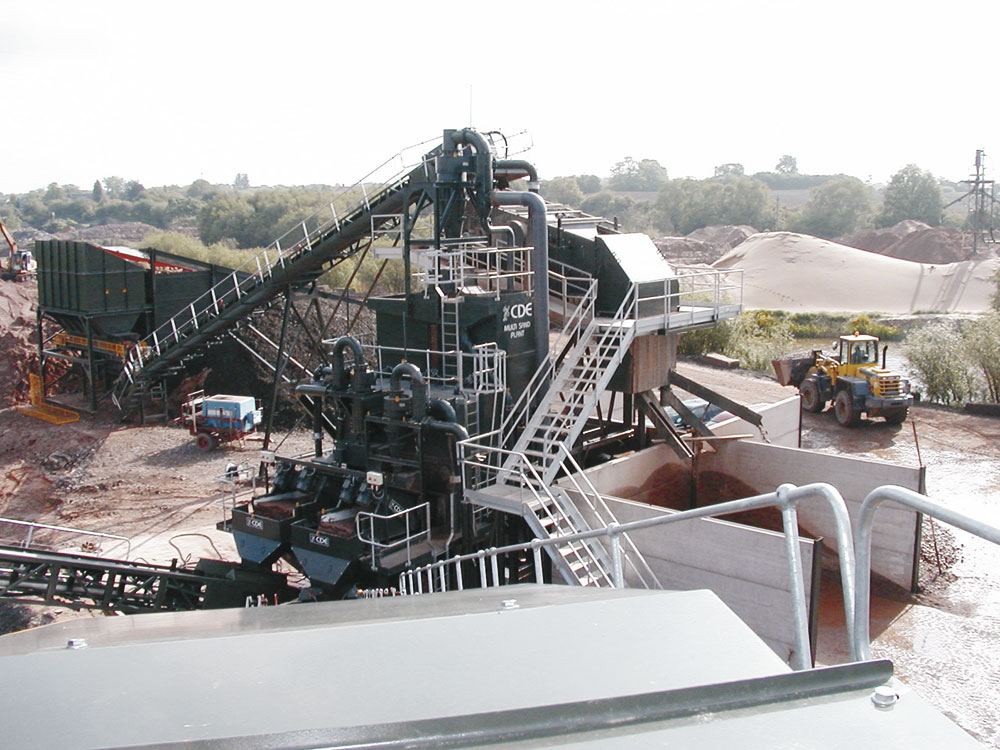
Specialist sports sand supplier chooses CDE Multi-Sands plant
Whitemoss are leading suppliers of specialist sports sands for applications ranging from the equestrian market to their mainstay of prominent golf clubs. Consistency is perhaps the most important element within this market sector where customers demand that the highest specifications be regularly met. To this end Whitemoss test all sands on an hourly basis during production. Root zone and top dressing are batch tested daily and random samples are regularly sent to independent laboratories.
Consistency, however, is not the only measure of specialist sand; the correct specification is crucial and golf sands offer little room for error. For example ‘Greens 1 USGA Top Dressing’ shows 22% retained at 0.5mm, 58.5% at 0.25mm and 16% at 0.15mm. Minus 0.063mm clay/silt must be negligible. Whitemoss’ attention to detail in this respect has been rewarded with repeat contracts from notable customers; Celtic Manor Resort, host to the 2010 Ryder Cup, has been a customer for over 10 years. As Celtic Manor’s golf operations manager Jim McKenzie commented: ‘This partnership is primarily thanks to the consistent and dependable product offered.’
To maintain this level of customer satisfaction while increasing production, Whitemoss decided to invest in a new washing plant for their main production facility near Crewe. The plant would have to achieve tight output requirements for their complete range of sand products. Early discussions noted CDE as favoured suppliers owing to their significant background in specialist plant design, particularly relating to sports and slow-filtration sands. A long consultation period was then initiated with CDE fully investigating Whitemoss’ requirements, ultimately leading to a 100 tonnes/h (sand output) installation.
This unique CDE system offers precise sand grades via full PLC control. The operator simply chooses the required specification from a pre-programmed selection and the plant automatically adjusts the output within minutes, changing the pinch valve timings and cyclone diversions as required. While this may sound complex the system is actually surprisingly compact and efficient. Pipework and valves are kept to a minimum while extensive use of hot-vulcanized rubber linings helps to reduce wear. There are very few moving parts within the system and nothing is required to operate while submerged. In addition, all elements are highly modular to facilitate inspection and maintenance. This approach also allows units to be easily modified or changed in the long term should the feed or output requirements change dramatically.
The process begins at a 50-tonne hopper with a 750mm belt feeder. Material is then carried by a 20m static conveyor to a triple-deck 16 x 5 rinsing screen featuring rubber top and middle decks and a polyurethane lower deck. This screen was supplied complete with galvanized stairway, walkways and handrails. CDE’s splash-reduction equipment was also included; the top deck is enclosed and each spray bar is sealed to the screen box by a flexible Faber grommet.
Oversize, 20mm, 10mm and 6mm aggregates are delivered directly to walled stockpile bays while the sand slurry passes to a sump. From here a Warman 8/6 pumps the slurry to the first of three hydrocyclones within the CDE Multi-Sands plant. This cyclone removes the majority of water and silts to an accurate and consistent silt cut-point of 70µm. Underflow is sent directly to the first counter-flow classi-fication unit (CFCU) for further separation. These are essentially hindered-settling tanks that separate sand at a point defined by an upward flow. Sand slurry is introduced to the top of the tank while clean water is introduced to the base at a precise rate; fines overflow the built-in weir while heavier particles settle. These larger particles are removed by a series of pinch valves, controlled by the PLC.
The precise configuration of a CDE Multi-Sands plant will vary for each application to accommodate the different feed materials and finished products involved. In this particular case the larger particles from the first CFCU are fed to the second unit while the fine fraction overflows to a sump. This –250µm slurry is pumped to a further hydrocyclone located above a Quickdry dewatering screen to offer the first sand.
The second CFCU divides the coarser fraction in the same manner. Heavier particles are taken from the bottom section of the unit via pinch valves and report to a slightly larger Quickdry dewatering screen as the main sand product. This screen is located over a further sump that receives overflow from the second CFCU. This slurry is pumped to a third hydrocyclone to recover the fines; the system can automatically divert this fraction between both dewatering screens, as dictated by the output specification. The overflow from this hydrocyclone is relatively clean as it has already passed through the first hydrocyclone; it can therefore be recycled to the primary sump, thus reducing overall water requirements.
CDE have used the same specification of dewatering screens as found in their popular Compact Sands plant. These incorporate Tema-Isenmann modular dual-density polyurethane panels as standard. Specially designed screen mounts and profiling ensure that very little force is passed to the support structure, greatly enhancing efficiency. Sand from the plant is passed to the CDE stockpile conveyors at less than 12% moisture content. These 20m static units feature full-length galvanized walkways with handrails, safety pull-cords and guarding as standard.
The system has now been running for a number of months and has proven both accurate and reliable in terms of the sands offered. Whitemoss director Dan Beecroft is certainly pleased with the results. ‘The CDE plant has given us an unrivalled ability to produce limited or large-run quantities of particular sands at short notice; 98% of orders are delivered within 48h. We now regularly produce five different specific grades of sand with consistent grade and low moisture content.’