PSWS Provide The Solution At Costessey
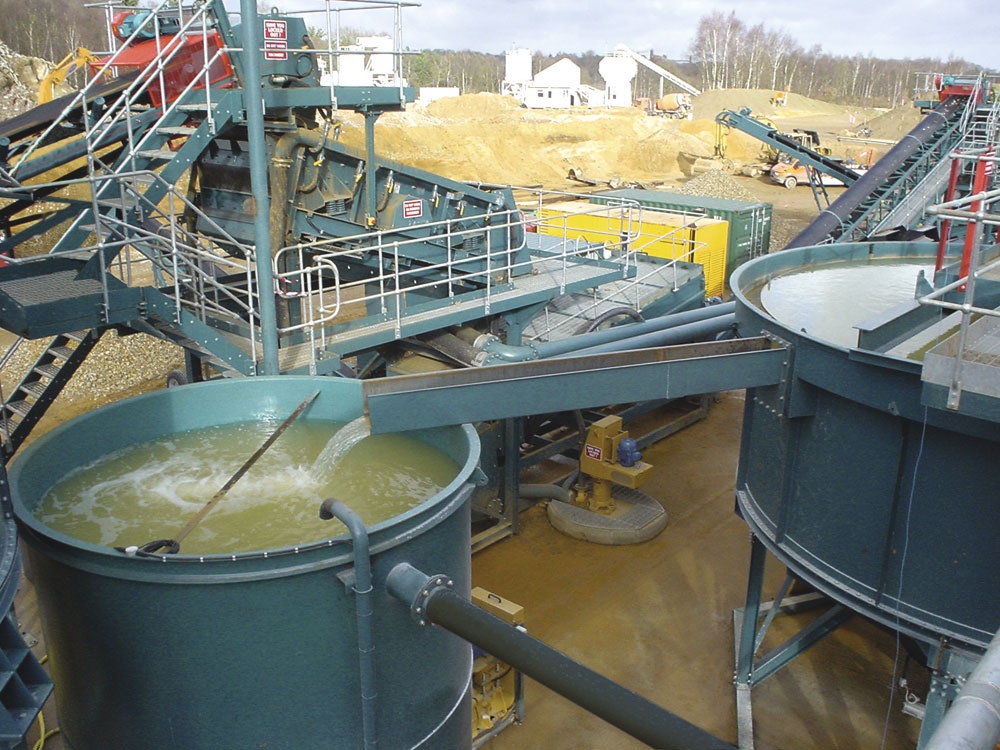
New washing plant and plate press eliminates the need for silt lagoons
Costessey Quarry is RMC Materials’ third largest site in Norfolk and plays an important role in the local construction materials market, particularly in supplying ongoing development in the city of Norwich. In addition to aggregate processing, the site boasts a ready-mixed concrete and mortar plant and a full recycling facility, as well as supplying a nearby asphalt plant.
During the past few years the site has undergone a reduction in size as land has been allocated to housing development. Whereas the original static plant relied on lagoons for silt disposal, as the site diminished a decision was made to install a new plant with the technology to manage water efficiently without the need for lagoons.
Coventry-based Powerscreen Washing Systems (PSWS) successfully tendered for the supply and installation of a washing and screening plant that would produce high-quality products while maintaining an efficient water-management system. Elimination of the lagoons is dealt with through the use of a plate press that provides a closed-loop system for the entire operation.
The plant is fed by wheel loader via a Commander 1400 feed hopper complete with remote-controlled tipping grid. From here the material is fed on to an inclined transfer conveyor for delivery to the primary screen — a Powerscreen 2 x 5 static rinser. Fitted with polyurethane screen modules and featuring six spray bars on both the top and bottom decks, the vibrating top eck rejects oversize material, which is delivered to an adjacent ground stockpile via a T4026 radial conveyor.
Mid-size material from the rinser is discharged into a Powerscreen Powerscrub 120R capable of producing up to 120 tonnes/h of contaminant-free sand and gravel. This unit comprises an inclined trough fitted with two counter-rotating axles with high-tensile exchangeable blades and an elevated spray-bar system. The unit mixes the incoming feed while milling and washing the material at the same time. Any lumps of earth or clay are broken down during this process and carried away in the wash water, while any lighter particles are floated off through specially designed outflow exits. Two spray bars are mounted at the discharge end of the unit to provide a final rinse.
The mid-size material is then fed on to a static transfer conveyor for delivery to the final screen. Similar in design to the primary screen but in this case fitted with a partial rinsing system, this unit sorts the material into three final single-size products — 10mm, 20mm and 40mm. These are delivered to their respective ground stockpiles by three T4026 radial stockpiling conveyors.
Meanwhile, the underflow from the bottom deck is classified and dewatered by a Fines Master 120 to produce a combined total of approximately 120 tonnes/h of fine and coarse sand, which is delivered to stockpile via two T4026 radial stockpile conveyors.
As water management was an essential part of the project, PSWS sourced a Tecnoidea multi-plate filter press specifically designed and sized to minimize operator input and maintain low running costs. As well as this 36-plate press the system includes a foul-water pump; an automatic flocculant mixing and dosing plant; a 6m diameter dynamic thickener tank with pneumatic discharge valve; a silt buffer tank with two stirrers; a 43m3 lime silo with automatic mixing and dosing tank; a fresh-water tank; and all the associated support framework, structures, walkways and access platforms.
The entire system is fully automated and requires only occasional operator intervention to add flocculant powder and remove the pressed silt cake using a loading shovel. As the sludge is fed into the thickening tank from the Powerscreen plant its density is monitored every 50s. This allows the system to automatically adjust the feed rate of the flocculant solution, thereby guaranteeing a continuous supply of clean water for reuse and minimizing the amount of flocculant required.
Once in the thickener the silt settles to the bottom of the cone and is auto-matically discharged into a silt buffer tank where the lime is added. The quantity of lime is controlled using a rotary valve that feeds the lime on to a rotary screw, which in turn feeds the lime into a mixing tank. At this point water is added to the lime to create a solution, which is automatically distributed into the silt buffer tank as required. The lime solution reacts with any clay material int he silt to facilitate the water drainage in the press. Once the press has been filled and the water drained the unit opens to allow the compressed silt cakes to drop into a concrete bay located below, before cleaning itself in readiness for another cycle.
Commenting on the success of the plant, which is currently in the final stages of handover, Mark Wood, RMC’s operations manager, said: ‘From initial quotation to the fitting of the last nut and bolt, PSWS have performed extremely well. Aspects such as build quality and the health and safety regime have been exceptional and any problems that have arisen have been dealt with efficiently and effectively.’