New Sand and Gravel Wash Plant for Readymix West Indies
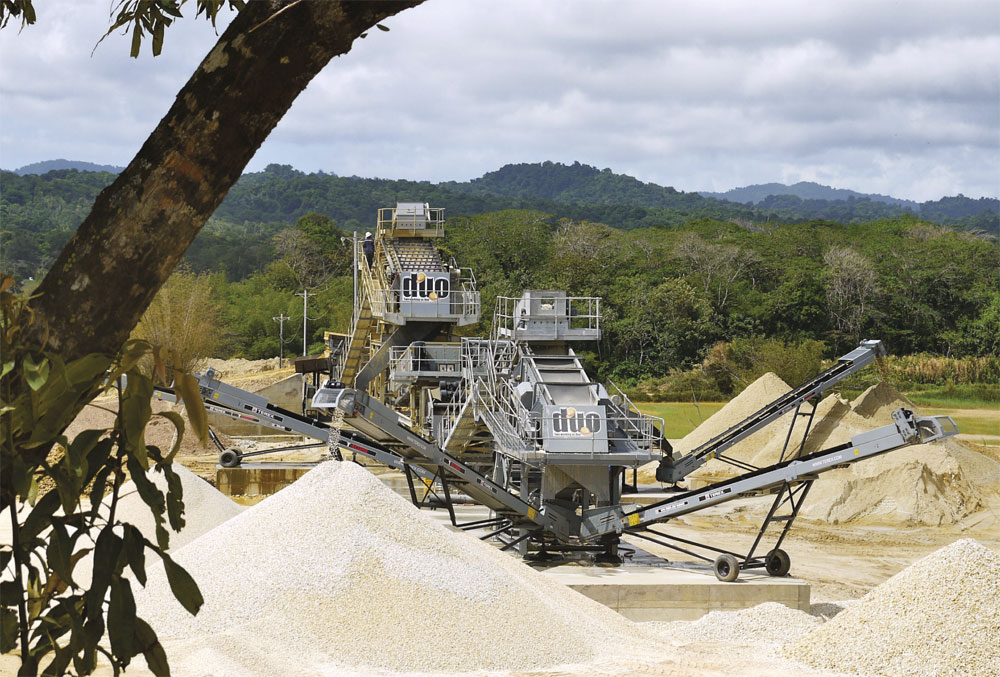
First published in the August 2013 issue of Quarry Management
DUO supply Terex Washing Systems plant to one of Trinidad's leading concrete producers
When Readymix West Indies Ltd needed a new sand and gravel washing plant to replace their existing facility in Valencia, Trinidad, they chose to work with DUO plc, who have more than 35 years’ industry experience and are well known across the Caribbean region.
Readymix (W.I.) have been one of Trinidad’s leading producers of high-quality concrete and related products since 1959. They are a member of the TCL Group – the leading producer and marketer of cement and readymix products in the Caribbean – who have eight operating companies in Trinidad, Barbados, Guyana, Jamaica and Anguilla, including Readymix (W.I.).
In 1962, Readymix (W.I.) began their sand and gravel operations in Valencia, supplying their own concrete plants and other customers with aggregates. They now stand as the single largest producer of pre-mixed concrete in Trinidad and Tobago. The company currently boasts an extensive network of concrete plants throughout the area and has even expanded its operations to other regional markets, such as Barbados.
After careful analysis of Readymix (W.I.)’s specific requirements and by paying particular attention to the varied high-silt feed material, DUO proposed a bespoke Terex Washing Systems (TWS) plant capable of processing clay-bound sand and gravel to produce three aggregates and one grade of sand at a rate of 200 tonnes/h. Readymix (W.I.) had no hesitation in selecting the Terex plant for their site in Valencia over other options due to the specific expertise both DUO and Terex offer in this field, along with their ability to provide a comprehensive sales and support package.
Ravi Singh, quarry manager for Readymix (W.I.), commented: ‘DUO and Terex closely investigated the product to be processed; they analyzed it thoroughly and from this designed a bespoke plant most suited to our individual needs. In addition, they provided a dedicated team of engineers, sales and after-sales technicians to provide support throughout the plant installation and commissioning process.’
The new DUO/TWS washing plant replaces an existing plant that had been burdened with inefficiencies and maintenance and production issues. All of these problems have now been effectively addressed through the new bespoke plant, which comprises an H9 feeder, 206R screenbox, FM 200C cyclone, 146 dewatering screen, PS 200R log-washer, 165D dry screen, two lattice-frame feed conveyors and four TC4026 conveyors.
Luke Talbot, international sales manager for DUO, commented: ‘We were delighted when Readymix (W.I.) selected us as their preferred supplier for the washing plant, which reinforces the success of our previous projects in this market and shows the strength of our reputation in the region. The new plant has been very well received and will certainly add a new dimension and increased efficiency to their overall production.’
Ravi Singh continued: ‘The new plant has replaced an existing barrel-type washing plant. The maintenance costs on the old plant were extremely high, making it less cost-effective for processing. However, the TWS equipment has much lower maintenance costs, allowing us to be much more competitive in the market. The newly designed plant also provides a cleaner, more desirable product.’
New plant
Operating at 200 tonnes/h, the new washing plant is designed to deliver four grades of product: 0–6mm sand and three aggregate products (6–10mm, 10–20mm and 20–75mm).
The sand accounts for approximately 60% of production, the aggregate comprise 30% and around 10–15% waste fines are discharged to silt ponds.
The site’s natural clay-bound sand and gravel feed material is first delivered to an H9 feeder with vibrating grid. This removes any +100mm material while an inclined lattice-frame feed conveyor, designed and built by DUO’s manufacturing division, delivers the –100mm material to a 206R two-deck rinsing screen for initial grading. Here, the top deck removes any +75mm material, which is stockpiled using a TC4026 conveyor, while the bottom deck removes the 6–75mm material.
Meanwhile, the –6mm underflow is pumped into a FM 200C cyclone sand-recovery unit, which produces an instantly saleable 0–6mm sand. This particular unit is capable of producing up to two separate grades of sand, but in this case the customer has opted for a single grade.
Due to the high and varied level of silt content in the 6–75mm aggregate material, this fraction requires additional scrubbing to ensure that it is cleaned to specification, which is achieved by means of a PS 200R washer unit equipped with dewatering screens at either end. This machine consists of a trough and two counter-rotating spiral axles with exchangeable blades that intensively scrub the feed material, effectively breaking down any clay agglomerations.
The clean 6–75mm aggregates are discharged from the PS 200R washer on to a second DUO lattice-frame conveyor for delivery to a 165D two-deck dry screen to achieve the final three-way split into the desired end products, which are sent to their respective stockpiles by three TC4026 conveyors.
Currently, dirty water containing –75 micron silts and clays from the FM 200C cyclone sand-recovery plant is sent to a series of settling ponds, although, in the future, a Terex water-treatment plant could be installed to eliminate the need for these ponds.
The entire washing plant is controlled and monitored from a central PLC electrical control panel housed within a 20ft ISO container. The panel is programmed to allow automated start-up and shutdown sequences, and was fully wired and programmed before leaving the factory.
Commenting on the installation process, Ravi Singh said: ‘The installation was very fast and efficient, which we were pleasantly surprised about, considering the complexity of the plant. It was delivered and installed in a very short time-frame, which ultimately reduced the overall costs.’
Speaking after the plant had been in operation for a month or so, Mr Singh, added: ‘We are extremely impressed and excited about the prospects for this new DUO/TWS wash plant, which is currently operating at 200 tonnes/h. We can firmly say this is the largest project the company has embarked on for a long time and undoubtedly the most successful in terms of production. The entire Readymix (W.I.) team involved in the project has been extremely impressed with all aspects of the plant, from the initial conception through to the final end-product, including consultation, engineering, service and aftersales support from both DUO and TWS.’
- Subscribe to Quarry Management, the monthly journal for the mineral products industry, to read articles before they appear on Agg-Net