The Power of Telemetry
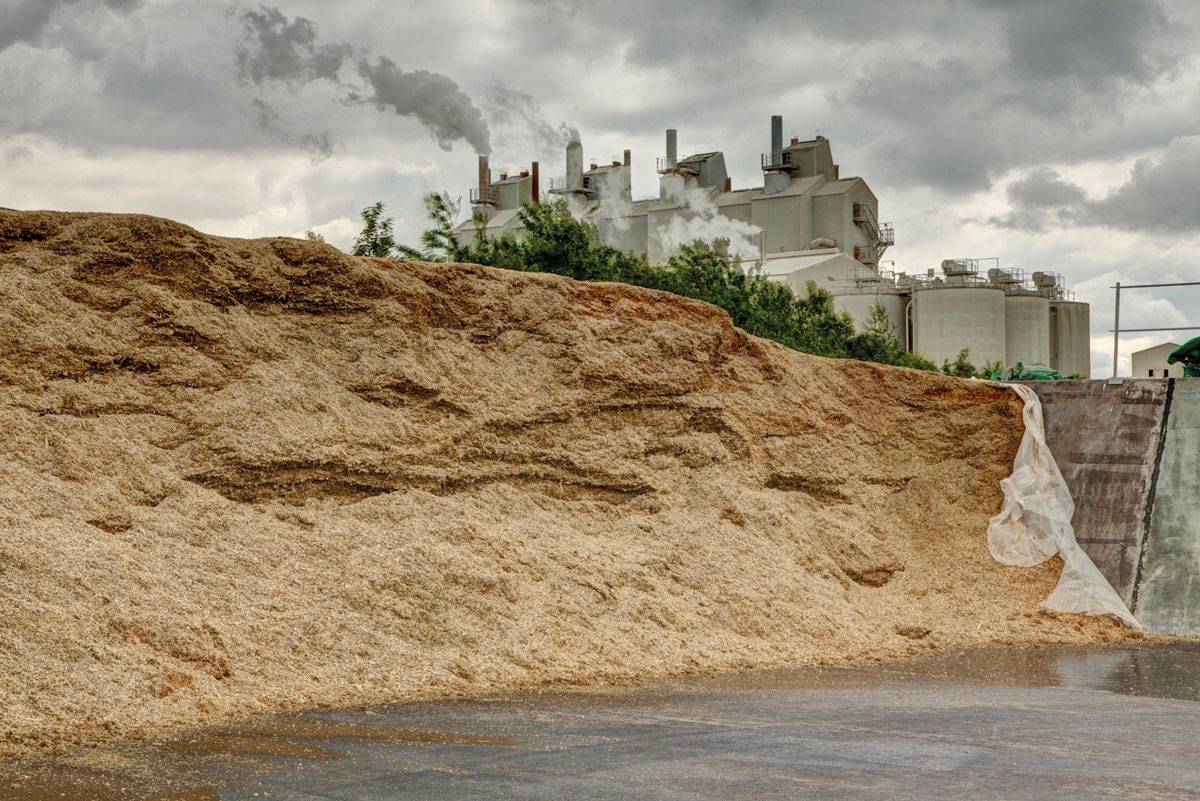
First published in the March 2022 issue of Quarry Management
How digital silo management is driving efficiencies for a 200-year-old quarrying business
Realizing major efficiencies in a business that has been perfecting its craft for nearly 200 years is never going to be easy. But for Singleton Birch, the continuous drive for efficiencies and innovation is what has built the business into the UK’s leading independent supplier of lime.
The company was named after founder and mineral merchant William Singleton Birch and was established in 1815. Since that time, it has grown into a global supplier of lime products and services, and even gave rise to that most British of institutions, car maker Aston Martin, via the former business owner and William’s grandson, Lionel Martin.
Reducing carbon emissions
Today, one of the main drivers of innovation at Singleton Birch is reducing carbon emissions across the entire group. Chief executive officer Richard Stansfield sees decarbonizing quarrying and lime production as a huge opportunity to help many processes and industries become more sustainable, as lime in its different forms is central to so many sectors.
To facilitate this, Singleton Birch recently announced a partnership with technology start-up Origen Carbon Solutions to work towards creating carbon-net-zero lime. The two businesses are working closely to build a carbon-neutral lime kiln where the CO2 emitted during the manufacturing process is removed. The technology, which will underpin a prototype plant capable of making 3,000 tonnes of carbon neutral lime per year, can even remove CO2 from the atmosphere.
‘Normally, lime production results in large amounts of carbon dioxide being emitted into the atmosphere,’ said Mr Stansfield. ‘Origen’s process produces lime in a way that captures all of the carbon dioxide that would normally be emitted, resulting in the generation of a zero-carbon lime.
‘Technologies like this are vital to the future of our industry, but also all the industries that rely on lime as a product, of which there are many. Much more important than that, however, is the fact that the world is relying on these types of innovations, as they have the power to slow down or even halt the biggest issue of our time – climate change.’
Internal processes
Grand plans to produce carbon-neutral lime are just one half of the battle, however. The other is realizing efficiencies and carbon savings within the rest of the business, ensuring all processes are as slick as can be. After nearly 200 years, over which time those processes have been constantly refined, efficiencies can be harder to find, and gains are often incremental.
But one area that has made a huge difference, both in terms of carbon emissions and bottom line, is a focus on inventory management. This led Singleton Birch down the path of remote monitoring for all hoppers and silos involved in the quarrying process and the wider business, which has not just helped revolutionize how the business operates itself, but has had marked, positive outcomes for how key clients manage their own silo levels.
The benefits of telemetry
Singleton Birch’s interest in telemetry brought them to Minsterport, at the time a West Yorkshire-based business that specializes in silo and process control solutions with more than 30 years’ experience in UK and European markets.
Minsterport provide their own telemetry platform, MySilo, which allows silo operators and managers to safely record data and measure silo contents without incurring the health and safety risk associated with working at height by manual checking. However, Singleton Birch soon realized the platform’s potential to deliver efficiencies via better forecasting, optimizing logistics, and almost eradicating the risk of silos running dry, was where its real value lay.
As a result, the business quickly moved to acquire Minsterport, which it successfully did in 2018, and now the telemetry specialist resides at Melton Ross as a valued member of the Singleton Birch family, providing products and services to other quarrying businesses and those in a host of silo-dependent industries.
According to Richard Stansfield, the efficiencies the platform brought to the business were evident early on and produced cost savings. ‘What was obvious was Minsterport’s experience in supplying the right weighing solutions for the applications was crucial when looking at how to get the information we needed on monitoring production for our four Maerz kilns,’ he said.
‘Not only did the cost-effective strain-gauge solution gives us the ability to know exactly what weight was being fed into the kilns, it also enables us to add a crucial safety feature. In the past, if there was an issue at the top of the kilns and the feed hopper had not emptied enough for the next skip, the programme would still call for product and overload the hopper.
‘Now, with this added accurate weighing system, we know that if the weight is not less than 3,000kg it will stop the programme, allowing us time to resolve the issues and stopping us overloading the hopper.
‘We can also now more accurately compare the amount of stone that is being fed into the kilns with what we are producing out of the bottom of the kiln as calcium oxide, which is essential for reporting our emissions to the UK ETS scheme.
‘We have also connected the strain-gauge system to 20 of the on-site silos we use to store our finished powder products and the remote monitoring software. It was a simple and inexpensive thing to do, but it has brought tremendous clarity to the business.’
However, it was the potential to bring similar efficiencies to their clients that led Singleton Birch to acquire Minsterport. ‘We quickly learned what remote monitoring could do for us,’ said Mr Stansfield, ‘but that wasn’t the whole story. We knew that if we could convince our customers to use it, the risk of them running out of product would be a thing of the past, simply because they – like us – can see exactly what is in their silos at any time, from anywhere with an internet connection.’
Minsterport business manager Peter Widdowson said that the telemetry system also enabled Singleton Birch to plan hopper and silo service and maintenance routines more effectively by identifying lime build-up in the bins. As anyone who uses or produces lime will know, the product becomes notoriously adhesive when it comes into contact with moisture, setting hard against the internal walls of storage vessels. This can lead to reduced usable volumes and problems with discharging the product.
But Mr Widdowson said the telemetry system identified problems with build-up much earlier than human judgement. ‘Remote monitoring will pick up lime deposits earlier because the silos will never register as empty,’ he explained.
‘The build-up will always be in there and will be picked up by whatever sensors are being used to monitor the silo. However, it is the software that identifies the issue because the pattern of discharging the product changes, and that is the key. Once you see that occurring, you can investigate any issue you might have that if left, could lead to major problems.’
Logistics efficiencies
The final link in the lime production chain is delivering the product to customers. It is here telemetry has had the biggest impact in terms of cost savings and the reduction in carbon emissions.
By encouraging customers to adopt a telemetry system and giving Singleton Birch access, they can assess their customers’ needs remotely, and optimize the delivery schedule around that. Doing this has led to a significant reduction in the number of partially full tankers sent out and has dramatically cut down on wasted tanker journeys.
Mr Widdowson said: ‘What often happens is a customer might have the capacity to take 28 tonnes of lime, but on a Friday, they’re running low and want to ensure they have enough to last until Monday. So, instead of ordering a full delivery, they’ll order 24 tonnes. This is inefficient and if this is the way they regularly order, essentially using best guess, they will order many partial loads across the year.
‘With the telemetry system in place, we can assess all their silo levels directly and work out if they have enough lime to last until Monday. If they do, we deliver a full load then. Working like this means they never run out of product and we reduce our annual number of tanker journeys, which can be by as much as 25%.’
Adopting this system also allows Singleton Birch to manage lime-in, waste-out services more effectively, generating customer efficiency gains by scheduling one tanker to deliver the lime and take away any waste powders generated on the customer’s site. Previously, using different tankers for this was common.
But as fuel accounts for 30–40% of the running costs of an HGV and HGV movements account for around 5% of the total greenhouse gas emissions emitted each year in the UK, Mr Widdowson said large efficiencies can be gained.
Even the newest, most fuel-efficient HGVs use around a gallon of diesel every seven to eight miles, he said, meaning an average journey of 200 miles will emit 330kg of CO2 to atmosphere.
‘Often, a wasted journey will incur a
200-mile round trip, so you can see the impact this is having on the business’s costs and the environment,’ said Mr Widdowson. ‘Without telemetry in place, these journeys happen several times a week.’
Data-driven efficiencies
Richard Stansfield added that adopting telemetry across the lime operation had allowed the business to get data-driven insights across parts of the business they had not previous been able to. This has translated into new ways of doing things that improve their own processes and their service to customers.
‘When we set out on the journey of introducing telemetry, we had an idea of the benefits we wanted it to bring us,’ he said. ‘But it has ended up delivering so much more than that, from mining the stone through to ensuring our customers never run out of product, it has added value at every step of the way while at the same time helping us to cut costs and our carbon footprint. It is definitely a win-win for us.’
For more information about the advantages of telemetry, visit: www.minsterport.com
- Subscribe to Quarry Management, the monthly journal for the mineral products industry, to read articles before they appear on Agg-Net.com