Extending oil change intervals on heavy mobile plant
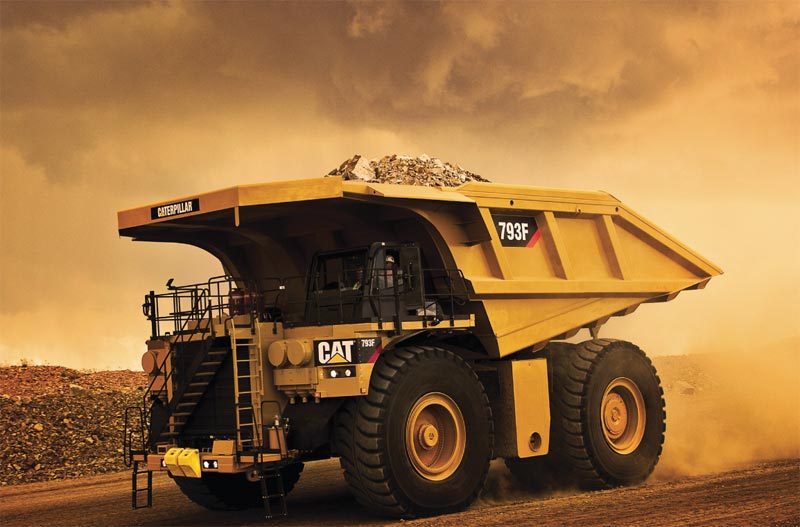
First published in the November 2013 issue of Quarry Management as Upping the Interval
Kleenoil By-Pass Filtration discuss how extending oil drain intervals on mobile plant can lead to significant cost savings
Extending oil drain intervals in off-highway engines and machines can be challenging. The cost reduction associated with longer oil and filter change intervals has to be balanced against the risk of shortened engine life and the costs associated with less reliability if oil drain intervals are extended too far.
There are many hidden costs of an oil and filter change that have influenced companies to find a more efficient approach to keeping oil healthy and reliable. A recent study found that the true cost of an oil change normally exceeds the oil cost by a factor of 40. These same principles can be applied to filter changes.
The following factors contribute to the true cost of an oil change: lost production; paperwork (including maintenance schedules, data entry, manpower planning, inventory management, work orders, documentation etc); labour and supervision; and storage and handling costs, purchasing and quality assurance (additional costs associated with obtaining lubricants must be taken into consideration, such as lubricant storage and handling, filtering new oil to ensure compliance with specifications, analyzing oil samples, transportation, disposal of used oil, environmental issues etc).
Often a lubricant remains serviceable for long periods of time without draining and recharging (influenced by makeup rates, operating temperature, fluid volume, cleanliness etc). Draining oil and adding new lubricants into a system can present risks such as: introduction of the wrong oil; introduction of contaminants or contaminated oil; re-suspension of settled contaminants in the tank/sump floors and inactive zones; and human agency failures (dead-heading pumps on restart, not opening suction lines, not removing cleaning solvents, loosening machine parts etc).
Considering the real cost and associated risks of an oil change, it is wise to let the conditions of the oil drive the decision.
Life factors for in-service lubricants
An assortment of operating conditions can reduce the life of lubricants and filters. If possible, these are to be avoided, however very often nothing can be done, as many of the factors are associated with the machine’s application and environment. The timing of an oil and filter change is important, but even more important is the strategy to proactively improve the conditions that extend oil life. When applied correctly, proactive maintenance strategies can double or triple lubricant and filter life. This is achieved by reducing the conditions that stress the oil and filter. Factors that influence the life of a lubricant include:
Contamination
Contamination control is indispensable in preserving the integrity of all material in power and motion systems. Without it, few if any systems could ever achieve their intended purpose, let alone their expected service lives. Knowing the potential and probable sources of contaminants helps to establish an effective exclusion programme. Generally, three fundamental modes contribute to contamination:
- Those injected by people (implanted during manufacturing or induced in the field during maintenance, repair or overhaul operations).
- Those generated by the systems (created tribologically, chemically or by desorption).
- Those ingested by the machine (introduced by inhalation of dust, air and water; encroachment of energy; and migration of microbes from the environment).
The control of contamination in machinery is pointless if contaminated or below-specification lubricants are used, or if clean lubricant is being handled so carelessly that it enters machines in a contaminated state. Much work should be done in close cooperation with the lubricant suppliers to ensure that clean lubricants of the right specification are used in a particular application.
High fuel consumption
Inefficient engines contaminate by way of combustion by-products, including soot, fuel and fuel residuals, sulphur, acids and water. These contaminants distress the quality of the lubricant, resulting in filters going into bypass very quickly.
Blow-by
Worn engines, timing/injector problems, lugging, incorrect rack settings, excessive idling, cold operating conditions and high elevations can all contribute to increased blow-by. This adds soot, fuel and other contaminants that distress even the most robust lubricants.
Coolant leaks
Glycol and water sharply disrupt dispersancy and contribute to a host of other problems such as corrosion, deposits, filter plugging etc.
Fuel dilution and fuel quality
Fuel dilutes additives and introduces sulphur and aromatics into crankcase oils, which will affect viscosity. Lubricant and filter life is influenced by the quality of diesel fuel and natural gas, especially relating to sulphur levels.
Air cleaners
Blocked air filters result in the engine being starved. This causes overfuelling, leading to higher levels of soot entering the crankcase oil.
Running conditions
Lugging, stop-and-go driving, intermittent service, cold ambient temperatures, idling etc, all influence the life of the crankcase oil.
Oil level
Low oil levels concentrate heat, contaminants and catalytic wear metals, resulting in fewer additives being available to resist oxidation and lubricant degradation.
Abrasives
Dirt and other solid contaminants attract additives and can catalytically advance the rate of oxidation. An even bigger problem is associated with the wear debris that is generated by abrasion and its influence as a pro-oxidant.
Water contamination
Water contamination leads to oxidation, additive distress, loss of dispersancy and many other lubricant life problems.
Sludge and varnish
Oil degradation products often contain high concentrations of carboxylic acids, free radicals and hydro-peroxides. When oil is drained from a compartment but sludge and varnish remain, the following oil change could be short-lived.
Make-up rate
Make-up oil refreshes additives and dilutes contaminants. Lube compartments with low make-up rates, while beneficial in one sense, also require more frequent oil changes.
Lubricant quality
The quality of base oils and additives can have a marked influence on oil life. Some lubricant suppliers can design lubricants with specific characteristics suitable for a high or low ambient temperature environment. High operating temperatures accelerate the rate of additive depletion and oxidation.
Other contaminants
The ingress of other contaminants can degrade additives and affect the quality of base oils. Any fluid system, reservoir or gearbox that is open or connected to the atmosphere by means of a breather inhales and expels air. By this action, it ingests moisture and collects water. Humid air exposed to temperature variations in a reservoir constantly condenses water into the system, causing hydrolytic action, corrosion, fluid additive breakdown etc.
Establishing extended oil drain intervals
To establish extended oil drain intervals it is necessary to: construct a fleet profile; estimate oil drain intervals and potential cost savings associated with the optimum oil drain intervals; assess the risk associated with the optimum oil drain intervals; develop a testing plan for a small segment of the equipment fleet to determine if the estimated oil drain intervals are acceptable; and implement the optimized oil drain interval after testing.
Fleet profiles describe the equipment, service severity, operating conditions and maintenance practices. Different engine models contaminate engine oil at different rates, while the same engine may have a different oil volume in different equipment. Fuel and oil consumption rates vary for different equipment and service severities.
The capability of the oil and the engines must be considered to properly estimate oil drain intervals. Studies show that a litre of fleet oil possesses the ability to neutralize and suspend the contamination generated by burning 300 litres of fuel. High-quality premium oils have the ability to neutralize and suspend the contamination generated by burning 500 litres of fuel.
Conclusion
Extended service intervals can lead to significant savings. By using oil analysis, setting target cleanliness levels and adopting proactive maintenance, a significant downward trend in lubricant consumption and maintenance costs can be achieved. At the same time, the availability and utilization of equipment will increase, allowing for more production and higher revenues.
This article has been compiled from information supplied by Kleenoil By-Pass Filtration Ltd. For further information visit: www.keenoil.co.uk
- Subscribe to Quarry Management, the monthly journal for the mineral products industry, to read articles before they appear on Agg-Net