Moving Forward
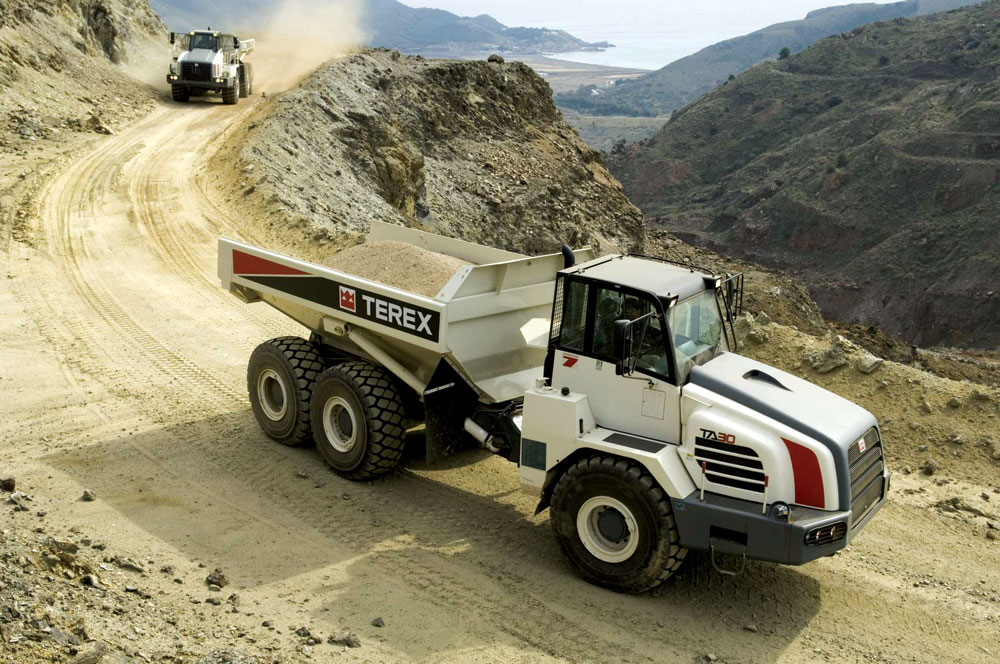
Terex Construction focus on the right products, the right people and the right processes
Last October Terex Corporation held a packed two-week programme of construction product presentations and demonstrations for an international audience of customers, dealers and the trade press. The event was held at the renowned La Manga resort in the Murcian hills on the east coast of Spain, and made use of the natural amphitheatre of an extensive nearby quarry for working demonstrations.
The object of the programme was threefold: first, to bring home to the participants the full expanse of the now extensive Terex product range; secondly, to highlight the key initiatives the company has in place to maximize customer productivity and return on investment; and thirdly, to demonstrate how Terex is adopting the latest technology in current and planned future models.
The event also provided an opportunity for the company to explain the benefits and reasoning behind the recent realignment of the leadership team within the Construction Group, which Terex say will maximize responsiveness to customers on a global level.
Following on from the Bauma exhibition in Munich in April 2007, where some of the newest Terex machines were first announced, the La Manga demonstration programme provided the first opportunity for many customers to see the equipment in action, and to have the chance to inspect, operate and discuss the machines at close quarters with product experts.
The line-up of more than 50 machines included representative models from every sector of the Terex Construction product range, from mini-excavators and site dumpers to wheel loaders, excavators and rigid and articulated dumptrucks, including the new TA30 ADT with its fully independent front suspension, the new top-of-the-range TG230 grader and the latest TL420 and TL450 wheel loaders with their load-damping carry system. In addition, products from other divisions of Terex Corp., including mobile crushers and screeners and large mining shovels, were also on display and demonstration.
Around 1,000 participants from major markets around the world took part in the event, which had a strong message woven through it that Terex are ‘moving forward’ in terms of quality, engineering and customer support.
Welcoming guests to the La Manga resort, Robert Isaman, president of the Terex Construction Group, said: ‘This is definitely a two-way event. We at Terex gain from demonstrating our latest products, but also from listening to end-users; taking on board their plans and expectations for the future, and helping them ‘move forward’ as well, by assisting them in making well-informed purchasing decisions to meet their own business objectives.
‘Over recent months, we’ve been assembling the right people and building the right processes to deliver the right products and services that our end-users need to become more productive at their job sites.’
Mr Isaman explained that focused actions had started around three core work initiatives:
- ensuring that Terex never leave a customer with a problem
- driving down the total cost of ownership
- focusing on building products that increase jobsite productivity.
‘We have already substantially changed our organization from being ‘product-centric’, where dealers and end-users often needed to co-ordinate with multiple points within the company to resolve an issue, to a more ‘customer-centric’ organization, with Terex Construction organized geographically into seven areas, each run by an area director. This will push decision authority further down in the organization to ensure quicker responses and actions,’ Mr Isaman explained.
He added that the company would also be focusing on several initiatives to drive down the total cost of ownership, including improved service density, greater commonality of components and more homogenous machines, while other initiatives would focus on building products that increase jobsite productivity.
‘Given the global shortage of both skilled operators and service technicians, our machines will be designed to be simple and intuitive to operate, repair and maintain,’ he said. ‘Our designs and training programmes will focus on how to make the operator more efficient and effective, within the context of the work to be performed at the job site.
‘We like to think of ourselves as a learning company, one that gets better with each developmental step we take along our journey of self-improvement. We also know that our success is dependent on our customers’ successes, which is why all of our staff, whether they work in engineering, after-market support or on the shop floor, understand the importance of doing what is right for the customer. This is part of our culture and central to the journey we are on.’
Terex Construction, Motherwell ML1 5RY; tel: (01698) 732121; email: construction@terex.com