Face Stability - Where Are We Now?
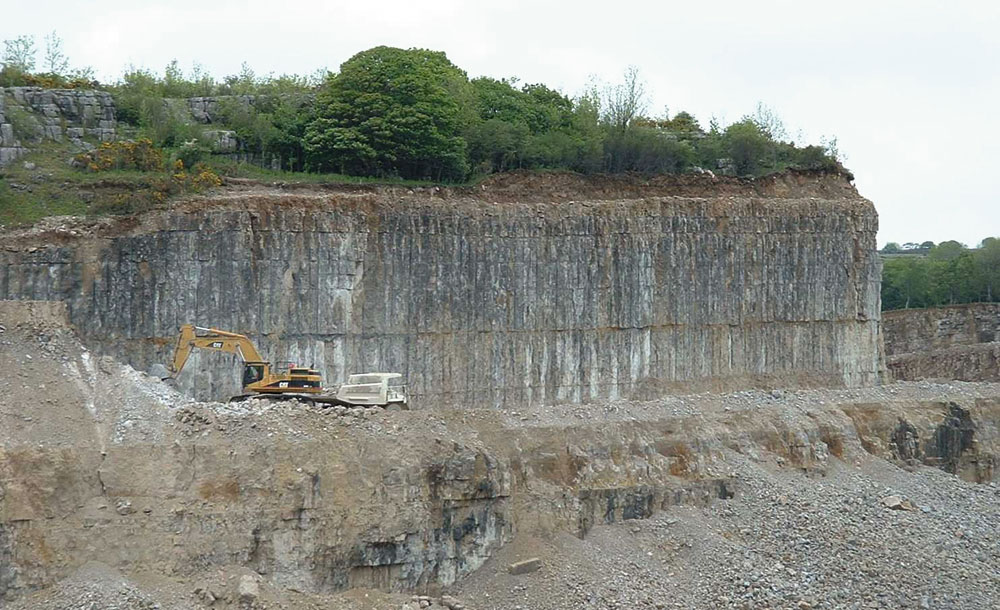
A review of available solutions
The authors, David Gibson, Ian Christie and Glyn Barnes, are business development manager, drilling and blasting manager and contracts manager, respectively, with Ritchies
Within the 1999 Quarry Regulations there is a statutory requirement for owners of existing and redundant quarries to ensure that they are geotechnically stable. Owners and managers are taking, or will have to take, measures to carry out risk assessments to ensure that faces and slopes are, and will remain, safe.
Some owners have in-house geotechnical experts to carry out these risk assessments while others need to employ third-party consultants to do it for them.
Either way, in most situations if physical on-site work is required specialist geotechnical and/or drilling and blasting contractors will be employed to implement the remedial proposals needed. In some cases it is advantageous to have the specialist contractor involved from an early stage since the contractor often has extensive experience and knowledge of the latest techniques and materials. In addition, the contractor has the specialist personnel, plant and equipment on which the most economically efficient solutions can be based.
This article summarizes some of the latest techniques and materials available.
Investigation
Prior to any work taking place, it is essential that there is a good knowledge of the geology involved. This is a significant aspect of any planning and execution of geotechnical operations and is even more important when working at height.
Modern technology such as stereographic photography (usually from helicopters or distant observations) and analysis can assist in designing the solutions required and determining the safe and economical methods of work. Laser profiling, which is used extensively for quarry blast design, can also be a useful tool in this process.
Drilling and blasting
One of the problems created by modern blasting techniques and the quarry operator’s desire to make primary blasting as economical as possible has been the increased use of bulk emulsions. This has led to larger patterns, heavier blast ratios and larger shots. The outcome of this is final faces left in a less stable condition.
The mitigating factor that can be offered by drilling and blasting falls into two categories.
First, where current blasting operations are on faces approaching their extraction limits, techniques can be employed to provide long-term stability during production blasting. The judicious use of pre-split and smooth-wall blasting will result in faces and slopes that are durable and, dependent on geology, require minimal additional support and ongoing inspection. This approach is undoubtedly the most cost-effective, while also minimizing the risks of remedial work.
Secondly, where the problem is historical, either in working or redundant quarries, there are solutions that drilling and blasting can offer. The techniques available are not dissimilar to those previously mentioned but require detailed geotechnical input to design the final solution. New blasting techniques, such as the use of electronic detonators, allow quality work with improved control of throw, fragmentation and, if planning restrictions are onerous, better control of vibration levels.
The major problem encountered in historical terms is generally the lack of available space between the face and boundary, where quarry operators have tried maximizing reserves without due consideration to long-term face stability. The problem with this approach is that there will be occasions when drilling and blasting is not an option due to lack of burden or where new activities, such as house building, are just outside the redundant boundary.
Rock removal
Should blasting not be possible but removal of rock is needed then some form of scaling is required. Men working from ropes is common for this activity but the use of modern ‘cherry pickers’ and long-reach excavators provides increased safety during this hazardous operation.
The use of temporary blast netting will ensure that the scaled material is contained and cannot fall onto people or property below.
Support
The techniques employed by geotechnical contractors are wide and varied. In the case of rock slopes, rock fall meshes are frequently installed to ensure that weathered and loose material is contained when it falls. Rock bolts, soil nails and anchors provide support to faces and individual features. Sprayed concrete allows concrete to be placed without the need for difficult formwork and placing equipment, which is much more involved at height. Dentition may be provided by brickwork, stone masonry or sprayed concrete.
Recent developments in technology have seen tensioned surface meshes being specified by engineers. These meshes, such as Geobrugg’s TECCO mesh system, provide active support to soil or rock faces and are usually used in conjunction with rock bolts or, where soil slopes are to be stabilized, soil nails may be used.
Rock bolts and soil nails can be made of plain, galvanized or stainless steel bar; self-drilling hollow bar, such as Dwyidag’s MAI; or Ischebeck Titan bar. In recent years glass-reinforced plastic (GRP) and carbon fibre bar has been used, especially where corrosion or residual stray electric currents are a problem. Full double-corrosion-protected (DCP) bars and strands are used in critical rock bolting, and soil nailing, and for active ground anchors.
Geobrugg have introduced the SPIDER rock-protection system that is suitable for rock slopes and overhangs where there is an irregular surface or clearly defined sliding mechanisms. The SPIDER system comprises a factory manufactured spiral rope net which, like rockfall netting and TECCO mesh, is attached to anchors or bolts at the top of the area to be treated and then unrolled downwards and secured around the perimeter. Its high strength provides active support to the face or a feature such as an overhang or isolated loose block.
Protection systems
Traditionally, rock falls have been controlled by the use of rock-fall meshes. These have reduced in price in recent years and are readily available from a number of suppliers.
They are usually made from hexagonal twist-wire net and are often PET coated. Although mostly grey in colour, other colours are available, albeit usually at extra cost.
While much of the geotechnical work carried out at height is aimed at stabilizing or securing faces and cliffs, sometimes this is too difficult or uneconomic. In these cases rock-fall barriers can be installed either at the bottom of the slope or higher up above the road, railway or structure at risk from falling material.
Rock-fall barrier technology has moved on apace in recent years with the Swiss being at the forefront — a fact that is hardly surprising considering their Alpine topography. Specially designed rock-fall barriers, such as Geobrugg’s ROCCO system, are available with up to 3,000kJ capacity to meet Swiss government guidelines. To give some idea of what a 3,000kJ impact is like, it is equivalent to a 10-tonne block free falling vertically 30m. From October 2006 Geobrugg will be offering a 5,000kJ barrier certified to Swiss government standards, which is equivalent to a 16-tonne block free falling 32m!
Currently, the European Union is putting the finishing touches to the European Organisation for Technical Approvals document ‘Guideline for European Technical Approval of Falling Rock Protection Kits’. These are less onerous than the Swiss guidelines and allow different categories of barriers to be offered. The guidelines will be formally issued within the next couple of years but clients may specify barriers to the draft standards since the contents are largely finalized.
Personnel, plant and equipment
Operative training is something that any responsible employer takes seriously since not only does it assist with safe operations but also ensures that the work is done correctly in the first place and maximizes the financial return on expensive plant and equipment.
Some modern plant being deployed for drilling and blasting, as well as geotechnical work, is highly sophisticated. Rigs can be radio-remote controlled to ensure operator safety and some even automatically send condition and performance reports back to the office via satellite and the Internet. Outputs are optimized through computer-designed in-hole equipment and the use of modern steels and other materials.
Environment
With more and more emphasis being put on the environment, plus the desire to turn redundant quarries into nature reserves and public amenities, the use of ‘green’ solutions is becoming increasingly popular.
Retention of top soils and their reuse afterwards is laudable and expected. In addition, soil-retention geotextiles (either plastic or biodegradable such as jute or coir matting) combined with hydro-seeding can assist vegetation to grow in the most barren of environments. The use of open-mesh supports as opposed to sprayed concrete or other concrete structures will allow the development of all forms of flora to progress unhindered.
This active encouragement of green growth will also encourage birds and other wildlife and reduce the ongoing impact of the scar left on the landscape.
Working at height
Specialist geotechnical contractors are often required to work at height to carry out inspections and investigations, remove dangerous or unstable ground, secure weak and weathered faces, and install support systems and drainage. The areas where these services are required include railway and road cuttings and embankments, cliff faces, old quarry faces and new excavations.
This type of work needs safe and flexible means of access, not only for the operatives involved, but also for the workforce and public below.
With the implementation of the new Work at Height Regulations [WAHR] 1995, the emphasis placed on adopting safe method-related work processes has never been greater. Close liaison between consultant and contractor is fundamental to achieving safe solutions.
The innovative use of long-reach excavators fitted with remotely controlled drilling feed masts illustrates well the minimization of an operative’s exposure to working at height and eliminates the potential consequences of vibration white finger syndrome while maximizing programme benefits through the use of high-output plant. This technique contrasts with the traditional labour-intensive method of roped access technicians using heavy hand-held rock drills where all of the risks mentioned are heightened and programme output is slow.
Scaffolding, mobile working platforms, cherry pickers, long-reach excavators, cranes, rope-supported working platforms and rope access techniques are all used. For drilling operations, which are often used in geotechnical work, special lightweight drilling machines are sometimes deployed along with hand drilling.
In the case of rope-access work, reputable contractors use IRATA (Industrial Rope Access Trade Association) trained and certificated operatives to ensure the highest safety standards. Since the provision of access can often be a significant proportion of any project’s costs, rope-access techniques can replace traditional solutions and offer clients significant savings.
Rope systems are usually quick to install and dismantle, flexible and allow work to commence quickly and finish promptly, avoiding lengthy scaffolding erection and dismantling programmes. By removing operational and time constraints, rope access services are often able to extend the ‘time window’ available to undertake work.
Ensuring safety with this type of activity is paramount and the HSE’s current campaign with regard to working at height highlights the importance placed on robust working systems. With due regard to the CDM regulations, this begins with the client’s requirements, the preparation of the health and safety plan, followed by the contractor’s project management plan that incorporates method statements and risk assessments.
In conclusion, the quarrying industry has available to it a wealth of resources, techniques and experience to ensure geotechnically safe faces and slopes either in the short-term or as a long-term legacy.