A Digital Surface Remote Blasting System
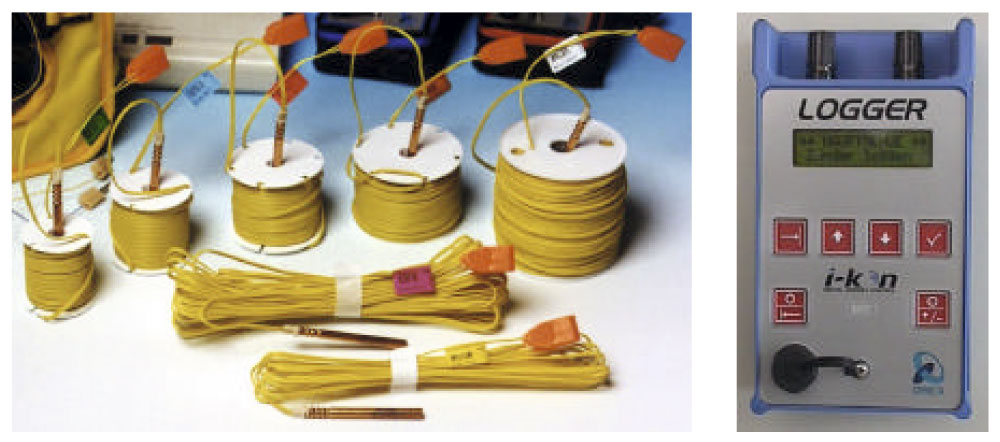
The advantages of using SURBS in quarries
By Dirk Hummel and Peter Reinders, R&D Electronic Blasting Systems, Orica Germany GmbH
The following article describes a newly developed Surface Remote Blasting System (SURBS) for electronic detonators, which is currently being introduced into surface blasting applications. The rationale for developing the SURBS was to meet key needs of mine and quarry operations, such as minimizing the site shutdown time and providing the capability to conveniently initiate blasts in difficult terrain from a safe distance. Increased distance from the blast, combined with a good overview of the blast site, provides maximum safety during blasting. The system also removes the inconvenience of running long firing cables.
The SURBS consists of the field-proven detonator and equipment technology of the existing i-kon electronic detonator system, a Surface Remote Blasting Box and a Surface Remote Blaster. The Surface Remote Blaster is the ‘master’ unit and controls the Surface Remote Blasting Box via encrypted radio communication using a sophisticated safety technology, which guarantees that the highest safety standards are maintained.
Five years ago Orica Mining Services launched their first electronic blasting system, ‘Digital Energy Control’. Since then many mines and quarries have successfully deployed the system, achieving significant advantages in terms of safety, cost and environmental compliance. However, the application of this original system requires a firing cable between the ‘Blaster’, at the point of safety, and the ‘Loggers’ and detonators at the blast site.
The new Surface Remote Blasting System makes hardwiring between the point of safety and the blast site a thing of the past, while allowing a remote blast initiation with the known precision and flexibility of the existing system. Instead of a single Blaster, which connects to the Loggers and detonators via the firing cable, the Blaster function is divided on to two new pieces of control equipment: the Surface Remote Blaster (Blaster2400R) and the Surface Remote Blasting Box (SURBB). The Blaster2400R is the master of the system and controls the SURBB via radio on a licensed and approved frequency. The SURBB is a slave to the Blaster2400R and supplies the firing energy to the attached Loggers and detonators.
All communications between the two units are encrypted using a digital single-use code for complete security, with the single-use encryption code carried on a Smart Dongle. The line-of-sight operating distance between the Blaster2400R and the SURBB is up to 2,500m (8,200ft). The units themselves are small, compact, portable and ruggedly designed to withstand the demanding conditions of surface mining and quarrying. The maximum system capacity is 2,400 detonators in a single blast.
The SURBS also has a test mode, which allows the strength and quality of the radio signal from various pit/quarry locations to be tested.
The benefits of using the SURBS in a quarry or open-cut operation are clear. Blasting will be safer because the blast can be initiated from a safe distance, well away from unstable ground and fly-rock. Blasting will also be more convenient, because there will no longer be any need to run a long length of firing cable often under time pressure in difficult terrain, across haulage roads etc. This will also contribute to cost savings, because with SURBS the shutdown time for blasting will be significantly reduced and mine/quarry efficiency will improve.
System components and operation of SURBS
Detonators and Logger(s)
The fully programmable electronic detonator can be programmed from 1 to 15,000ms in 1ms increments. The detonators are capable of two-way communication. Each detonator has a unique factory-assigned ID number, which is written to the detonator microchip. This is the basis for full two-way communication between the detonators and the control equipment, allowing the operator to test the detonators at all stages during preparations for a blast.
During hook-up of the detonators to a twin twist harness wire, the desired delay times are assigned to individual detonators by means of a Logger. The detonator is attached to the harness wire with a clip connector.
The Logger is capable of storing data for up to 200 detonators. When assigning delay times to the detonators, it can be operated in four different modes (Manual, Auto, Delay numbers or SHOTPlus-i), thus allowing the operator to choose the most convenient option for the application.
Surface Remote Blasting Box
After the detonators have been logged and tested, the Loggers are connected in parallel to the Surface Remote Blasting Box, which must be positioned a safe distance from the blast. A single SURBB can fire up to 2,400 detonators programmed via a maximum of 12 Loggers.
The SURBB provides the higher energy level required for programming and firing a blast. It is operated via encrypted two-way radio communication from the point of safety.
To activate the SURBB, the shotfirer needs a Smart Dongle. As part of the activation sequence the SURBB generates a single-use encryption code and writes it to the Smart Dongle. A successful activation sequence is indicated by the LEDs on the front panel, after which the SURBB is in standby mode. The operator can set the standby time up to a maximum of 4h. The blast must be fired within this time. If the standby time is exceeded the SURBB shuts down automatically and the single-use encryption code becomes invalid. During the standby mode no power is switched to the output terminals and the SURRB can only be addressed via radio by the Blaster2400R with the valid encryption code. With the start of the blasting sequence the two-way communication between the two units is continuously monitored. If the data transfer is disrupted, the SURBB will automatically default to standby mode. After firing, the SURBB shuts down automatically.
Surface Remote Blaster2400R
After activation the shotfirer must transport the Smart Dongle with the valid encryption code to the safe blasting location. This location will be at a safe distance from the blast but close enough that the shotfirer has a clear line-of-sight view of the blast site and its approaches.
The shotfirer then inserts the Smart Dongle in the Blaster2400R, which reads the encryption code. It is only after the Smart Dongle has been read that the Blaster2400R can communicate with the SURBB.
The entire blast sequence is controlled via full two-way communication from the Blaster2400R, and the shotfirer can continually verify that all the detonators are responding and fully functional, right up to blast initiation. Shotfirers can now easily position themselves to clearly view every blast, and will no longer have to rely on third-party information to verify that everything is clear before and after firing. Plainly, this remote blasting system will enhance the safety and convenience of blasting.
REFERENCES
- STIRLING, A.G.: ‘Digital Energy Control – A new tool for blasting’, Proceedings of the ISEE, 2002, vol. 1, pp. 439.
- HAMMELMANN, F., and P. REINDERS: ‘Electronic Blasting and Blast Management’, Proceedings of the EFEE, 2003, Prague.