New Mixing Technique for Mortar Plant
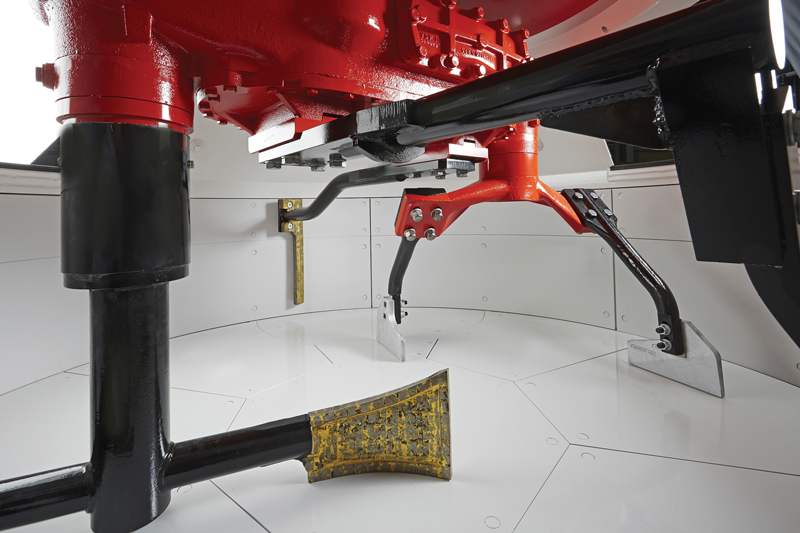
First published in the December 2015 issue of Quarry Management as Challenging Convention
Eco-Readymix adopt new Teka THT Turbine mixing technology combined with next-generation Hydronix moisture-control system
A substantial upgrade to a ready-to-use mortar plant has challenged convention by adopting a revolutionary new mixing technique for the first time in the UK mortar industry, combined with a novel system for controlling moisture in the batching and mixing process.
Eco-Readymix are long-established and well-respected producers of ready mixed-concrete, mortar and floor screed from two batch plants situated in the North West and Wales. The plant upgrade was driven by the company’s desire to use the most environmentally friendly manufacturing techniques to continually reduce its carbon footprint.
Eco-Readymix owner and industry veteran Gary Billington commented: ‘We maintain our position at the forefront of the industry through the pursuit of technology to constantly reduce our CO2 emissions. Mixing is at the heart of our process and I was keen to explore whether recent developments in mixing and batching technology could help us achieve our goal.’
Mixing
Producing consistently high-quality coloured mortar is challenging. Higher levels of mixer performance are required to ensure pigment is evenly blended throughout the all-fines mix. Ready-to-use mortar has traditionally been mixed in pan mixers in the UK, and although some planetary and twin-shaft mixers have been used, the vast majority of mortar plants still utilize the conventional pan.
As distributors for Teka mixers in the UK, ConSpare were one of the companies approached to assess the project. ConSpare’s engineering director, Steve Peterson, who visited site to conduct a detailed analysis of the application, said: ‘Teka offer four models of mixer, each with a completely different mixing action. We take a consultative approach and don’t jump to conclusions about which model mixer will perform best until we have all of the necessary data.’
Following consultation with the Eco-Readymix team and Teka’s technical department, ConSpare proposed the new Teka THT Turbine mixer for the project. Although a Turbine mixer has never before been used in the UK to produce mortar, the mixing action is well proven in other applications in plants across Europe.
THT mixers have a completely different mixing action to conventional mixers. The world-first, patent-pending MixTurbine mixing tool combines two sweeping arms to generate a new ‘swing and throw effect’, specifically developed to blend materials more effectively, particularly in mixes using a high proportion of fines or colour.
The shape of the turbine mixing tool causes raw material to accelerate across the face of the mixing arm as it rotates, powerfully sweeping the mix from one side of the pan to the other. Every full cycle of the MixTurbine causes maximum raw material movement for minimum rotation. This constant ‘throwing’ action produces a highly intensive mixing effect.
The project assessment highlighted a number of advantages where the new mixing action could potentially help achieve Eco-Readymix’s objectives, such as:
- Shorter mix times, faster discharge and less ‘pushing’ of the mix resulting in lower power consumption
- MixTurbine mixing tool reduces the risk of cross-contamination of different coloured batches resulting in less wastage
- Turbine mixers produce small batches, down to 15% of theoretical batch size, without compromising mix quality, thereby offering far greater production flexibility
- The combination of fewer mixing tools and low MixTurbine rotation speed creates less wear, reducing the need to enter the pan and resulting in a safer working environment
- Low-profile mixing tool design leads to less build-up on the MixTurbine blade for easier, quicker cleaning.
Batching
The mortar plant upgrade project included a review of moisture-measurement techniques. As master resellers for Hydronix, ConSpare were able to offer a full package. The success of this type of project relies on integrating mixing and batching technology, so having expertise in both of these crucial areas is essential if plant performance is to be optimized.
Steve Peterson, who proposed replacing the existing moisture-measurement system as part of the overall upgrade package, explained: ‘You can have the best mixer in the world, but if proportions of raw materials are inconsistent it is not possible to produce a consistently high-quality mix. If Eco-Readymix were going to invest in the latest mixing technology, we felt it was important to make sure they got the best return on that investment and, based on our experience, accurate moisture-control techniques are essential.’
The timing of the project was fortuitous as it coincided with the launch of a new range of Hydronix moisture sensors. The upgraded digital sensors offer next-generation measurement techniques and far greater flexibility for integration into plant control systems. The new developments simplify calibration and reliability.
ConSpare proposed to incorporate the new sensors into the upgrade, including:
- Hydro-Probe sensors in each of the four sand bins to feed moisture data to the Cantech control system via a Hydro-View interface panel. Raw material batch weights to be adjusted to compensate for sand moisture levels, ensuring consistently accurate raw material batch sizes. Water addition to be adjusted to the precise level required to achieve the desired mix design.
- Hydro-Mix sensor installed in the mixer floor to provide real-time information to the batcher through a second Hydro-View interface panel to monitor mix consistency and homogeneity. Once the target moisture level is achieved the mix can be discharged immediately, reducing the risk of over-mixing and wasted power consumption.
The decision was made to replace the existing pan mixer with a Teka THT1875 Turbine mixer and to replace the existing moisture-control system with the new Hydronix system. The installation was undertaken in January 2015.
Conclusion
The mixing action generated by the MixTurbine mixing tool proved to be ideal for mortar production. Gary Billington commented: ‘We immediately noticed a significant improvement in the quality of both mortar and screed. Mix quality was vastly improved – perfect mortar with a butter-like consistency that our clients love as it is so easy to work with.’
After nine months of arduous production the mixing tools show virtually no signs of wear, indicating that maintenance downtime and spare part costs are set to be permanently reduced.
One of the most significant changes has been the production flexibility which the Turbine mixer allows. ‘We can produce a full batch or a single tub of mortar and the quality is exactly the same,’ said Mr Billington. ‘We have the flexibility to deliver what the customer wants, when they want it, without the difficulties we used to experience making small batches, which has reduced wastage. It is far more efficient for us and better service for our customers.’
Although the mixer is proving very successful, the contribution of the Hydronix equipment cannot be underestimated. Accurate batching ensures the mixer performs to the best of its ability.
The existing ammeter-based workability control system, which is widely used throughout the industry, relied upon measuring the change in running amps of the mixer from empty-load current to full-load current. Pan mixers tend to see a large increase in amps as raw materials are loaded, facilitating this kind of measurement system.
Once the Teka THT mixer was introduced to the plant the difference in mixing efficiency soon became apparent. The mixer drive system and high-efficiency mixing action meant there was very little change between empty running and full-load current, rendering the old ammeter-based system ineffective. The Hydro-Mix mixer sensor measures moisture in the mix, not amps, and therefore is unaffected by low running amps, providing consistently accurate workability control. Also, lower power consumption during the mixing cycle delivers precisely the low-carbon mixing which Eco-Readymix were trying to achieve.
Gary Billington is so convinced of the improvements which the latest mixing technology has delivered that he has already committed to upgrading the other Eco-Readymix plant. The upgrade to a Teka THT3000 Turbine mixer will go ahead in January 2016.
Summing up his thoughts on the project, he said: ‘The Turbine mixer was new to our industry and we took something of a risk investing in this new technology, but I’m very pleased that we did. Our customers are impressed and we have been able to make greener mortar. The ConSpare Engineering Department have worked with us throughout the process and demonstrated that they really do understand what it takes to make better mortar. We were not intending to upgrade our second plant at the start of the process, but I cannot ignore the benefits.’
For further information visit: www.conspare.com
- Subscribe to Quarry Management, the monthly journal for the mineral products industry, to read articles before they appear on Agg-Net.com