Microwave Moisture Measurement
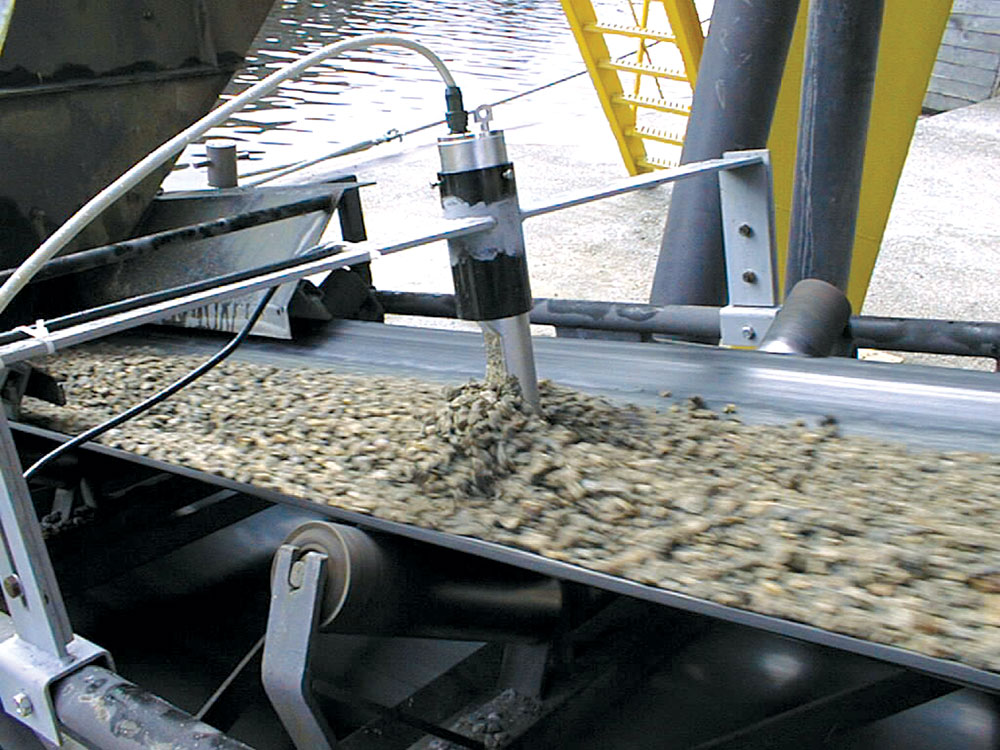
The latest digital online moisture measurement is not only critical to the production of quality concrete, but also financially beneficial, as Rolf Laffan, chairman of Hydronix Ltd, explains
Sourcing suitable raw materials within an acceptable distance from quarry to plant is of prime importance to manufacturers dealing with the production of concrete and asphalt. However, the supply of these high-quality raw materials can be limited by the geology of the accessible area.
Increasingly, to help address this issue, the advantages of microwave moisture measurement systems in concrete, asphalt and aggregate applications are now not only considered beneficial, but also essential: both in terms of aspect of quality control and also the cost savings that can be achieved.
The ability to measure and quantify the amount of water present in bulk materials, such as sands and aggregates, was, in the past, extremely limited by the use of flawed technology. All the techniques used, whether infrared, electrical conductance or even nuclear, had significant shortcomings and disadvantages. The introduction of the microwave technique into the concrete industry in the late 1980s and early 1990s was the first major breakthrough.
Up to now, the industry that, worldwide, has benefited most from the implementation of moisture measurement systems using digital microwave technology, has undoubtedly been the concrete industry. The need to produce consistent quality concrete to a rigorous specification is ever increasing in line with the continuing developments in mix-design technology. In simple terms, what the end-user is seeking is a concrete with a consistent workability/slump that attains a consistent strength; whether it be a semi-dry mix for the production of paviors or a self-compacting concrete for on-site use.
One of the major causes of inconsistency in the batching of concrete is the ever-varying moisture content of the sand and aggregates from one batch to another. This may be ameliorated by adopting good housekeeping practices, but even for materials stored in covered silos the moisture will be forever changing due to the inevitable effects of drainage. Moisture content in stored sand and aggregates can have dramatic effects on the water/cement (W/C) ratio, the aggregate/cement (A/C) ratio, yield and the colour of the mix.
Hitherto, considerable attention had been given to the capability of the batching system to weigh to an accuracy of around ±0.5% without appreciating that variations in the moisture content of the raw materials could easily introduce errors of up to ±2.0%, and in many instances very much more.
Today, however, this is a readily solvable problem. Designers would no more think of building a batch control system without a microwave moisture sensor system than building it without a computer.
Microwave moisture measurement systems were first introduced into the concrete market 25 years ago by an innovative UK company who received the much sought after British design award in 1992. This new product development fortuitously coincided with the computerization of batch controllers, making it possible to integrate the two systems. This allowed the batch control system to:
- Provide online (real time) weight correction to compensate for the variable amount of water being weighed, thereby ensuring a consistent dry weight of material. This provides mixes with consistent A/C ratios.
- Make sure that the appropriate quantity of water is added to the mix to ensure consistent workability and, in conjunction with 1. (above), consistent W/C ratios.
The above aspects of moisture measurement apply equally to other applications, such as asphalt, where there are three significant benefits:
- optimizing the use of the binder
- maintaining a consistent grading when blending aggregates
- saving energy in the drying process.
With fine sands holding between zero and 25% moisture, an asphalt producer will benefit by correcting the fine sand weight for moisture on a real-time basis. By measuring the inputs it is possible to effectively correct the aggregate grade proportioning in real time, tackling and resolving the cause of the problem rather than simply measuring and dealing with the symptoms. This will greatly improve the consistency of the materials entering the process.
Measuring the moisture of the blended aggregates on the cold-feed belt will allow the burners to be controlled to optimum efficiency, thereby saving considerable energy. This information may also be used to compare the ‘burning efficiencies’ of various plants, hence assisting in the selection of the most efficient burners for the process.
By measuring and controlling the moisture of the inputs, the correct recipe and a known volume can be maintained. This effectively ensures that the asphalt cement, RAP, binder and other inputs are correctly proportioned and ensures that the producer is maximizing the use of the materials by ‘running lean’ and to specification.
Once again, moisture measurement provides improved quality of product with financial savings.
The success of the microwave technique hinges on the unique properties of the water molecule, which resonates at certain frequencies when subjected to a microwave electromagnetic field. This is exemplified by the microwave oven, in which the water molecules absorb so much energy when resonating in an electromagnetic field and heat up to such an extent that they heat and cook the surrounding food.
Such is the success of this technique that it has now been adopted in one form or another by nearly all suppliers of moisture measuring equipment. Technology moves on, however, and more recently the original pioneers of the microwave technique have developed moisture sensors utilizing a ‘digital’ microwave technique. This, they claim, allows these sensors to measure more accurately over a wider range of moisture contents than had been possible hitherto. Other side benefits include ease of communication and ease of calibration.
As with most things, once an idea is found to be successful, new manufacturers start to appear. So, when investigating possible suppliers of moisture measuring sensors or systems, what are the criteria for selecting a suitable system? Each manufacturer will claim that their system is better than their competitors’ products, which can lead to confusion over which system to choose. Some might opt for a cheaper product and hope it works, while others will pay a bit more for a reliable product with a proven track record of good customer service and support. When choosing the right system for a particular requirement, it is important to ensure the system offers:
- An accurate system of measurement, almost certainly microwave, with a possible preference for a ‘digital microwave’ technique.
- Sensors, whether for measuring in bins, conveyors or in concrete mixers, must have a proven track record of robustness, reliability and longevity. One well known company has over 40,000 sensors installed in over 50 countries around the world.
- Ease of integration with the main control system, if being supplied separately or as an addition to an existing system.
- Ease of calibration. No matter how accurate the sensors may be, they are useless if incorrectly calibrated.
- Good after-sales service and technical support. This is possibly the most important consideration. A system, no matter how good it may be, is of little use if it is not working, cannot be fixed and help cannot be obtained. Examine the reputation and track record of the supplier.
Concrete and asphalt manufacturers are no longer asking the question: ‘Do I need moisture measurement?’, but rather: ‘Which system should I choose?’ Practical experience from end-users has confirmed that the cost savings achieved will, in many circumstances, pay for the investment within months. Clearly, these figures are dependant on many factors, such as the type of concrete being produced, the yield of the plant etc. However, once installed and up and running, most operators will be well satisfied by the difference it makes to their concrete and their profits.