MachineGuard
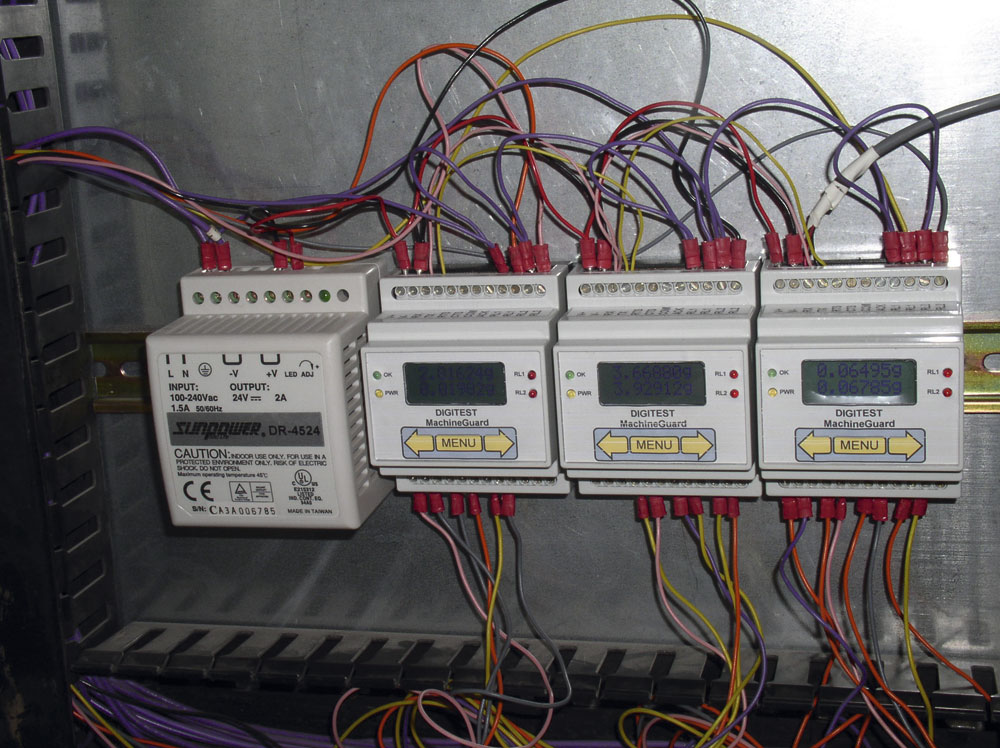
Live, condition-based monitoring of critical plant and equipment
One of the biggest challenges facing the manager of any major quarry is ensuring that the plant remains operational and productive throughout the course of every working day. Unplanned downtime as a result of machine failure can be enormously expensive and have a significant effect on the plant’s output and profitability.
One common source of downtime in the quarrying industry is premature failure of vibratory screen bearings. Vibratory screen bearings are notoriously difficult to monitor continuously and their failure can cause the plant to come to a complete standstill while the offending items are stripped down and replaced.
After continuous problems of this nature, a major UK aggregates company decided that they needed to find a better solution and somehow implement a ‘live’ condition-based monitoring system. This was the challenge they set their existing condition-monitoring company, Drive Management Services (DMS), a specialist power-transmission consultancy that provides a range of total asset management services and products designed to help clients manage their critical plant asset reliability and efficiency.
The challenge
On discussing the requirements with the engineering manager, it was agreed that a number of key components would need to be delivered if the solution was to be effective:
- Continuous 24h-a-day monitoring.
- Multi-level, complex alarms to identify specific events.
- RS485 serial communication.
- Information delivery in real time.
- Simple but effective information that could be interpreted easily.
In addition to these requirements, the system had to be affordable and not cost-prohibitive.
The solution
Having reviewed the specific requirements outlined above, DMS recommended the implementation of their leading-edge condition-based monitoring system, MachineGuard.
MachineGuard has been specifically designed and developed by DMS as a simple, effective and affordable system for continuously monitoring critical plant and equipment. Modular in nature and simple to install, one of its key features is its flexibility to monitor all, or a combination of, the following conditions:
- vibration
- oil condition
- oil temperature
- motor current
- temperature
- any 4–20mA signal.
These features allow engineers to understand the ‘bigger picture’ when problems occur and assist in quickly identifying the root cause.
For the purposes of the aggregates company concerned, MachineGuard was installed to monitor three pieces of critical plant: vibratory screen no.1 (monitoring the screen DE and NDE bearings, as well as the drive motor DE bearing); vibratory screen no.2 (monitoring the screen DE and NDE bearings, as well as the drive motor DE bearing); dust exhaust fan unit (monitoring the motor NDE and DE bearings (radially) as well as the motor DE bearing axially).
The software control panel for MachineGuard was installed on a laptop computer in the engineering office and on the control room PC. The system was initially set up to warn the plant operators by a series of simple local alarms, such as flashing lights inside the control room. By setting up the system in this way, the customer was given complete control of the monitoring system, with instant access to up-to-the-minute data on the condition of critical plant.
In addition, DMS decided to fast-track the development of a GPRS component to the system. This additional functionality allowed DMS to provide a ‘live’ monitoring capability from their own offices in Sheffield and an ability to advise the plant manager of any change in bearing condition as and when it occurs.
The benefits
Within two months of its installation the aggregates producer derived some tangible benefits from the new system with two separate early-stage warnings.
First, in early February 2006 DMS received an SMS text message alerting them that the no. 1 screen DE bearings were displaying high levels of vibration, suggesting that they were in failure mode. DMS immediately contacted the plant manager to inform him of this condition with the result that the bearings were replaced that weekend, in a controlled manner. When the spherical roller bearings were removed, the deterioration was obvious — the result of water and dirt/dust particle contamination. The bearing outer race also showed signs of fatigue due to excessive out-of-balance loads. This failure mode was confirmed in an independent report by a leading bearing manufacturer.
Secondly, towards the end of February, the dust exhaust fan bearings began to show signs of serious deterioration. DMS had monitored these bearings over a period of time and contacted the aggregates company to inform them of this condition. DMS were advised that the company had been increasing the fan speed above that normally associated with this fan in an effort to alleviate the problem of filler material getting into the hopper. With this early warning, the quarry was able to order a new bearing to cover any eventuality and was also able to slow the fan speed back to the correct setting, without damaging the fan bearings further. The screen data from this application is shown in figure 1.
The software supplied and installed with MachineGuard offers the client the following features: trends display of all parameters relevant to each separate area of machinery, and on screen analysis; automatic housekeeping including routine capture of logged data and event logging of significant events; easy export of data into a spreadsheet or database applications for further analysis or reports; simple point-and-click interface giving context-sensitive menus; compatibility with Windows 95, 98, 2000 and XP.
Other key features include:
- Ability to monitor four channels per unit.
- Multi-level complex alarms to identify specific events.
- RS232, RS485 and multi-drop communications.
- Wireless communication.
- GPRS connectivity.
- Can be observed remotely.
- Can be monitored and controlled locally.
- Can be connected to a PC online/offline.
- Compact design, DIN rail mounted and can be used to monitor several machines by installing multiple MachineGuards.
- The unit is real-time date-stamped internally, with the capacity to log over 16,000 records.
- The unit can be auto self-configured and changed from a remote PC. It can also be configured for high-frequency logging.
- Simple traffic-light system icon for each machine or section of plant being monitored.
- Can be installed with built in alarms: local, eg klaxon/ flashing lights; or PC warnings, text messages, emails, faxes etc.
Drive Management Services Ltd, Unit C1, Sheffield Technology Parks, Don Valley Site, 60 Shirland Lane, Sheffield S9 3SP; tel: (0845) 838 6710; e-mail: allan.findlow@dmsinteractive.co.uk