Wolverhampton gets its first recycled rubber road
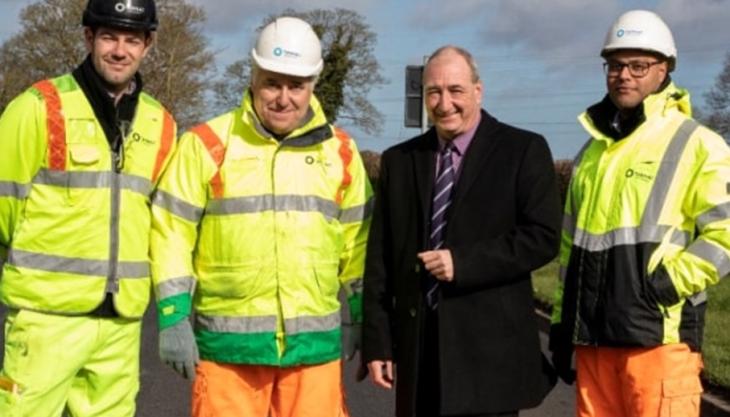
City leads the way with first trial of Tarmac’s rubber-modified asphalt in the Black Country
THE City of Wolverhampton Council, in partnership with Tarmac, has now laid a new type of sustainable asphalt that uses rubber crumb from the 40 million waste tyres produced every year, to support environmentally friendly roads in the city.
Northcote Lane is the first road in the city of Wolverhampton to trial the new asphalt technology, using recycled waste tyres as a sustainable alternative to resurface local roads.
Each tonne of asphalt incorporates one used tyre, therefore depending on the thickness of the layer, approximately 500 tyres can be used in each kilometre of carriageway.
The surface is laid at a lower temperature which means roads can be reopened quicker with up to 10% less CO2 emissions, improved site safety, reduced fumes and less risk of burns to workers.
Councillor Steve Evans, Cabinet Member for City Environment at City of Wolverhampton Council, said: ‘It’s great to see innovative solutions to repurpose these tyres that could otherwise have to be exported if no other use can be found due to the European landfill ban introduced in 2006.
‘We were the first local authority in the Black Country to declare a climate emergency and we are keen to explore ideas that can reduce our carbon footprint and improve our environment.
‘This technology will provide a safe surface with less emissions and reduces disruption during the laying process, which is a fantastic move towards achieving our carbon-neutral target.’
Brian Kent, national technical director at Tarmac, said: ‘Our innovative rubber-modified asphalt technology takes advantage of one of the UK’s most significant and overlooked waste streams – used tyres. Every single day in Britain alone, some 100,000 worn tyres are removed from vehicles and sent for recycling or export.
‘The City of Wolverhampton has taken the lead in delivering sustainable highways solutions in the Black Country by leveraging this pioneering technology and unlocking the benefits provided by a circular economy approach.’