Schaeffler UK extend condition-monitoring services
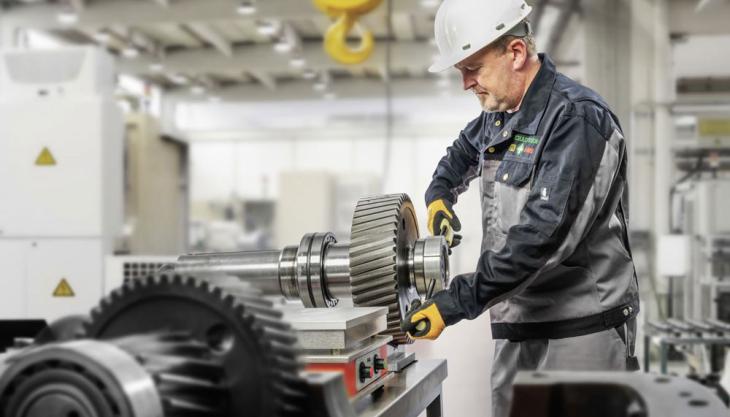
Company offers wider range of condition-monitoring and vibration analysis services for mines and quarries
PRECISION bearing manufacturers Schaeffler UK have extended their range of condition-monitoring (CM) services for the UK market.
With their combination of expertise in bearing failure analysis, vibration monitoring, fitting and maintenance of bearings, and their own portfolio of condition-monitoring equipment, Schaeffler UK say they are uniquely positioned to offer CM services to a wide range of industry sectors, including mining and quarrying.
The range of services now offered by Schaeffler UK includes condition monitoring using both online and patrol monitoring, vibration analysis, thermal imaging, bearing failure analysis, bearing mounting and dismounting, training and consultancy.
The aim of these services is to help plant operators (MRO) and plant manufacturers (OEM) to reduce the operating costs associated with rolling bearings, increase plant availability and reduce total cost of ownership (TCO).
Although most companies have an in-house maintenance department responsible for the condition monitoring of plant and equipment, many require external help from an expert when it comes to analysing vibration data obtained from CM equipment, particularly for process-critical plant and machines.
David Goves, application engineer at Schaeffler UK, commented: ‘Our condition-monitoring service is a unique offering to UK industry, combining the specialist knowledge, skills and experience of our engineers.
‘As manufacturers of bearings ourselves, we have the specialist bearing knowledge, condition-monitoring products and vibration analysis skills to help customers get the most from their rotating equipment.
‘We typically work closely with the customer’s maintenance or plant engineers, assisting in their predictive maintenance regimes and helping to reduce production downtime and increasing plant availability.’
Schaeffler UK’s condition-monitoring services include:
Vibration analysis
Vibration monitoring can be applied to any type of rotating plant or machines that use rolling bearings. These include electric motors, drives, gearboxes, fans, pumps, cranes, conveyor systems and other mechanical handling equipment.
Schaeffler UK offer a comprehensive range of equipment to monitor plant condition and a vibration analysis service, either on a one-off consultancy basis or as a regular contract-based service.
The most important part of the service is an asset condition report that clearly identifies what maintenance action is required. An exception report is left with the customer prior to leaving site, which indicates where any immediate action is required.
Patrol monitoring can also be provided, including any machine identification and asset mapping that may need to be carried out first. This can provide the customer with the necessary data with which to plan a suitable patrol monitoring route for a plant.
Thermal imaging
Thermography is one of the most important non-destructive diagnostic techniques. Many technical issues manifest themselves in the form of heat generation, which can be detected using high-resolution infrared cameras.
Schaeffler UK can provide thermal surveys of plant equipment such as electrical control panels, rotating equipment and machines. These thermal surveys can be very useful when used in conjunction with vibration analysis.
Training
Schaeffler UK offer a range of training courses either on site at the customer’s premises or at the Schaeffler UK training centre in Sutton Coldfield, West Midlands.
Courses offered include one-, two- and three-day training for managers, engineers and technicians involved in the selection, operation and maintenance of rolling bearings, as well as condition monitoring, vibration analysis, bearing failure analysis and mounting of rolling bearings.
While training takes a modular approach for ease of selection, courses can be tailored to meet the specific requirements of the customer where necessary.
Bearing mounting and dismounting
Schaeffler UK can also provide customers with a complete on-site bearing replacement service, including bearing mounting and dismounting.
The correct mounting and dismounting of rolling element bearings can save time and significantly increase the life of bearings, as well as maximizing the availability of critical plant and machinery by avoiding costly breakdowns.
The key is to ensure that the appropriate tools and equipment for the mounting and dismounting of rolling bearings are on hand for the engineer at the installation or assembly stage.
The Schaeffler Mounting Toolbox is a web-based information guide on how to professionally install rolling bearings.
As well as learning about which tools and fitting aids are required to install rolling bearings, users can also view short educational videos that demonstrate how these tools should be used in practice.