Lafarge Cement select Trolex pressure sensors
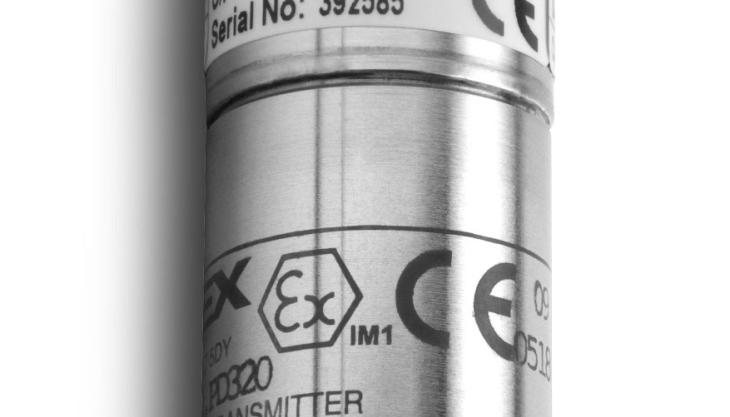
Trolex pressure sensors installed as part of kiln process cleaning system
Trolex pressure sensors have recently been installed at Lafarge Cement in Derbyshire, as part of an upgrade to their kiln process cleaning system.
The two kilns each have their own cleaning systems and 80 of the Trolex TX6114 pressure sensors have been used in each system. The Lafarge cleaning process comprises air blaster cannon systems to fire automatically at regular intervals to blast any build-up of material such as shale, limestone and clinker that may settle in the kilns.
The Trolex pressure transducers monitor the pressure lines and measure the pressure in the cleaning air pressure vessels providing analogue trends of the cleaning cycle pressure. This allows Lafarge to view the discharge and re-charge of the vessels and the trends provide diagnostic information for analysis of system efficiency and operation.
Commenting on the installation, Mark Bramley of Lafarge said: ‘The original control equipment had become obsolete and unreliable and did not give the operators the required information to enable them to maintain its function. We chose Trolex pressure sensors as our previous experience has shown them to give consistent accuracy, robustness and reliability, and the new equipment continues to meet our expectations.’
The Trolex TX6114 pressure sensor is a proven product that has had many applications around the world from mining and chemical processing to medical engineering. The low-cost high-performance sensor has a stainless steel housing that is chemical and corrosion resistant. The sensing capsule is completely resistant to the most severe and aggressive products and is particularly suitable where frequent cycling is required. The pressure sensing element, with integral four active arm strain gauge, provides an exceptionally stable output signal with negligible zero drift and remarkable over-pressure capability. It is two-wire, loop-powered, 4…20 mA analogue output and is fully temperature compensated. It has full ATEX M1 approval and is group 1 and group 2 intrinsically safe.