Improved performance and versatility with ROC L830
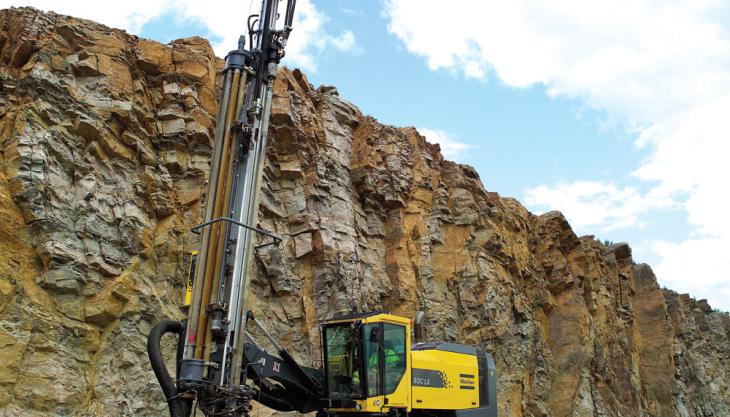
First introduced in 1999, Atlas Copco’s ROC L8 down-the-hole drill rig has become a popular choice in quarries and open-pit mines thanks to its high performance and ability to cope with a number of different drilling applications. Recently, however, the ROC L8 has undergone a number of significant changes to reduce its weight and further increase its performance and versatility, resulting in the introduction of the ROC L830.
The ROC L830 operates at up to 30 bar pressure and comes with a choice of two different drill tube lengths; long feed for 6m drill tubes or short feed for 5m drill tubes and toe-hole drilling capability. Overall drilling capacity has been improved due to the increased operating pressure, as well as through the use of a special cylinder feeding and tube-handling system that can accommodate up to 140mm diameter drill tubes. Atlas Copco say the penetration rate of the machine is up to 30% greater than previous models.
Equipped with a 402kW Tier 3 engine and a 470 litres/s high-pressure, two-stage Atlas Copco compressor, the ROC L830 is capable of drilling with hammers up to a maximum diameter of 203mm.
The rig features a comfortable ROPS/FOPS cab equipped with a new, easy-to-use display unit complete with GPS-based angle and hole depth readings, laser plane capability and auto-stop at the desired hole depth, allowing blastholes to be drilled accurately and exactly according to plan. This, in turn, results in increased production of excavated material thanks to smoother benches and better fragmentation control.
Meanwhile, Atlas Copco say their radio remote controlled (RRC) drill rigs are among the new stars in the drilling world, thanks to the greater operator safety, terrain ability and productivity they offer.
Using radio remote control, the operator can manoeuvre the drill rig from a safe distance while having the best possible view of the operation. All functions, such as tramming, drilling and rod handling, can be controlled from the RRC unit, with the stepless controls providing the smooth, precise movements required when positioning the drill rig.
Atlas Copco say that by using their ROC D7RRC rig, operators can easily gain access to sites that would otherwise be considered inaccessible. By combining RRC with a rig that has a low centre of gravity and a hydraulic support leg, high levels of stability and safety are achieved, while ground clearance of 455mm provides manoeuvrability in rough terrain.
The ROC D7RRC is also equipped with Atlas Copco’s folding boom, which is centrally located with a low mounting point for optimum stability and maximum coverage. The versatile boom head allows the drill feed to be set up in many different positions, including high-reach for rock-bolting applications or applications that require horizontal drilling.
The machine also features the combined power of a COP1838 rock drill, a high-performance Caterpillar engine and an Atlas Copco compressor that delivers efficient hole cleaning. The rig is also equipped with Atlas Copco’s patented automatic drill stop, which stops the drilling and loosens the rod threads at a preset depth.
Atlas Copco Construction & Mining Ltd, PO Box 79, Swallodale Lane, Hemel Hempstead, Herts HP2 7HA; tel: (01442) 222100; fax: (01442) 234467.