Bardon Asphalt clean up with BagVAC
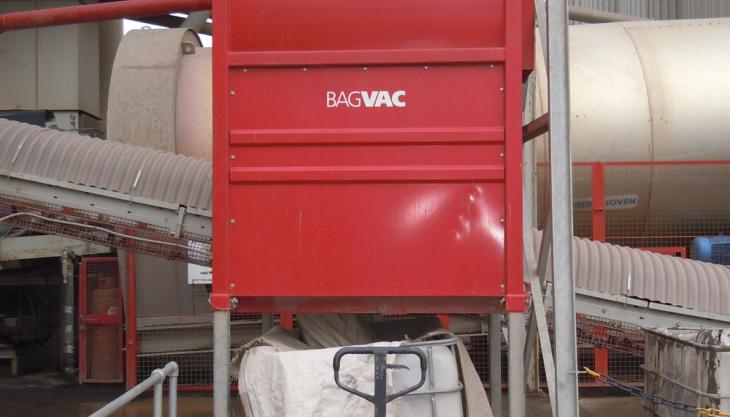
Aggregate Industries use a Gotland BagVAC system at Leicestershire asphalt plant
Aggregate Industries have been using a Gotland BagVAC for several years, exploiting its dust-removing capabilities to minimize manual-handling issues and dust exposure risks at their Bardon Hill asphalt plant at Coalville, Leicestershire.
Bardon Asphalt, part of Aggregate Industries UK Ltd, are one of the leading asphalt suppliers in the United Kingdom, and supply a full range of both British and European Standard products and proprietary products for the transport and construction industry.
A key feature of the asphalt plant at Bardon Hill resulted from the decision to equip it with a centralized vacuum system, designed and supplied by Gotland, with inlet valves around each of the six levels of the asphalt plant for attaching a length of flexible suction hose. A Gotland BagVAC then supplies the suction power so that all the dust and build up that inevitably results from asphalt production is sucked away into large one-tonne IBC containers.
The Gotland system is said to provide a number of benefits, from minimizing dust through its fully enclosed system from nozzle to bag, and the avoidance of manual handling risks, along with improving Bardon Asphalt’s own health and safety and general housekeeping standards.
Jason Broughton, Bardon Hill’s asphalt plant manager, commented: ‘The BagVAC dust-removal system is used for the internal cleaning and dust removal of our Benninghoven asphalt plant. This means working around and up on seven levels internally, via the connectors we have on all levels for sucking all the dust away into the BagVAC system.
‘Prior to commissioning and installing the BagVAC system, there was a serious manual-handling issue. Bags were filled and removed by hoist on level six – using internal stairways. As a direct result of this laborious and unpopular chore, the housekeeping of the plant interior was left to become one of the last things anyone had or wanted to do.’
Bardon Asphalt use the BagVAC system on a weekly basis to maintain their housekeeping standards with the plant internals. They report that it is user friendly and greatly reduces the time spent on the cleaning and housekeeping tasks compared to manual removal, based on volumes found and spillages – as many as four levels of the asphalt plant can now be completely cleaned in a day.
‘The BagVAC has made a big difference to achieving higher on-site environmental standards and it has improved our general house keeping standards. All in all, the BagVAC system is an excellent piece of kit that has effectively removed other critical issues like manual handling of bags with filler fines. It has made housekeeping easy and allows us to maintain the high standards expected on site’, concluded Jason Broughton.