Another AggreSand 165 wash plant for Leiths
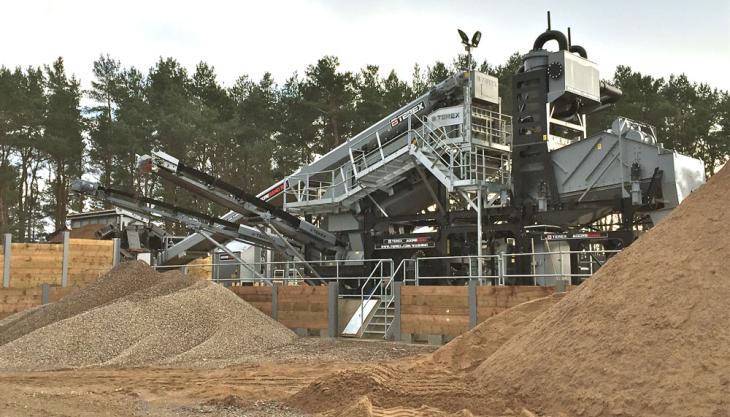
Blue Scotland supply quarrying business with second TWS modular wash plant in three years
THE Leiths Group, a multi-discipline organization and one of Scotland’s largest privately owned quarrying and civil engineering businesses, have recently taken delivery of their fourteenth piece of plant from Blue Scotland in the last three years. As a long-standing customer this now officially places Leiths as Blue Scotland’s biggest purchaser over that period.
Leiths are a long-established family business with their head office in Aberdeen. The company is primarily engaged in quarrying operations but is supported by an extensive construction and surfacing division, precast factories and five other subsidiary companies, namely Joss (Aberdeen) Ltd, A Ross & Sons Ltd, Lawrie Demolition, Markon and M&M Road Surfacing Ltd.
Leiths currently operate 10 hard rock quarries and four sand and gravel operations throughout Scotland, offering a wide range of products to a continually expanding customer base. As well as traditional quarry products, such as sand and gravel, aggregates, concrete and asphalt, Leiths also manufacture more specialized materials such as rail ballast, limestone filler, agricultural lime, animal lime feeds, road surface dressing chippings and decorative aggregates.
In 2014 the company purchased its first Powerscreen machines – a Chieftain screen, a Warrior screen and three Maxtrak mobile cone crushers – to work at various quarries located throughout Scotland. Since then the company has further invested in a Terex Washing Systems (TWS) AggreSand 165 wash plant, which is located at Midlairgs Quarry, near Inverness, as well as three more Powerscreen machines and an MDS 515 trommel.
The latest addition to Leiths fleet of equipment is a second TWS AggreSand 165. This fully modular wash plant is capable of handling more than 200 tonnes/h of quarried sand and gravel feed material to produce a range of different aggregates and sand, meaning it can adapt to customer demand.
Feed material is loaded into a 9 cubic metre capacity hopper feeding an inclined conveyor that transports the material to the first stage of the washing process, a 4.8m x 1.5m, two-bearing, triple-deck rinsing screen. Each of the screen decks is fitted with polyurethane modular screen media and individually controlled spray bars that wash and separate the material to leave high-quality aggregates.
The remaining fine fraction is pumped into a cyclone system that retains any material greater than 75 microns in size and produces two grades of sand. The residual material moves on to a lagoon to be filtered, with the resulting clean water being recirculated into the system, thereby improving water recycling and reducing process water waste.
Commenting on the new Terex washing system, managing director Grant Milne commented: ‘The new wash plant has recently been commissioned and will totally transform the capability of Netherpark Quarry, in Aberdeenshire. We know demand for products from the quarry will grow and the equipment will help us fulfil this increase.’
Blue Scotland sales manager Al Rees said: ‘Leiths have been a very loyal customer over the years and we greatly appreciate their support. The guys there are very knowledgeable about their industry and know exactly what kind of equipment is best suited for the task in hand. It is therefore testament to the quality of Powerscreen and Terex Washing Systems that they choose their equipment.’