Tracking and Tracing Explosives
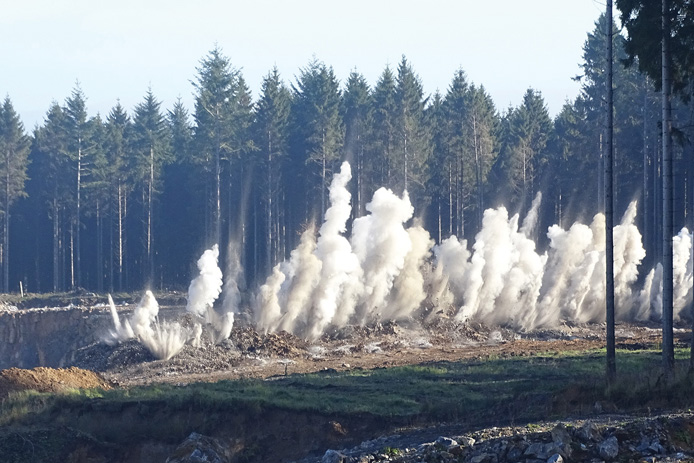
First published in the March 2016 issue of Quarry Management
Practical experience with the Ontaris explosives stock book at a quarry in Germany
It is 7.00am in the morning at Alme Stone Quarry in North Rhine-Westphalia, Germany. There is a truck with a delivery of explosives in the yard. The explosives are being unloaded by fork-lift and placed in the bucket of a wheel loader, which will take them to the blast site.
Alfons Planken, blasting specialist with Sauerländer Hartkalkstein-Industrie GmbH (SHI), in Bad Wünnenberg, examines the delivery once again. Using the delivery slip, he goes through the individual items and checks them off. This is routine; he has received every delivery and inspected it for years. Since April 2015 he has used a rugged tablet computer together with a small hand-held Bluetooth scanner to check the incoming goods. After 10–15 scans, he releases the goods for transfer to the blast site, presses the tablet’s display and posts the explosives in the electronic explosive stock book.
New EU directive
This new technology was introduced some six months ago throughout the whole of Mitteldeutsche Hartstein-Industrie Gruppe (MHI); the Europe-wide directive came into force a few months earlier on 5 April 2015. Since then, all companies dealing with explosives and detonators have been obliged to ensure the traceability of the products used. Alfons Planken reports that this was not initially well received in the industry and was a great cause for concern. ‘There was no opportunity to familiarize ourselves with the new system prior to its introduction and there was no time to practice, mainly because the manufacturers of explosives were not ready,’ he said.
Since 5 April 2013, all manufacturers of explosives have been obliged to label each detonator, each cartridge and each detonating cord with a unique number. It was agreed that a data matrix code would be printed on each item in addition to the alpha numerical representation. Two years later, on 5 April 2015, the ‘tracing’ obligation became mandatory for consumers too. This means that all the individual numbers must be documented upon goods receipt as well as when they are used.
To make the whole system practicable, the European explosives manufacturers established for every supply a digital delivery slip in the form of an XML file, which includes all the individual identification numbers of the explosives supplied.
Before the directive entered into force in April 2015, the theme of ‘Tracking and Tracing Explosives’ had proved highly controversial. From 2013 onwards, it was repeatedly a major theme at conferences and seminars. However, implementation did not take place. Time passed without producing any tangible results. The manufacturers did not provide digital delivery notes because, supposedly, there were no users who wanted to receive this information with the delivery. Everybody was waiting. But for what?
Development of a solution by Ontaris
At the end of 2013, Wuppertal-based Ontaris GmbH & Co. KG, in close co-operation with several quarries, mines and explosives dealers, started to develop an easy-to-use system that would be optimally matched to the application, and sought companies where practical experience could be gained.
‘Everything was new. People authorized to perform blasting in companies were not used to working with computers. Moreover, the processes, such as how digital delivery slips would be transferred from the supplier, were completely unclear. One had the feeling no one wanted to take the first step,’ said Martin Schüssler, managing director of Ontaris.
‘Our goal in developing the stock book was to create an easy-to-use system that gives complete information about the stock at all times and which does not cause any extra work.’
At the same time, MHI were seeking to address the new guidelines within the Group and were looking for a suitable supplier for implementation. Thus, in the summer of 2014 initial discussions took place with Ontaris.
MHI were quickly impressed with Ontaris’ explosives stock book. People authorized to carry out blasting in the individual facilities recommended the solution for the Group, so that introduction could take place in early 2015. Unfortunately, at that time the explosives manufacturers were not so advanced with their IT and training that they could regularly and reliably supply digital delivery slips with their shipments.
‘Due to the situation with the explosives manufacturers, an introduction phase was not feasible for us, even if it had been planned in advance. This was mainly due to the electronic delivery notes, which were not available everywhere,’ said Katharina Hermsen, executive assistant technology with MHI. ‘That took a lot of energy, and the authorized blasters barely had time to familiarize themselves with the new system before it had to be converted by April 2015.’
Return of unused explosives
Meanwhile, the explosives are ready at the Alme Stone Quarry blasting site. The holes are filled and the initiation system connected. The explosives that were not needed have been returned to the supplier’s truck. There, using the Ontaris system, Alfons Planken scans the cartons and some detonators that are going back to the supplier. One click on the stock control immediately gives him the certainty that he has carried out all bookings correctly. The inventory indicates an empty warehouse and the stock movement includes all actions performed.
Commenting on the fact that, in practice, there are always things that are not regulated by the law, Martin Schüssler of Ontaris said: ‘Nowhere is it written what I should do if I have to take explosives from the blast site back to my warehouse or return them to the supplier when the label with the barcode has become dirty or lost. We have found a very simple, practical solution for these cases. We have continually developed our system over recent months, so that our customers can work even better with it.’
Although initially extremely sceptical, Alfons Planken is very positive about his first six months using the tablet: ‘I am extremely pleased with the Ontaris system. Overall, the cost is lower, the whole thing runs faster and more easily. I don’t want the paper book anymore,’ he said.
For further information, contact Ontaris’ UK partner, Phil Robinson of Amber Valley Blasting Services Ltd, on email: avbsl@aol.com; or visit: www.ontaris.eu
- Subscribe to Quarry Management, the monthly journal for the mineral products industry, to read articles before they appear on Agg-Net.com