Cost-saving Methodology for System Control of the Drilling and Blasting Process
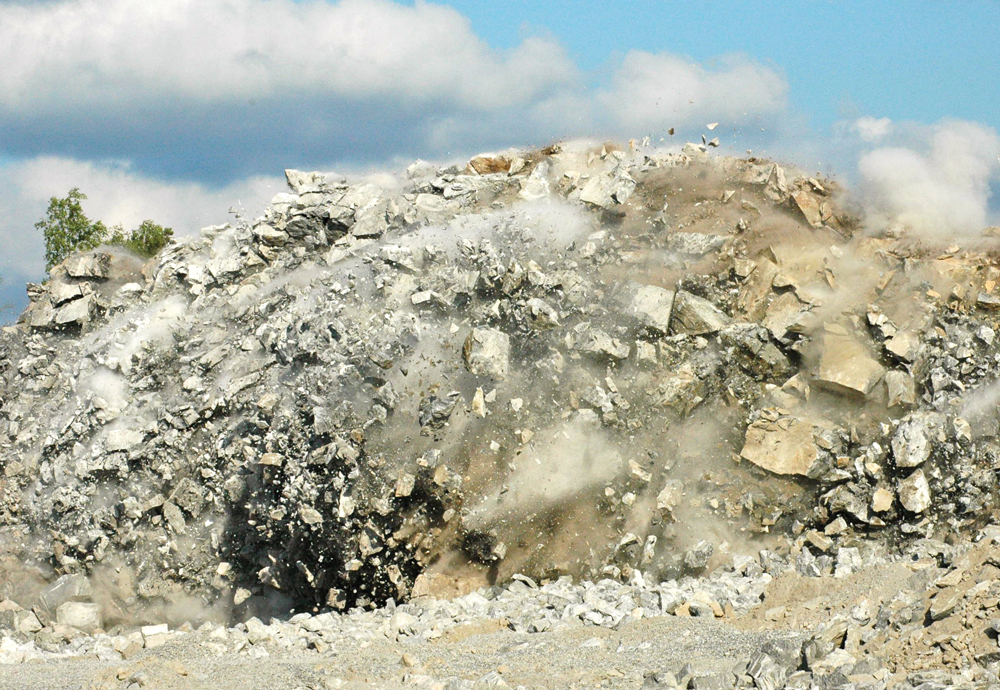
First published in the March 2016 issue of Quarry Management as Six Sigma Blasting
A new cost-saving methodology for system control of the drilling and blasting process
By Anthony Konya, Precision Blasting Services
In the past, senior management would often give a technical person such as an engineer or supervisor the task of production control and research in an attempt to develop a process control system. For example, if blasting costs were a problem, the engineer would be given responsibility for taking measurements and determining the reasons for the high cost. However, once the causes had been identified, the senior management may not have implemented the engineer’s recommendations because of a lack of understanding of the total problem. In addition, drillers and shotfirers, who were not directly involved in the process, may simply have been given orders to be more accurate in their drilling. There was usually no direct control of the drillers. In other words, the recommendations were not enforced and further evaluations were not conducted to ensure the drilling was corrected over the long term.
What this commonly used method lacks is the team approach, as well as consistent monitoring and detailed reporting. For this reason, these older methods commonly fail over the long term. It has been the author’s experience that even when problems have been identified and immediate changes made to correct them, these changes have disappeared over a matter of months or years and the operation has ended up just as inefficient as it was before the system was implemented. This is often because of changes in management, drillers/shotfirers, supervisors etc, and no follow-up or control on the process. The Six Sigma blasting programme focuses on a team made up of all levels, from upper management to the driller and shotfirer, to ensure co-operation and effective completion and control of the process; along with consistent monitoring and reliable, timely reporting.
Six Sigma is a manufacturing term that is used to describe a very specific continuous improvement process. This process involves system inputs and outputs, determining customer needs, and developing ways to ensure that all outputs of the system are similar while utilizing a team approach. In Six Sigma processes, two main statistics are used to determine the success of the system; the system mean and the system standard deviation.
Precision Blasting Services have been studying the process of drilling and blasting to help identify variables that can be systematized to ensure a constant blasting operation. For its own Six Sigma blasting programme, the company has found ways to correct the most common problems that quarries and mines encounter when drilling and blasting, including: drill angles, drillhole drift, geological variation, and other factors.
The Six Sigma DMAIC methodology works well as a roadmap for Six Sigma blasting. This methodology begins by defining the requirements and goals, as well as key milestones, project leads, and project deliverables. The next step is the measure phase, which involves collecting the data needed to determine the current blasting programme opportunities. These can be either problems that are occurring or areas that can be improved for better results. The next phase is analyze, which takes a deeper look at the measurables collected and determines the opportunity areas that exist in a blasting programme. The next step is the improvement phase, which develops potential solutions and assigns the failure measures for the programme. At the end of this phase these changes are incorporated into a blasting programme and mark the start of the control phase. In this phase the standards for the new system are developed to ensure system failure does not occur and to determine the true process stability.
In the drilling and blasting sector a great deal of time is spent considering the efficiency of drills, new products, and better explosives. What is rarely considered is the system control aspect. In one case, a US mine saved $100,000 a year through product optimization. When this same mine developed a Six Sigma blasting programme it saved more than $400,000 a year. Below is the way that Precision Blasting Services administer this process.
Define phase
During the define phase, one of the most important steps is to identify the true outcomes and requirements of the programme. This could be a more uniform fragmentation size, a reduction in drilling and blasting costs, a reduction in vibration levels, or more tons per shot.
The next important part of this phase is to put together a team that will implement the Six Sigma blasting process. In general, the team should consist of managers, engineers, engineering technicians, and the drillers and shotfirers. This ensures co-operation at all levels and begins the discussion on blasting system control.
After the team has been formed jobs need to be defined for each member. There should be a mixture of: sponsor (executive who will be sponsoring the programme), leader (person responsible for implementing and guiding the team), black-belt member (usually an expert in drilling and blasting who will identify opportunities and solutions), green-belt members (the people gathering data, helping with analysis, and suggesting solutions), and team members (those assisting the team and helping to implement the solutions). This team will meet on a scheduled basis (bi-weekly, monthly, quarterly etc) and smaller groups within the team will meet on a more frequent basis.
The next step is to develop a process map of the operation to ensure everyone understands the process in place, areas for development, and the end goals of the programme.
Measure phase
In the measure phase the black belt and green belts will begin to take measurements throughout the blasting programme. These should include both the inputs and the outputs. In a complex blasting programme, it can be difficult and time consuming to measure all the different variables. This makes it important to know the end goal and to ensure the black belt has a deep understanding of drilling and blasting.
A few key inputs and main outputs will be defined and measured. A list to assist in some important first-step areas is provided here:
This step also marks the beginning of the collection of baseline data that will measure the success of the programme. It will generally take from one to three months to ensure good, consistent baseline data are collected and accurate inputs are matched.
Once the exact inputs and outputs have been designated, monitoring of these continues and a more defined measure phase begins. In order to prevent overwhelming anyone collecting the data, generally only a few inputs and outputs are measured over the long term. This also ensures that the relationship can be tracked more accurately.
For example, considering fragmentation size (using the WipWare size distribution analysis; figs 3 & 4) as the main output objective and burden, spacing and drill depths as the main inputs, these will be tracked and analyzed to form a relationship for future models.
Analyze phase
The analyze phase will be ongoing concurrent with the measure phase and will take the results from the measure phase and begin to construct the relationships and models. Some helpful tools in this phase will be: using and updating process flows and maps, histograms, Pareto charts, scatter plots, and other forms of statistical analysis.
These tools will be used to develop specific relationships between the inputs (x) and outputs (y). These can be fitted to a Y=f(x) relationship that can be linear, logarithmic, exponential, or one of a variety of other relationships. In a theoretical example, it was found that face advance in coal mining with undercut blasting methods was related with undercut depths by:
Face advance = Undercut depth + 16cm
It was also found that the drill depth (especially drilling farther than the undercut depth) had almost no effect on the face advance and that this was an area for economic improvement by reducing the total drill depth and explosives used. The unnecessary drilling and explosive use were then considered economic losses per ton (fig. 6).
After development of these relationships, the next step would be to determine why the undercut depths where not always at the designed level.
Improve phase
After achieving a consistent baseline (1–3 months) from the measure phase and the development of relationships in the analyze phase, the improvement phase will begin. In this phase model adjustments and specific designs will be constructed. In the previous example (face advance with undercut and drill depth) an employee was asked to take extra care to undercut by a set 4.4m and the drillers drilled shorter holes (4.2m horizontally). The process was then carefully examined and the results showed that the face advance still followed the previous equation; this reduced drilling by more than 8,000m per month along with the subsequent explosive cost associated with loading the additional 8,000m.
After the design and testing phase, implementation of the new systems and identification of scenarios that could lead to failure of this system will be conducted.
Control phase
The last phase of the Six Sigma blasting process is the control phase. Here, periodic monitoring of the inputs will be undertaken with the results graphed on quality-control charts. This will ensure that the systems created are meeting the designed goals. Standards and procedures (SOPs) will then be developed to ensure that these processes are easily trainable and followed.
The next part of the control phase will be to develop a total cost savings and transfer plan which can be given to the process owners. For example, if drillhole depth is a problem, at the end of the Six Sigma blasting process the drillers would begin taking their own depth readings and be periodically checked by supervisors or engineers.
After the transfer is complete the project is officially finalized and closed. Following this step, the process can be reinitiated to look at other variables or the Six Sigma initiative can be terminated.
Conclusion
Six Sigma blasting is a new methodology for system control of the drilling and blasting process in mines and quarries. Using a DMAIC method to analyze and correct key inputs in order to achieve desired outputs, the Six Sigma blasting process has saved some sites in excess of US$400,000 a year by looking into areas that, traditionally, have not been considered. Precision Blasting Services can help ensure that a operator’s Six Sigma blasting process is being run effectively and that the desired results are being obtained.
- Subscribe to Quarry Management, the monthly journal for the mineral products industry, to read articles before they appear on Agg-Net.com