New CDE plant for Creagh Concrete
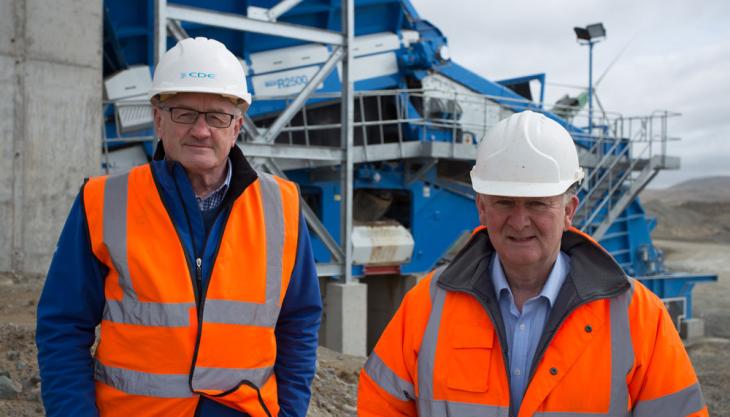
R2500 feeding and screening system helps tackle problematic conglomerate deposit
CREAGH Concrete, a long-term CDE customer from Northern Ireland, have added a CDE R2500 feeding and screening system and an additional AggMax log-washer to their existing installation at Draperstown, to help tackle a difficult conglomerate material even more efficiently and rapidly than before.
A percentage of Creagh’s products are generated from this challenging raw feed, which comprises conglomerated aggregates, sands and silts in equal proportions, and underlies the company’s main sand and gravel deposit.
Previously, difficulties in processing the conglomerate had been partially overcome through the installation of a CDE AggMax modular log-washer, which was able to recover approximately 70% of the material, including top-quality natural sand.
However, after three years of successful production, Creagh Concrete decided to further increase their capacity by tackling additional issues.
Willie Doherty, the director responsible, explained: ‘Whilst we were very happy with the previous outcome, there remained some issues that we felt we wanted to address to further improve our production facility.
‘Some extensive areas of the pit contain what is effectively a compacted conglomerate which has to be ripped from the face using an excavator. The original feed hopper was specifically designed by CDE to handle sticky material when wet. This was fed by loading shovel from material that had been pre-screened and crushed in the pit.
‘It proved necessary to crush the conglomerate to reduce it to a size suitable for processing, thereby preventing any large oversize from blocking the hopper. Originally this was done at the face, but the process required the use of a mobile crusher followed by a mobile screener. We also wanted to avoid double handling and use dumpers to feed the plant and increase efficiency.’
The solution came with the introduction of a CDE R2500 feeding and screening system, which made the use of 40-tonne dumptrucks possible and eliminated the need to use shovels for transport from the pit.
The R2500’s apron feeder can handle even the most difficult of feed materials, and the heavy-duty P2-75 Infinity screen that forms part of the R2500 removed the need for a mobile screener at the face.
Additionally, after consulting with CDE, it was agreed that the plant layout should be redesigned so that Creagh’s existing jaw crusher could be incorporated into the feed arrangement, to remove the need for a mobile jaw crusher at the face. Crucially, double handling has now been taken out of the equation.
Moreover, a second AggMax 251 was incorporated into the washing circuit and is now used to break up the conglomerate and release the sand, which is then removed before the aggregates are sent to the original log-washer for even more efficient scrubbing.
With the new upgrade in place, Creagh currently process up to 150 tonnes of raw feed per hour. A variable-speed drive unit has been fitted to the first AggMax log-washer to accommodate any variations in the feed rate.
Commenting on Creagh’s decision to tackle all available feed material more efficiently, Des Crawford (left of photo), Northern Ireland area sales manager for CDE, said: ‘With planning permission for new deposits of sand and gravel being so difficult to attain, it is extremely important to gain maximum production from existing resources.’
According to quarry manager Colm Scullion, the latest innovations should extend the life of the quarry by at least 10 years, while CDE say Creagh’s installation represents a landmark in terms of engineering innovation and design solutions, allowing the company to tackle the most challenging materials and produce high-quality products with minimum waste.